Cooper Instruments & Systems DFI 1650 Multi-Channel Digital Force Indicator User Manual
Page 47
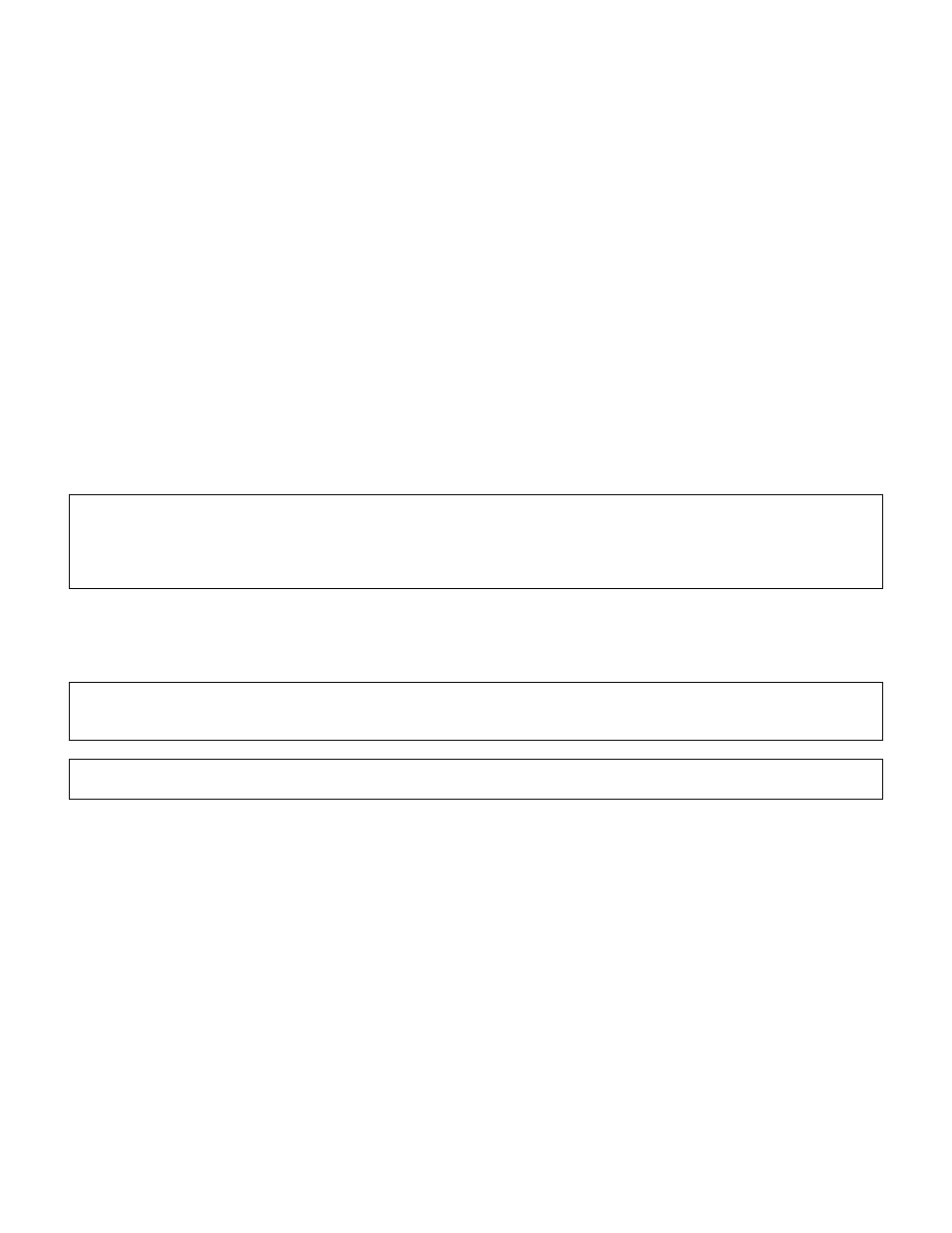
CF 66
41
Rev. C 2/05
KNOWN POINT x/y Menu Items
This enters the engineering units for the know-displacement calibration points. These points must match the actual
displacements that you will apply to the transducer during calibration. The number of calibrations points depends
on the CALIBRATION TYPE.
When using the 2-Point Known Displacement Calibration type, the following menu items are available:
• “KNOWN POINT 1/2”: point 1 of 2, usually 0% of the transducer’s full-scale capacity.
• “KNOWN POINT2/2”: point 2 of 2, usually 100% of the transducer’s full-scale capacity.
When using the 3-Point Known Displacement Calibration type, the following menu items are available:
• “KNOWN POINT 1/3”: point 1 of 3, usually 0% of the transducer’s full-scale capacity.
• “KNOWN POINT 2/3”: point 2 of 3, usually 50% of the transducer’s full-scale capacity.
• “KNOWN POINT 3/3”: point 3 of 3, usually 100% of the transducer’s full-scale capacity.
When using the 5-Point Known Displacement Calibration type, the following menu items are available:
• “KNOWN POINT 1/5”: point 1 of 5, usually 0% of the transducer’s full-scale capacity.
• “KNOWN POINT 2/5”: point 2 of 5, usually 25% of the transducer’s full-scale capacity.
• “KNOWN POINT 3/5”: point 3 of 5, usually 50% of the transducer’s full-scale capacity.
• “KNOWN POINT 4/5”: point 4 of 5, usually 70% of the transducer’s full-scale capacity.
• “KNOWN POINT 5/5”: point 5 of 5, usually 100% of the transducer’s full-scale capacity.
To insure both correct operation of the transducer and application of the displacement, the instrument expects the
voltage applied at each known-displacement point to be increasing. For example, the displacement applied at
Known-Displacement Point 2/2/ must cause the transducer to produce a more positive voltage than at a Known-
Displacement Point ½. You may need to swap the (+)Signal and (-)Signal wires on the 12-pin channel connector to
accomplish this.
11.5.6 CALIBRATE Menu Item
This menu item performs a calibration according to what was entered in the CALIBRATION TYPE and
CALIBRATION DATA menu items.
Before performing a calibration, the transducer must be connected to the instrument, the CALIBRATION TYPE
must be selected and the CALIBRATION DATA must be entered (see “CALIBRATION DATA Sub-Menu” in Section
11.5.5)
For maximum accuracy, allow at least twenty minutes of warm-up with the excitation voltage applied to the
transducer before calibration
If the CALIBRATON TYPE is a 2-Point Known Displacement Calibration…
• The display will read DOING 2POINT CAL, and prompt you to APPLY 00000 UNIT (where 00000 and UNIT are
previously entered as KNOWN POINT 1/2 and DISPLAY.UNITS). When you have applied this displacement to
the transducer, press [ENTER].
• The display will read WORKING, then APPLY 01000 UNIT (where 01000 and UNIT are previously entered as
KNOWN POINT 2/2 and DISPLAY.UNITS). When you have applied this displacement to the transducer, press
[ENTER].
• Upon completion, the display will indicate DONE and the instrument will return to the RUN mode.
If the CALIBRATION TYPE is a 3-Point Known Displacement Calibration…
• The display will read DOING 3POINT CAL, and prompt you to APPLY 00000 UNIT (where 00000 and UNIT are
previously entered as KNOWN POINT 1/3 and DISPLAY.UNITS). When you have applied this displacement to
the transducer, press [ENTER].
• The display will read WORKING, then APPLY 00500 UNIT (where 00500 and UNIT are previously entered as
KNOWN POINT 2/3 and DISPLAY.UNITS). When you have applied this displacement to the transducer, press
[ENTER].