AMETEK PLA-PLW User Manual
Page 49
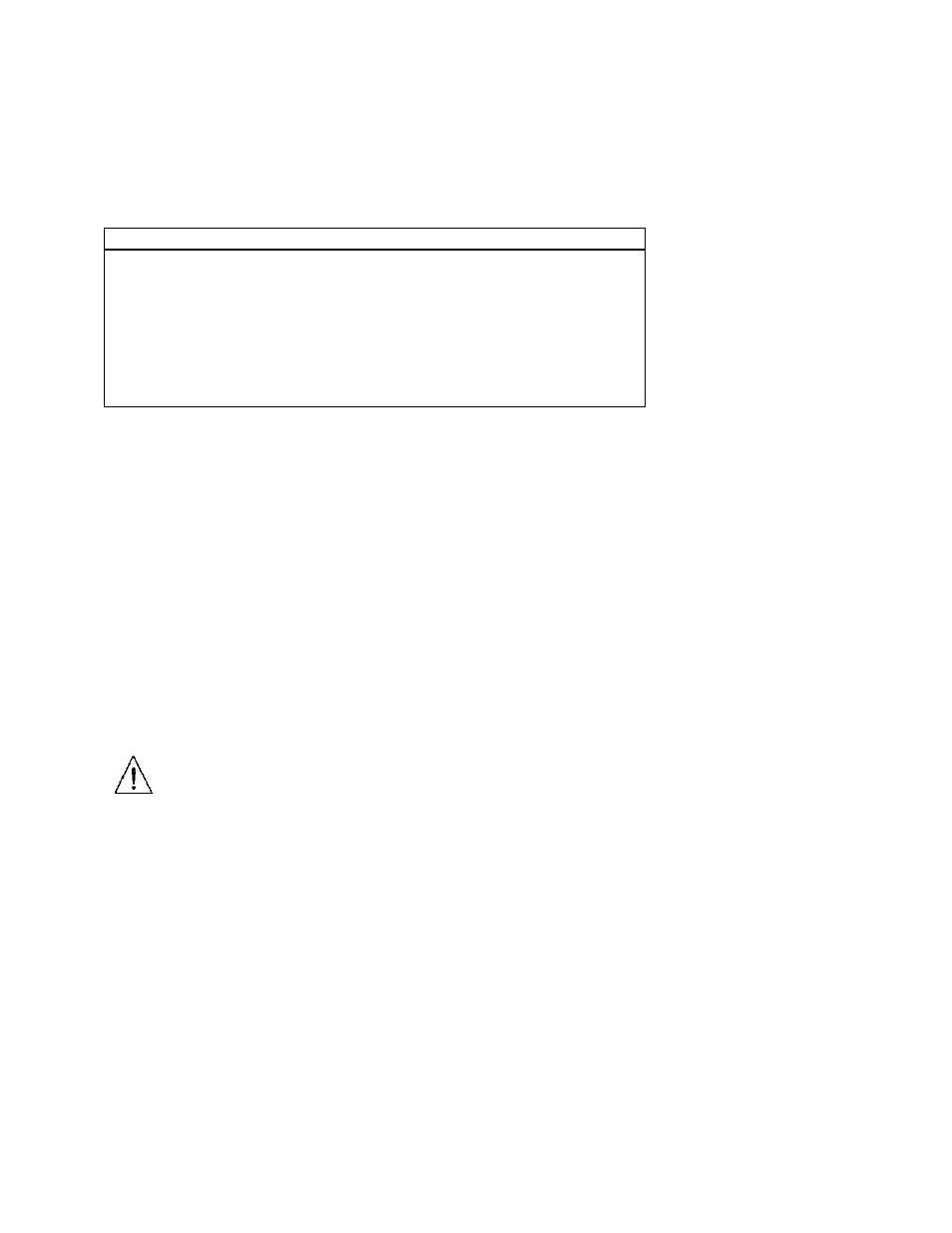
LOAD WIRING LENGTH FOR OPERATION WITH SENSE LINES
For applications that use remote sensing, you must limit the voltage drop across each source line. The eLOAD must be
supplied with the minimum operating voltage or compliance voltage for normal regulation and the voltage drop across the
cables should be accounted for. We recommend that you use the larger load wiring or ensure a smaller voltage drop (1V
typical max.) along the wire, although the remote sensing will accommodate voltage drops up to 1% of V
MAX
in each line.
Please see the following table:
Max Rated Voltage
Max Voltage Drop Compensation
100 V
1 V
200 V
2 V
300 V
3 V
400 V
4 V
500 V
5 V
600 V
6 V
700 V
7 V
800 V
8 V
TABLE 2.6 VOLTAGE DROP COMPENSATION
NOISE AND IMPEDANCE EFFECTS
To minimize noise pickup or radiation, use shielded pair wiring or shortest possible length for source wires. Connect the
shield to the chassis via a rear panel mounting screw. Where shielding is impossible or impractical, simply twisting the
wires together will offer some noise immunity. When using local sense connections, the user must use the largest
practical wire size to minimize the effects of load line impedance on the regulation of the load.
LOAD CONNECTIONS
The eLOAD is designed with an air-cooling/water-cooling system that provides airflow/water flow through the heat sink
to remove the heat generated by the Power MOSFETs. To obtain efficient heat exchange rate between heat sink and
power MOSFETs, the user needs to follow the instruction outlined below to ensure the heat is removed from heat sink
properly to prevent excess heat from accumulating in the power module. Under high power handling applications or
increased temperature operation, heat dissipation becomes a key factor in determining the reliability of the overall unit.
INPUT TERMINAL
For the safety of personnel and to prevent electrical shock due to high voltage, do not come in contact or obstruct the
input terminals. Refer to the next page diagram, for the location of the input terminals.
Observe the maximum current handling capability of the power cables from DUT to the Load Bank. Please refer to Table
2.4 for higher current rating cables. Observe the maximum input current and voltage of the terminals. Do not underrate
the cable, excessive current will cause the temperature to increase and cause melting of the insulation rubber of the
terminal and cable insulation sleeves resulting in input cable shorts.
For the high current applications, large diameter power cables are necessary to prevent load oscillation. The power cables
should be as short as possible to reduce inductance from the power cable and cause oscillation between power sources and
the load unit.
CAUTION
2-9