Yaskawa P7B Drive Bypass User Manual
Page 48
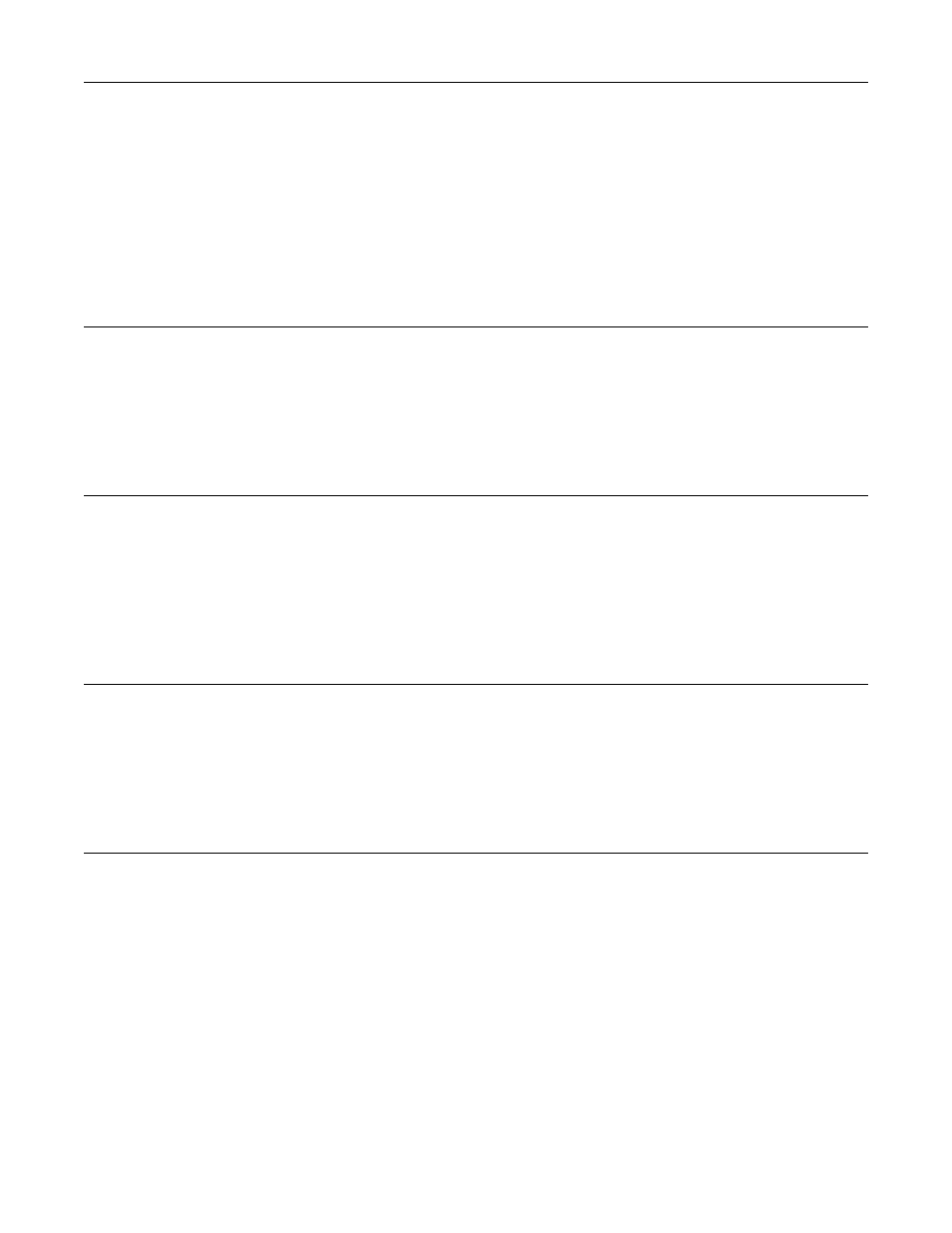
Electrical Installation 2 - 10
!
Damper Control Circuit
TB1 terminals 19 and 20 are provided to power a customer supplied 120 VAC relay, electric actuator or electro-pneumatic
solenoid air valve employed to control a pneumatic damper actuator, typically for outdoor air intake damper interlock. The
power rating of the connected device should be no more than 40 VA continuous and 70 VA inrush. An off command (from the
H/O/A switch) or a safety device trip-out will immediately de-energize these terminals. At the same time the Drive will begin
the ramp to stop process (in Drive mode with the default stopping method). In some air handling unit applications operation
during the ramp to stop time with the dampers closed may be problematic. Over pressurization of ducts or trip-out on high DC
bus voltage, due to overhauling of the load by other fans in the system, are possible outcomes. One solution is to reprogram the
stopping method in parameter b1-03 to “coast to stop” eliminating the potential for both of these problems.
!
Customer Supplied Run/Stop circuit:
A control terminal block position (TB1, terminals 3 and 4) is provided to connect the Normally Open (NO) Run/Stop contact
from a separate source or other remote controller
for auto mode control.
There must be continuity between these terminals in order for the motor to run.
!
Safety Interlock Circuit:
A control terminal block position (TB1, terminals 1 and 2) is provided to connect the series circuit of Normally Closed (NC)
safety devices such as: freeze up thermostats, smoke/fire sensors, high pressure limits, temperature limits or vibration
detectors.
There must be continuity between these terminals in order for the motor to run.
!
Customer Supplied Interlock Circuit (Drive and Bypass enable input):
A control terminal block position (TB1, terminals 5 and 6) is provided to connect Normally Open (NO) enabling contacts such
as: damper end switches or occupied cycle timers.
There must be continuity between these terminals in order for the motor to run.
!
Switch Selectable Functions:
The slide switches used to select these functions are located on the relay controller Printed Circuit Board (PCB) A2
(See Figure 1.9). The factory default is for these functions to be de-selected.
Smoke Purge: When enabled (switch S105) this function allows a contact closure, between terminals 17 and 18 of TB1, to
transfer motor operation to bypass for a maximum capacity smoke control function. When in smoke purge mode, during
emergency fire/smoke situations, the motor overloads and safety interlock circuit are overridden to shift the priority to
protecting people rather than equipment.
Remote Transfer to Bypass: When selected (switch S104) this function allows a contact closure from a separate source,
between terminals 25 and 26 of TB1, to transfer motor operation from Drive mode to bypass mode. This remote tranfer to
bypass function overrides the Drive/Bypass manual switch.