Ntellisys, Daptive, Ressure – Nor-Cal Intellisys Adaptive Pressure Controllers User Manual
Page 15: Ontrollers, 0 - apc controller module interfaces
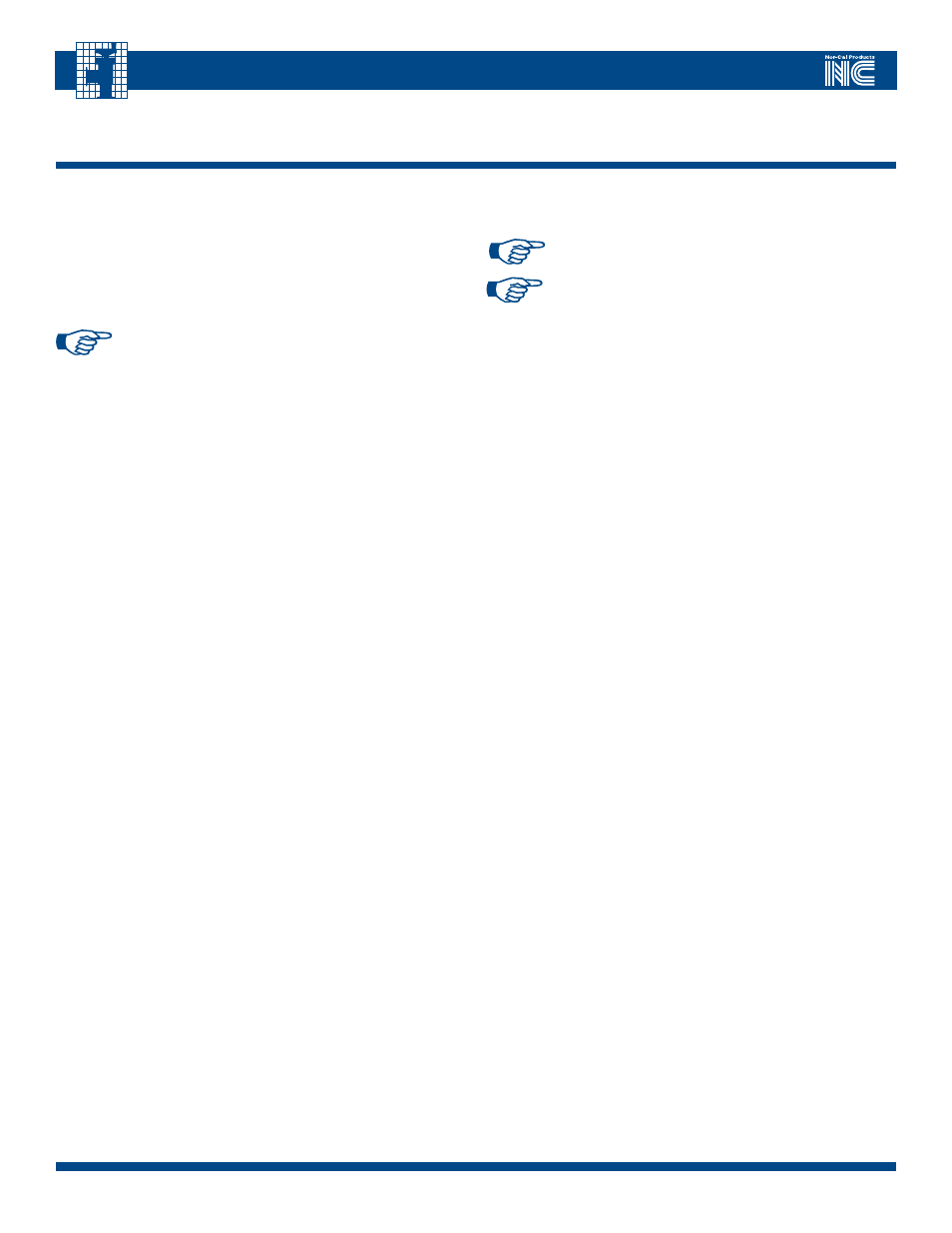
15
Call toll free
800-824-4166
or 530-842-4457
•
FAX 530-842-9130
I
ntellIsys
A
dAptIve
p
ressure
C
ontrollers
APC-OP-LIT 1/12
Vacuum Gauge Interface
The pressure signal from one or two vacuum gauges can be interfaced to the
APC controller module through the connector labeled GAUGE, or CDG1 and
CDG2 depending on the model. In addition, ±15 VDC is available to power
such gauges from these ports.
NOTE:
If the power requirement of the gauge(s) used
exceeds the rated power output, then a separate power
source must be used.
When only one gauge is used, then the pressure signal must be connected to
the CDG1+ and CDG1- signal pins. Use of two gauges requires adhering to
the following steps:
1. The full scale range of the two gauges used must be at least one but
no more than four decades (factors of ten) apart.
2. Only 1 gauge is active at a time.
Analog and TTL Interface
(not available on all models)
For complete control and monitoring purposes using a PLC or A/D communi-
cations PC cards, several analog I/O signals as well as a host of discrete (TTL)
I/O contacts are made available through the connectors labeled ANALOG/TTL
or I/O, depending on model. The analog inputs and outputs are referenced to
the analog output common, and are factory set as 0 to 10 Volt signals, though
a 0 to 5 volt range can be selected via the dip-switch. All analog I/O is
calibrated to within 10 mV.
All TTL outputs are active low signals except for the FAULT function, which is
active high. TTL inputs are diode protected at –0.4 VDC. Maximum low input
voltage is 0.6V and the minimum sink current is 1 mA. The minimum high
input voltage is 2.5V, or open. TTL outputs are optically isolated and rated at
25V max and 10 mA. TTL inputs are referenced to the Digital Ground (pin #7),
whereas the TTL outputs are referenced to TTL Out Common on pin #24.
On some controller models, certain functions and signals are available on
more than one connector. This is to give the user a choice of how to connect
the device, and also to offer the capability for in-situ monitoring without
disconnecting the main interface cables
Serial interface
An RS-232 serial interface is available on all controller models, through one or
more ports. Please refer to the Section 6.0 for a full description of the com-
munications protocol and a listing of all active serial commands. A three-wire
connection completes the communications consisting of Rxd (data from the
APC), Txd (data to the APC) and digital ground.
NOTE:
CTS, RTS and DSR connections
are neither needed nor available.
NOTE:
The default factory RS-232 communications parameter
settings are 9600 Baud, 1 stop bit and no parity. These settings
can only be changed on models with DIP switches, and changing
the setting requires cycling APC input power off then back on.
Every serial input command sent by the HOST has an end-of-line delimiter, car-
riage return ASCII 0x0D [hex], or the line feed character ASCII 0x0A [hex], or
the carriage return and line feed character in that order. The APC-device end-
of-line delimiter is the carriage return and line feed characters.
DeviceNet Interface
(not available on all models)
The five-pin circular DeviceNet port allows for complete remote control,
monitoring and power supply of the APC controller in a cost effective and reli-
able way. In addition to the connector are two status LEDs labeled Mod and
Net, as well as three rotary switches labeled MSD, LSD and RATE. A complete
explanation of the DeviceNet physical and software interfaces can be found in
Sections 8 and 9.
Indicating LEDs
There are a host of indicating LEDs on the APC controller, depending on
model. In general, the green Power LED is illuminated whenever power is
applied to the device. The green Ctrl LED is illuminated whenever the APC is
in set point control (pressure or position). The amber Fault LED is illuminated
briefly during the initialization sequence after power-up but primarily if the
APC device enters a fault state. Two LEDs usually are located adjacent to the
OPEN and CLOSE switches or labels, and are illuminated whenever the valve
position is within 2% of either limit.
Switches
Some controller models have a bank of four or eight dip switches labeled SW1.
These are principally used for serial communications settings and selecting 0-5
VDC analog input. A switch in the “up position” (relative to the text) is OFF,
and dip switch #1 is always in the left most position. Please refer to the tables
in Section 3 for a complete listing of valid dip switch settings.
Primarily intended for operation during installation or troubleshooting, some
APCs also feature two momentary switches that can be used to drive the valve
fully open or closed. To prevent inadvertent valve operation, these switches
cannot be used if the APC valve is in Control Mode (green Ctrl LED on).
5.0 - APC Controller module Interfaces
APC controllers have several interfaces available for communications and connectivity to peripheral devices, depending on model. These are described by func-
tion below. Please also refer to Figures 3.1 – 3.5 and their associated Tables for the specific connectors and their pin assignments.