Hypertherm HT2000-200 Volt User Manual
Page 158
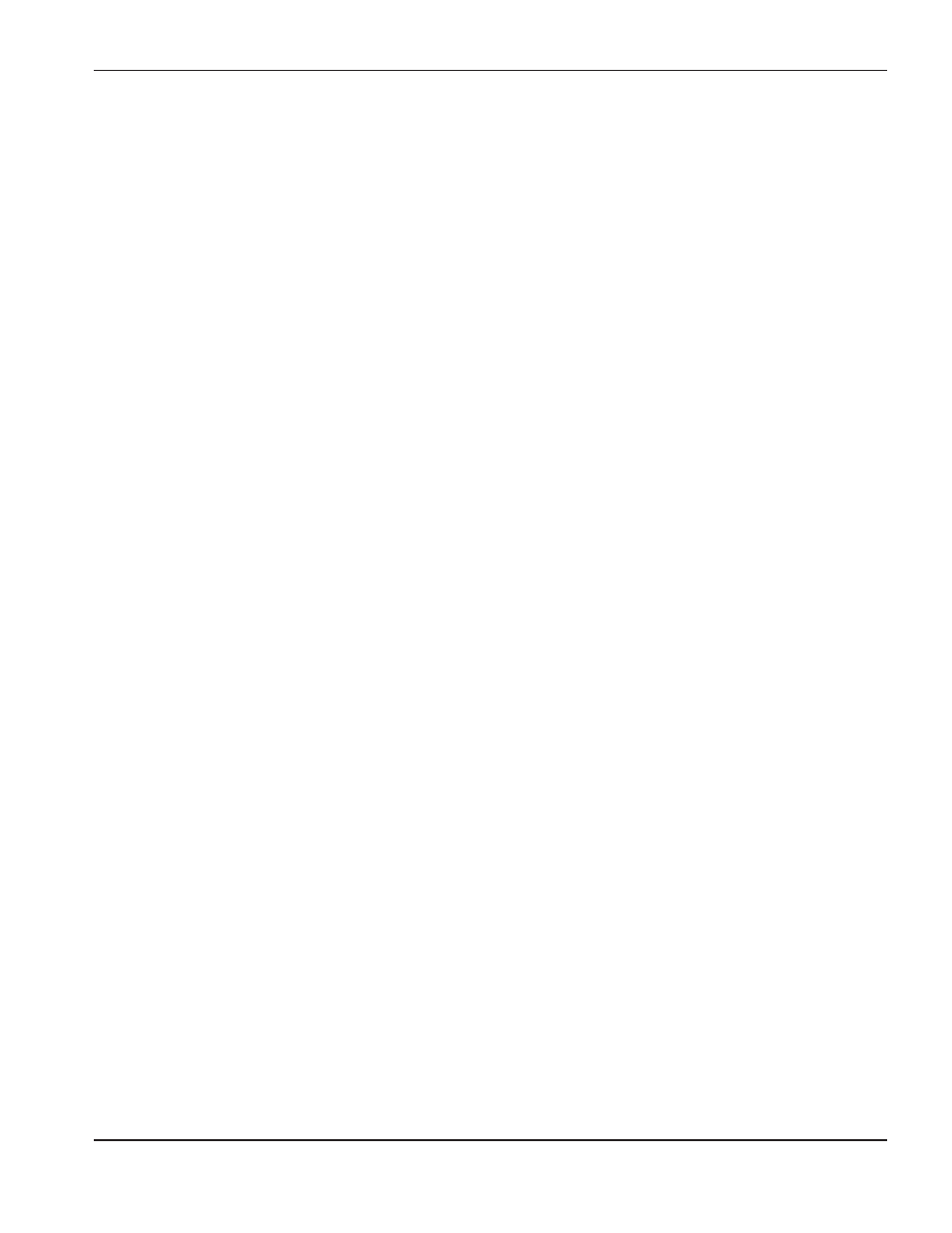
MAINTENANCE
HySpeed HT2000
Instruction Manual
8-13
19
Problem
Possible Causes
/ Solutions
If there is no 120VAC, check pins, connectors and
associated wiring from CON1 to PCB4.
• If wiring is OK, PCB4 or PCB2 may be defective.
See
Section 10
for location of the relay that controls main
contactor CON1.
• If CON1 is getting 120VAC from the relay board as
described above, measure the voltage between
secondary terminals of main transformer T2 after the
START command is given. See Figure 9-3 for location of
T2. The voltage between any two of the three points
connected to each chopper should be equal to 200VAC.
If there is no voltage at any of the above points, replace
CON1.
If there is voltage at some but not all of the above points,
check wiring and connections to and from T2. If wiring
checks out OK, return to
Initial Checks
section and repeat
steps 1-5.
5.4. Choppers are defective or not functioning.
See
Chopper Module Test Procedure
later in this section.
6. The unit stops cutting during cut, or
cuts poorly.
6.1. The work cable is not connected or it is broken.
Connect or repair the work cable.
6.2. Arc not transferring to workpiece.
Check work cable connection to workpiece. Good contact
must be made in order for the arc to transfer.
6.3. There is insufficient air or gas pressure.
Check gas inlet pressure and the plasma and shield gas
pressures in TEST and RUN modes as specified in the
Cut
Charts.
6.4. Torch is getting insufficient current.
Check the arc current setting in the
Cut Charts
for the type
and thickness of metal you are cutting.