1 preparation, 2 installation procedure, Preparation – Rice Lake Combination System - Precision Loads On-Board Weighing Systems User Manual
Page 64: Installation procedure
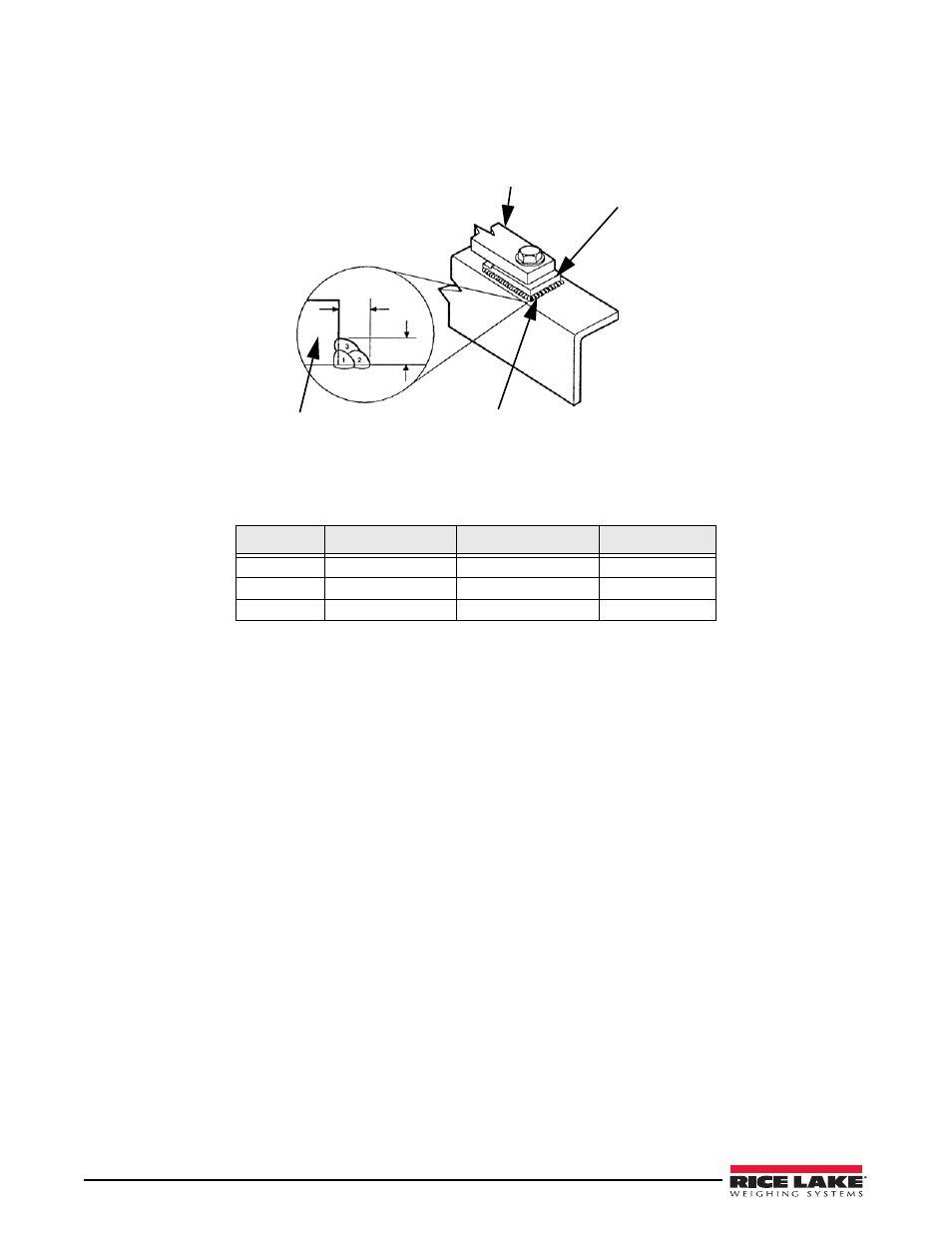
60
Precision Loads On-Board Weighing Installation & Service Manual
Fillet Size
The minimum size of the finished triple-pass fillet may not be less than 1/2 inch. See Figure 6-1, “Weld Sequence,”
on page 60.
1.
Root Pass
2.
Base Pass
3.
Final Pass
Bending Plate
Load Cell
Bearing Plate
Weld Three
Exposed Surfaces
0.5”
0.5”
Figure 6-1. Weld Sequence
Electrode
Specifications of the electrode are as follows:
Table 6-3. Electrode Specifications
Process
Size
Type
Company
SMAW
1/8, 5/32 or 3/16
E7018
Must be dry
FCAW
.045 to 3/32
E71T-5 or E70T-5
Gas shielded
GMAW
.035 to 1/16
E70S-6
Spray Transfer
6.3.1
Preparation
All bearing plates must be inspected by the installer and cleaned prior to welding to remove any dirt, paint, rust,
grease, oil or other material from the bare metal surfaces. The angle brackets to which the bearing plates will be
welded must also be cleaned to bare metal. Use a surface grinder or power wire brush to ensure that the bearing
plate mounting areas of the brackets are clean, flat bare metal. Never use bearing plates that have been removed
from another installation.
6.3.2
Installation Procedure
1. Preheating of the bearing plates and the angle bracket surface is necessary prior to welding in order to
minimize shrinkage stresses. Use an acceptable torch arrangement and preheat to a minimum of 70 degrees
F (20 degrees C) and a maximum of 150 degrees F (65 degrees C).
2. Tack weld all bearing plates to angle brackets with load cells mounted to ensure correct positioning. Rice
Lake Weighing Systems recommends removal of load cells prior to final welding of the bearing plates. The
installer must ensure that the electrode is directed away from the underside of the load cell.
3. Remove slag from tack welds and "feather" end of tack with a grinder to provide a smooth transition for
the final weld root pass as it passes through the tack. Each fillet bead must be visually inspected with all
slag cover removed before proceeding to the next bead.
4. Alternate weld passes end to end, side to side to avoid bracket distortion.