2 troubleshooting, 3 cleaning rules, 2 troubleshooting 16.3 cleaning rules – ARAG GCS 3200 User Manual
Page 41: Maintenance / diagnostics / repairs
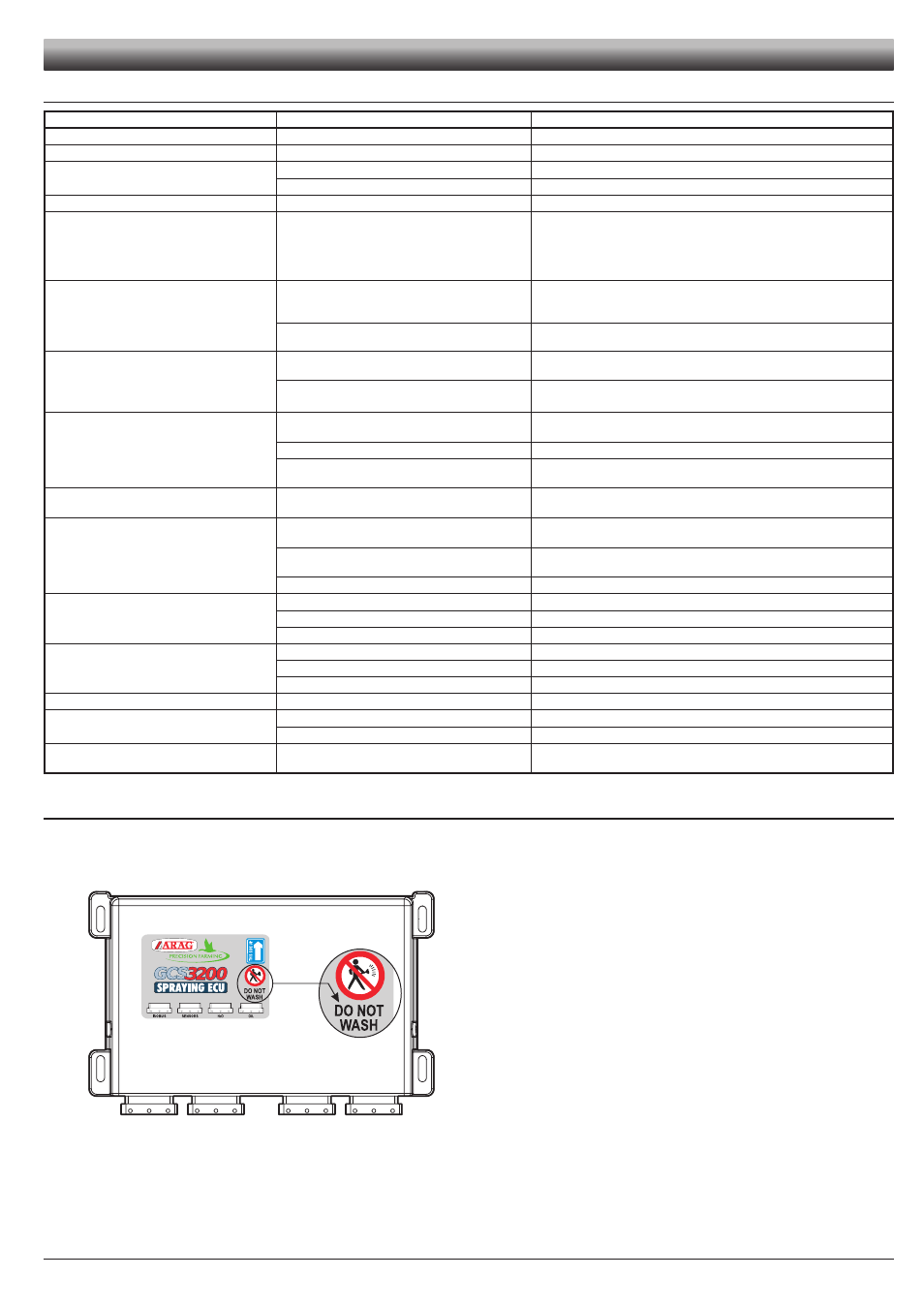
41
16.2
Troubleshooting
fault
cause
reMedy
Valve controls take no effect
Valves not connected
• Connect the IN-CAB cable
(Chapter 9).
One valve does not open
No power supply to valve
• Check valve electric connection and operation.
The display no longer shows the speed
Wrong setup
• Check the setup of the wheel constant
(Par. 13.1).
No signal coming from the speed sensor
• Check connections to speed sensor
(Par. 8.4).
The displayed speed is not precise
Wrong setup
• Check the setup of the wheel constant
(Par. 13.1).
Output volume readout inaccurate
Wrong setup
• Check boom width setting
(Par. 12.4).
• Check the setup of the flowmeter constant
(Par. 12.6).
• Check the setup of the wheel constant
(Par. 13.1).
• Check the setup of the section valve type
(Par. 12.5).
• Check connections to speed sensor
(Par. 8.4).
Sprayed surface displayed does not match
actual sprayed surface
Wrong setup
• Check boom width setting
(Par. 12.4).
• Check the setup of the wheel constant
(Par. 13.1).
• Check connections to speed sensor
(Par. 8.4).
Covered area count not reset
• Reset counter.
(Par. 14.2.1).
Distance traveled count displayed does not
match actual distance covered
Wrong setup
• Check the setup of the wheel constant
(Par. 13.1).
• Check connections to speed sensor
(Par. 8.4).
Distance travelled count not reset
• Reset counter
(Par. 14.2.1).
Sprayed fluid count displayed does not match
litres/gpm actually sprayed
Wrong setup
• Check the setup of the flowmeter constant
(Par. 12.6).
• Check the setup of the section valve type
(Par. 12.5).
Distance travelled count not reset
• Reset counter
(Par. 14.2.1).
Three-way section valves in use, but no backflow
calibration
• Perform calibration.
Time count displayed does not match actual
time worked
Work time count not reset
• Reset counter
(Par. 14.2.1).
Spray volume set for automatic operation
cannot be achieved
Wrong setup
• Check spray rate setup
(Par. 13.2).
• Check boom width setting
(Par. 12.4).
System not adequately sized to provide required
rate
• Check maximum pressure valve setting.
• Make sure control valve is adequate for specific system.
Control valve malfunction
• Check valve operation.
Instantaneous pressure readout inaccurate
Wrong setup
• Check pressure sensor full scale setting
(Par. 12.7).
Pressure sensor not calibrated
• Perform calibration
(Par. 14.3).
Pressure sensor improperly installed
• Check connections to pressure sensor
(Par. 8.4).
Instantaneous pressure not displayed
Wrong setup
• Check pressure sensor setting
(Par. 12.7).
Computer receives no signals from speed sensor
• Check connections to pressure sensor
(Par. 8.4).
Pressure sensor improperly installed
• Check connections to pressure sensor
(Par. 8.4).
RPM readout inaccurate
Wrong setup
• Check RPM sensor constant setting
(Par. 12.11).
RPM not displayed
Computer receives no signals from RPM sensor
• Check connections to RPM sensor
(Par. 8.4).
RPM sensor improperly installed
• Check connections to RPM sensor
(Par. 8.4).
Pump failure alarm permanently active
Computer receives no signals from Pump
Protector sensor
• Check connections to Pump Protector sensor
(Par. 8.4).
Tab. 11
16.3
Cleaning rules
- Clean only with a soft wet cloth.
- DO NOT use aggressive detergents or products.
- DO NOT use water jets to clean the monitor and the control unit.
Fig. 101
MAINTENANCE / DIAGNOSTICS / REPAIRS