Cutmaster 42 troubleshooting – Tweco 42 CutMaster Service Manual User Manual
Page 54
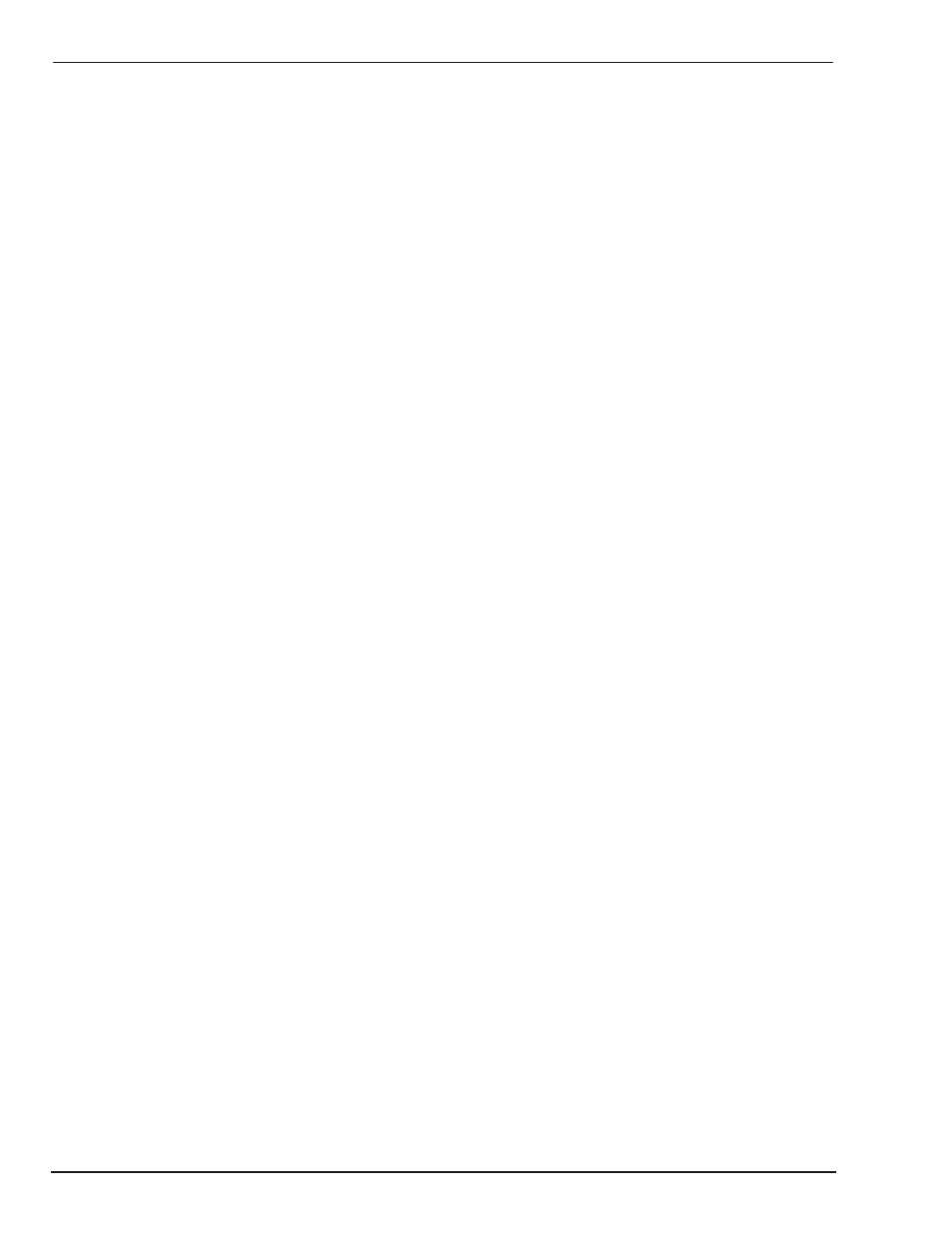
Troubleshooting 6-18 Manual 0-5171
CUTMASTER 42
TROUBLESHOOTING
The mains supply voltage is connected via a double pole switch to the input rectifier U1 through an EMC filter. Over-
voltage protection is provided by varistor CY1.
The rectifier circuit converts the inputted AC voltage to DC voltage. The input current is controlled through being
compared with reference wave. The reference point is a pure sine wave which derives from the source voltage. The
PFC control chip will be used to generate suitable gate signal to drive V8 and V8-1, ensuring the current is sinusoidal.
The boost diode output charges the main capacitor bank (C16, C17, C18, C19, C20 and C21) to high voltage. Inrush
current limiting is provided by a high power resistor which is then bypassed by relay J1 after a few seconds.
The primary igbt transistors (T1, T2, T4, and T5) switch the transformer primary at high frequency and varying duty
cycle. The transformer return wire is taken from the junction of the capacitors C20 and C21 (the voltage at this point
is approximately half the DC bus voltage).
Secondary output voltage from the transformer is rectified by the output diodes (T14-1 and T16-1) to DC. This DC
is controlled by the PWM of the primary side igbt transistors, and is filtered by an inductor before connecting to the
output terminals.
A thermal overload device (thermistor) is fixed to the rectifier heatsink. When an over temperature occurs, the control
circuit inhibits the trigger and the output. The thermal overload indicator LED on the front panel is illuminated.
The current transformer TR8 provides a signal to the control circuit to indicate both transformer primary current, and
also detect transformer saturation. The Hall effect current sensor is powered from regulated + & - 15VDC supplies
and provides a voltage signal proportional to the output DC cutting current to allow the control circuit to regulate
cutting current.