Class 2 functionality, Commissioning diagnostics, Scaling function control – HEIDENHAIN PROFIBUS-DP (DPV0) User Manual
Page 34
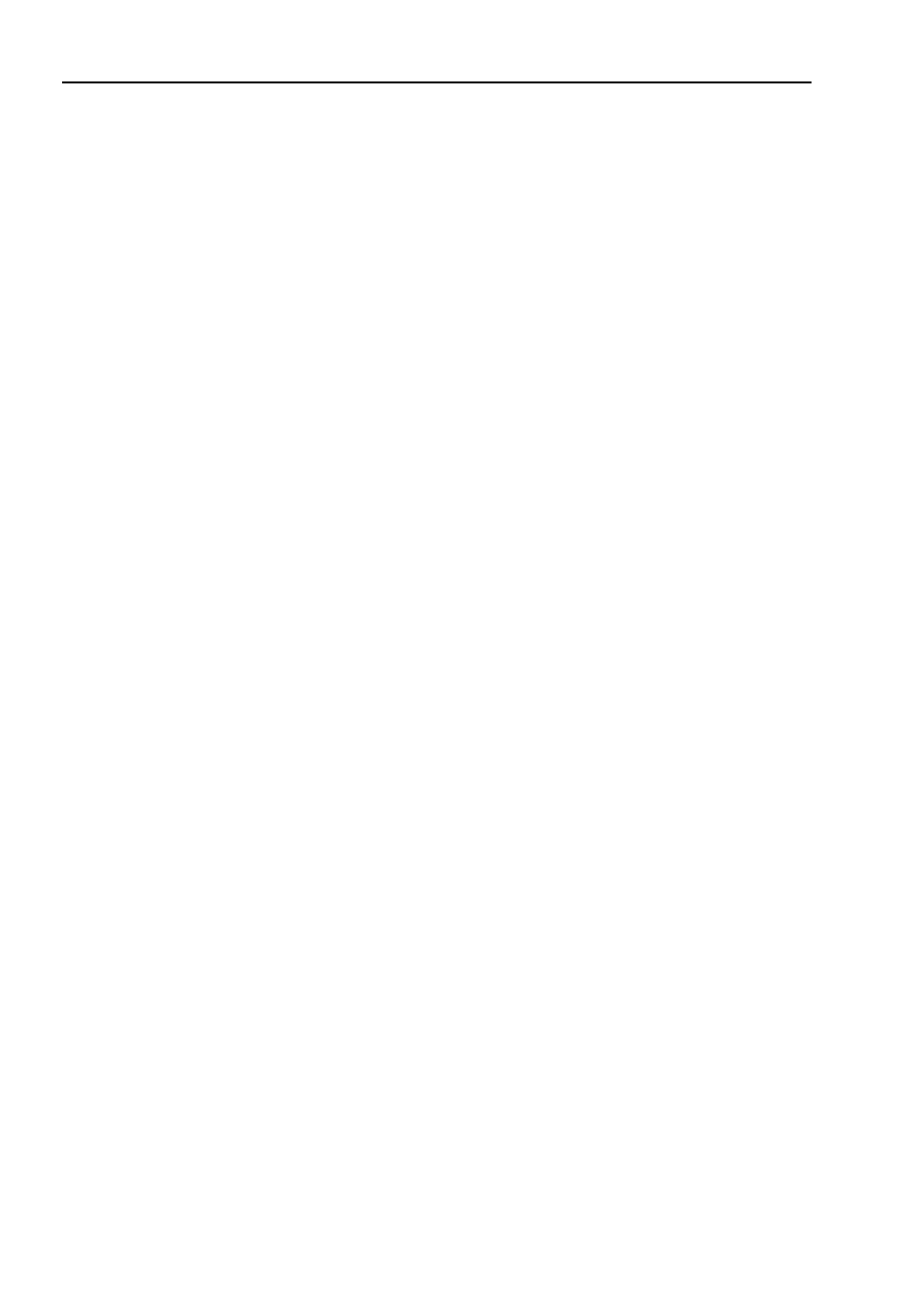
Encoder and Gateway functionality, DPV0
34
5.4.1
Code sequence
The code sequence defines whether the absolute position value
should increase during clockwise or counter clockwise rotation of
the encoder shaft seen fromflange side. The code sequence is by
default set to increase the absolute position value when the shaft
is turned clockwise (0).
Note:
The position value will be affected when the code
sequence is changed during operation. It might be
necessary to perform a preset after the code
sequence has been changed.
5.4.2
Class 2 functionality
This bit enables or disables class 2 functionality. The Class 2
functionality bit for PROFIBUS-DP devices is by default disabled
(0). This means that this control bit must be activated during
parameterization in order to support the class 2 functions.
Note:
If a class 1 device uses some optional class 2
functions, the class 2 control bit must be set.
5.4.3
Commissioning diagnostics
The commissioning diagnostics function makes enable the device
to perform internal diagnostic test of the encoder components
responsible for position detection during a standstill of the
encoder (i.e. light unit, photovoltaic cells etc.). In conjunction
with the position alarms, it enables thorough checking of
whether the position values provided by the absolute encoder
are correct. The commissioning diagnostics function is started
by the commissioning bit in the operating parameters. If an
error is found within the absolute encoder, this is indicated in
the diagnostic function by the commissioning diagnostics
alarm bit (see chapter 5.6.2).
The commissioning diagnostics function is an option. To find out
whether the device supports commissioning diagnostics, the
“operating status” should be read by the diagnostic function
and the commissioning diagnostics bit should be checked.