Fundamentals of thread milling – HEIDENHAIN iTNC 530 (340 422) User Manual
Page 302
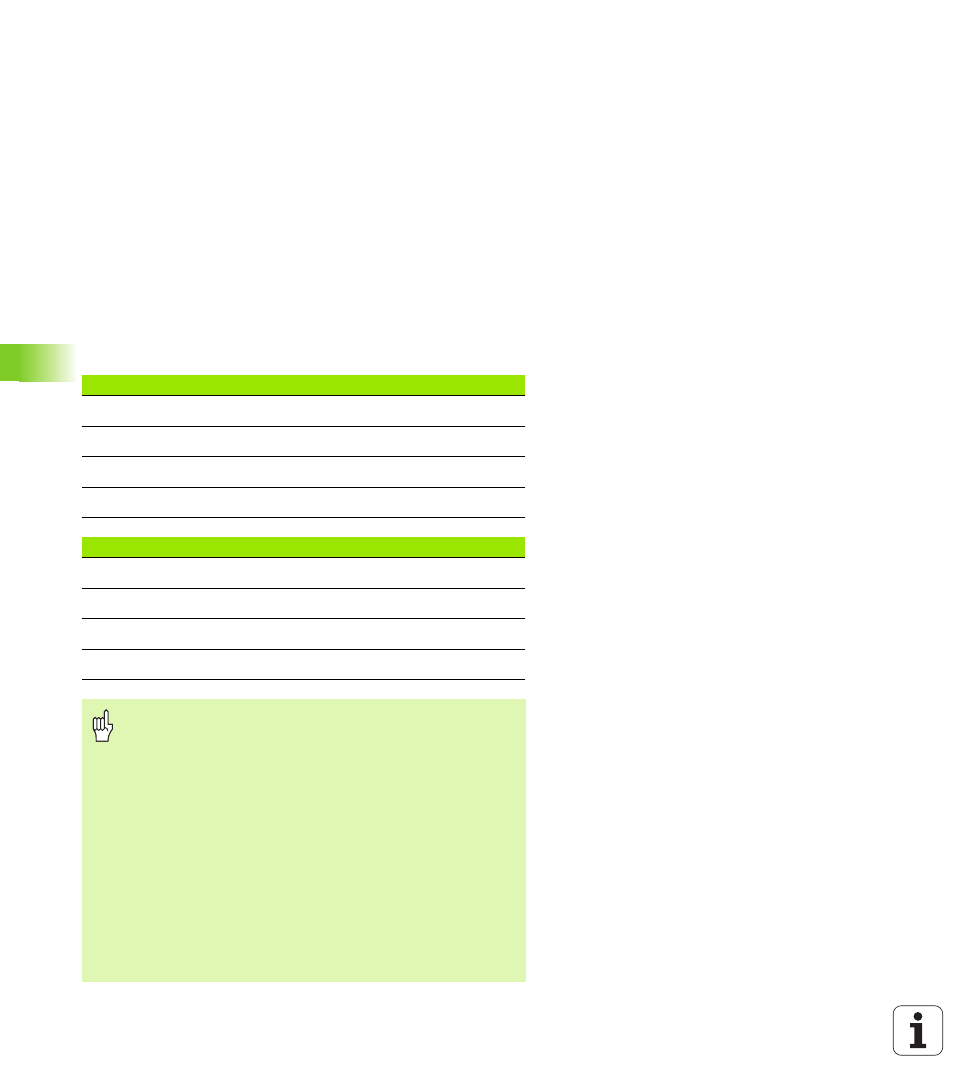
302
8 Programming: Cycles
8.3 Cy
cles f
o
r Dr
illing, T
a
pping and Thr
ead Milling
Fundamentals of thread milling
Prerequisites
Your machine tool should feature internal spindle cooling (cooling
lubricant at least 30 bar, compressed air supply at least 6 bar).
Thread milling usually leads to distortions of the thread profile. To
correct this effect, you need tool-specific compensation values
which are given in the tool catalog or are available from the tool
manufacturer. You program the compensation with the delta value
for the tool radius DR in the tool call.
The Cycles 262, 263, 264 and 267 can only be used with rightward
rotating tools. For Cycle 265 you can use rightward and leftward
rotating tools.
The working direction is determined by the following input
parameters: Algebraic sign Q239 (+ = right-hand thread / – = left-
hand thread) and milling method Q351 (+1 = climb / –1 = up-cut).
The table below illustrates the interrelation between the individual
input parameters for rightward rotating tools.
Internal thread
Pitch
Climb/Up-cut
Work direction
Right-handed
+
+1(RL)
Z+
Left-handed
–
–1(RR)
Z+
Right-handed
+
–1(RR)
Z–
Left-handed
–
+1(RL)
Z–
External thread
Pitch
Climb/Up-cut
Work direction
Right-handed
+
+1(RL)
Z–
Left-handed
–
–1(RR)
Z–
Right-handed
+
–1(RR)
Z+
Left-handed
–
+1(RL)
Z+
Danger of collision!
Always program the same algebraic sign for the infeeds:
Cycles comprise several sequences of operation that are
independent of each other. The order of precedence
according to which the work direction is determined is
described with the individual cycles. For example, if you
only want to repeat the countersinking process of a cycle,
enter 0 for the thread depth. The work direction will then
be determined from the countersinking depth.
Procedure in case of a tool break
If a tool break occurs during thread cutting, stop the
program run, change to the Positioning with MDI
operating mode and move the tool in a linear path to the
hole center. You can then retract the tool in the infeed axis
and replace it.