2 constant setpoint mode, 1 setting the setpoint, 3 4 to 20 milliamp remote setpoint mode – AERCO KC1000 Boiler equipped with Mod-Box Controller User Manual
Page 30: 1 4 to 20 ma remote setpoint field wiring, 2 4 to 20 ma remote setpoint startup, Mode of operation
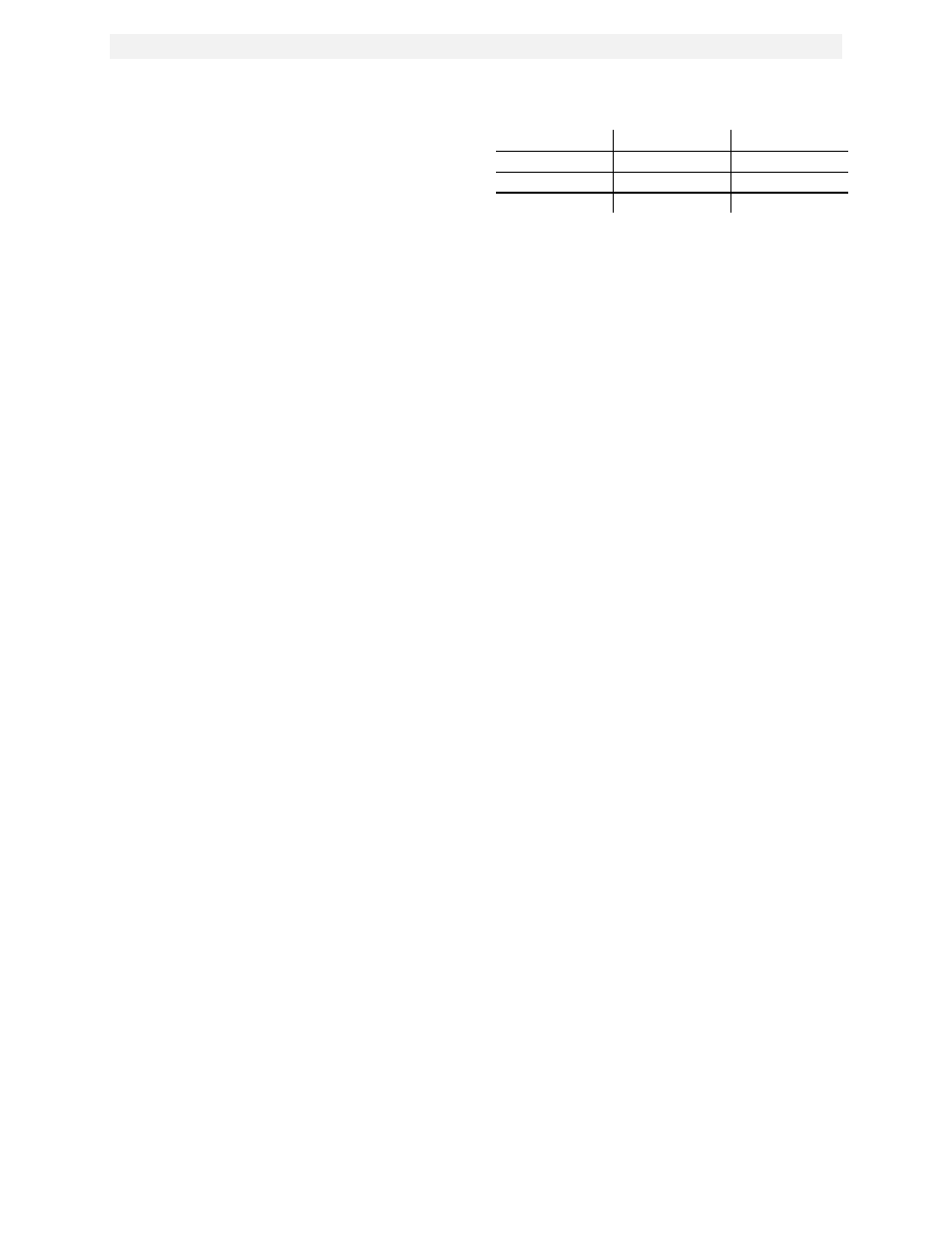
MODE OF OPERATION
25
5.2 CONSTANT SETPOINT MODE
Constant setpoint mode of operation is when a
non-changing, fixed, header temperature is
desired. Common uses of this mode of operation
include water source heat pump loops, and shell
and tube heat exchangers for potable hot water
systems or processes.
There are no external hookups, other than AC
power, necessary to operate in this mode. While
it is necessary to set the desired setpoint
temperature, it is not necessary to change any
other temperature-related functions. The unit is
factory preset with settings that work well in most
applications. Prior to changing any temperature-
related parameters, other than the setpoint, it is
suggested that AERCO be contacted. For a
complete listing of factory, defaults and a
description of temperature related functions see
Appendices A and E.
5.2.1 SETTING THE SETPOINT
The setpoint of the unit is adjustable from 50 to
220 degrees. To set the setpoint do the
following:
1. While in the Primary menu, scroll through it
until "Setp" is displayed.
2. Use
the
⇑ ⇓ keys to set the desired setpoint.
3. Press enter to accept any changes.
4. The unit is now ready to run.
5.3 4 to 20 MILLIAMP REMOTE
SETPOINT MODE
In this mode of operation a 4 to 20ma signal sent
to the unit changes it’s setpoint. The signal is
typically sent from an energy management
system that determines the appropriate setpoint
based on outside air temperature. In this mode a
4ma signal is equal to a 50-degree setpoint while
a 20ma signal is equal to a 220 setpoint. This
mode of operation can be used to drive single as
well as multiple units.
In this mode, the external interface board is
utilized. The interface board, located in the field
wiring box, is factory configured and converts the
4 to 20 ma signal to an RS-485 signal. The RS-
485 signal is in turn sent to the temperature
controller. For the temperature controller to
recognize a signal, from an external source, the
following functions must be correctly set.
MENU FUNCTION
SETTING
Secondary Lore
re
Secondary FUNC
Cont
Primary
Auto
ON
While it is possible to change the settings of
temperature related functions; the unit is factory
preset with settings that work well in most
applications. It is suggested that an AERCO
representative is contacted prior to changing any
temperature related function settings. For a
complete listing of factory, defaults and a
description of temperature related functions see
Appendices A and E.
5.3.1 4 to 20 MA REMOTE SETPOINT
FIELD WIRING
The only wiring necessary is the 4 to 20ma
signal wires from the source, to terminals 13 and
14 in the field wiring box. The signal must be
floating (ungrounded), and the wire used must
be a two wire shielded cable of 22 gauge
minimum. Polarity must be observed and the
shield must be connected to terminal 1 in the
external field wiring box. The source end of the
shield must be left floating and not connected.
When driving multiple units, each unit’s wiring
must conform to the above.
5.3.2 4 to 20 MA REMOTE SETPOINT
STARTUP
Since this mode of operation is factory preset
and the setpoint is being externally controlled, no
startup instructions are necessary. However the
unit must be taken out of remote mode, and set
to local mode, to manually run the unit. Once
finished with manual mode it is necessary to set
the unit back to remote mode for it to accept
signals from an external source. The
temperature controller must also be left in
manual and not automatic mode.
To set the unit to local mode, do the following:
1. Access the temperature controller’s
secondary menu.
2. Scroll through the menu until "lore" is
displayed.
3. Use
the
⇑ ⇓ keys to set the temperature
controller to local. The yellow REM light, on
the temperature controller, should
extinguish.
4. Press ENTER to accept the change.