Ntellisys, Daptive, Ressure – Nor-Cal Intellisys Adaptive Pressure Controllers User Manual
Page 17: Ontrollers, 0 - rs-232 serial interface and commands
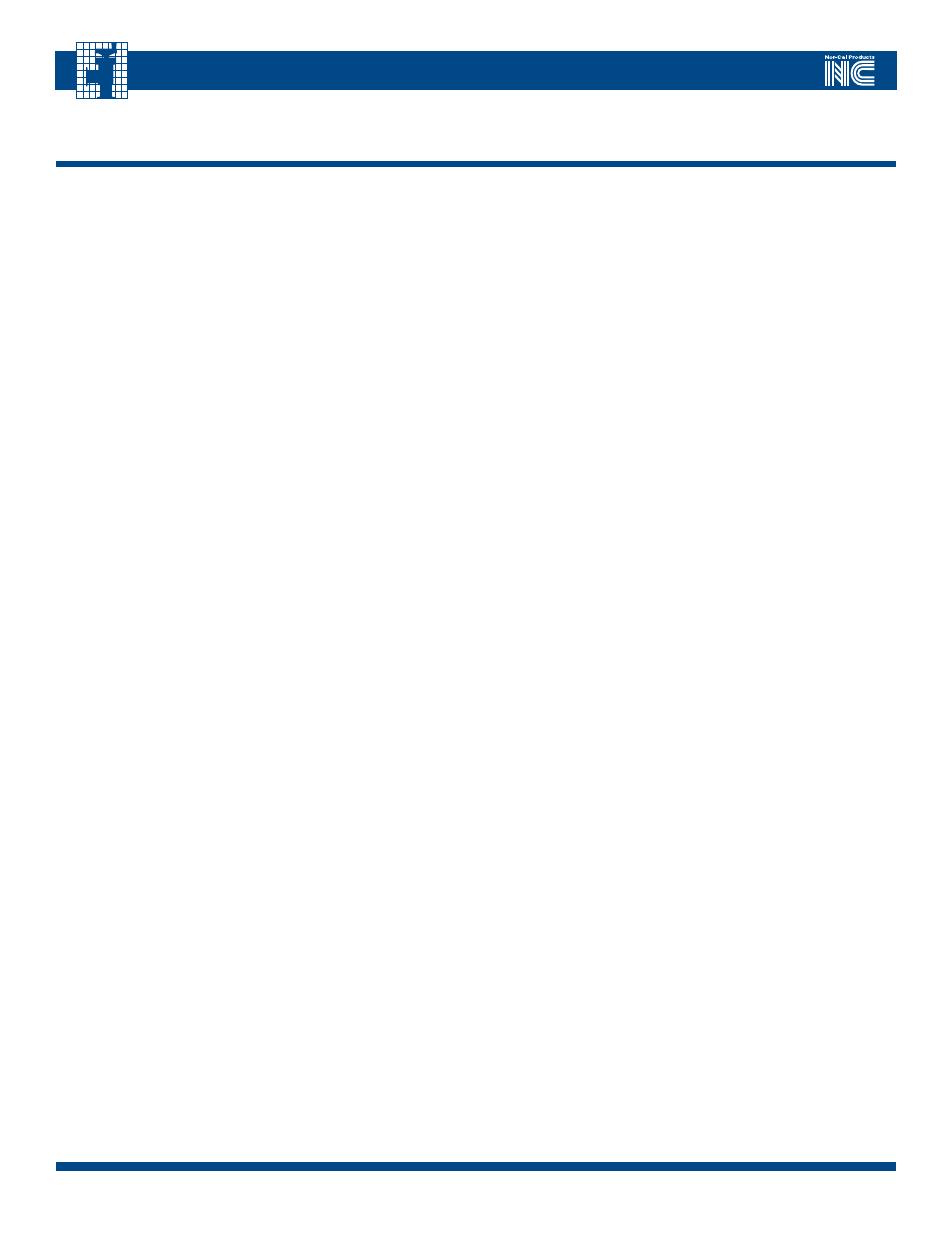
17
Call toll free
800-824-4166
or 530-842-4457
•
FAX 530-842-9130
I
ntellIsys
A
dAptIve
p
ressure
C
ontrollers
APC-OP-LIT 1/12
Modifying the Setpoint
The APC controller normally has five programmable set point selectable
to be either pressure control or valve position control. Before using the set
point to control either pressure or valve position, the set point value must
be programmed. This is done by the following command:
S1xx.xx
where xx.xx is a number from 0.00 to 100.00.
One or no decimal places may also be used i.e. x.x or x.
Reading the Setpoint
The set point can be read back to the Host
controller only through the serial port.
R1
To verify the set point
The IQ controller will respond with
S1+xx.xx
where xx.xx is the set point value.
Selecting Valve Position Control or Pressure Control
The set point input value is common for both valve position and pressure
control. Therefore, it is necessary to program the APC so that it controls
to the correct type. The factory default setting is pressure control.
To assign the set point control type and source,
send the following commands:
TØØ
Analog STPT input, position control
TØ1 (T02, T03, T04, T05)
Digital STPT 1 (2, 3, 4, or 5 if present), postion control
T1Ø
Analog STPT input, pressure control
T11 (T12, T13, T14, T15)
Digital STPT 1 (2, 3, 4, or 5 if present), pressure control
Verifying the Control Mode
Before starting either pressure control or position control operations it
might be necessary to verify the setting of the set point type. This can
only be accomplished through the serial port with the command
R25
Analog STPT
R26
The IQ controller responds with:
T1x
where x is Ø for position control or 1 for pressure control (default).
How to Control Valve Position
One of the two main functions of the APC controller is Valve Position Control.
In this mode the APC controller will simply move the throttle valve plate to a
prescribed position according to a set point. The set point is a value between
0% and 100%, where 0% is closed and 100% is open.
OPEN:
The serial command is
O
.
The controller will only respond by opening the valve.
CLOSE:
The serial command is
C
.
The controller will only respond by closing the valve.
hOLD:
The serial command is
h
. The controller will
only respond by stopping the valve at the current position.
Any Valve Position:
Vxx.xx
where xx.xx is a number from
0.00 to 100.00% of full open. One or no decimal places
may also be used i.e. x.x or x.
Similarly use the
T1Ø
command to set the set point type to position control.
Then follow the information outlined in the How To Modify the Setpoint and
How To Control System Pressure sections.
Reading the Valve Position
The valve position may also be obtained through the serial port.
The valve position is reported as a % of full open using the command:
R6
The Controller responds with the valve position using the format:
Vxx.xx
where xx.xx is a number from 0.00 to 100%
of valve open position.
How to Control System Pressure
The principal function of the APC controller is to control system pressure.
To accomplish this, the APC controller needs to be put in “pressure control
mode” while being supplied a pressure set point. The pressure set point is
proportional to the vacuum gauge’s full scale range.
Controlling pressure using the serial port provides additional flexibility.
To activate a set point issue the command:
D1
The active set point must be set to the correct value before activating the
pressure control set point. The set point can be modified any time before, dur-
ing, or after pressure control. Also a different set point can be activated
at any time.
Reading System Pressure
Pressure, as output by the system gauge(s) to the APC Controller,
can be read directly from the controller. Both the signals from
CDG1 and CDG2 can be read independently.
The APC controller will report the pressure via
the serial port with the following command:
R5
The controller will respond with:
P+xx.xx
where + indicates the polarity of
the value and xx.xx is a value.
The range of xx.xx is typically from 0.00 to 100.00 and represents the pressure
as a percentage of the full scale of the pressure gauge. The value can be less
than 0 if the vacuum gauge electronics have drifted or greater than 100 but
limited to 101.5%. For example, it the system uses a 100 Torr gauge and the
pressure is actually 10 Torr, the controller response will be P+10.00. On the
other hand, if the pressure is 10 Torr but the system has a 20 Torr gauge, the
controller response will be P+50.00.
When two CDG’s are used, the APC controller will always report the
pressure as a percentage of the high range gauge. For example, if the
system has a 100 Torr gauge attached to CDG1 and a 1 Torr gauge attached
to CDG2 and the actual system pressure is 0.1 Torr the response to the
R5 command will be P+0.100.
6.0 - RS-232 Serial Interface and Commands
(continued)