Testing the control – tekmar 263 Boiler Control User Manual
Page 32
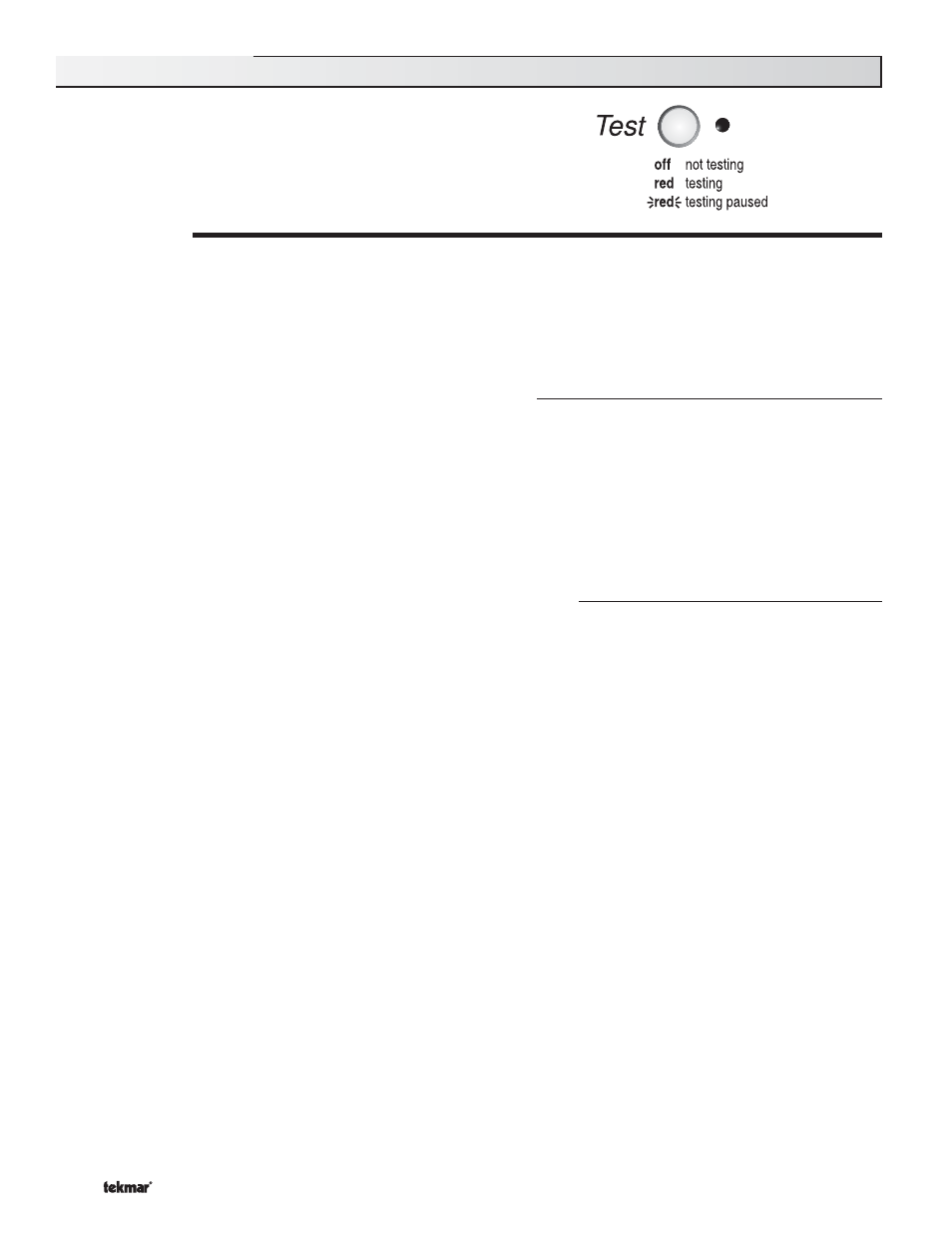
© 2009 D 263 - 03/09
32 of 36
The control has a built-in test routine that is used to test the main control
functions. The control continually monitors the sensors and displays an
error message whenever a fault is found. See the following pages for a
list of the control’s error messages and possible causes. When the Test
button is pressed, the Test light is turned on. The individual outputs and
relays are tested in the following test sequence.
Testing the Control
TEST SEQUENCE
Each step in the test sequence lasts 10 seconds.
During the test routine, if a demand from the system is present, the test sequence may be paused by pressing the Test button.
If the Test button is not pressed again for 5 minutes while the test sequence is paused, the control exits the entire test routine. If
the test sequence is paused, the Test button can be pressed again to advance to the next step. This can also be used to rapidly
advance through the test sequence. To reach the desired step, repeatedly press and release the Test button until the appropriate
device and segment in the display turn on.
Test sequence when in MODE 1 - Two Stage On / Off Stages:
Step 1 – The primary pump contact is closed.
Step 2 – If Boiler 1 is set to automatic (Au), the Boiler 1 contact is closed for the Fire Delay time or a minimum of 10 seconds.
Step 3 – If Boiler 2 is set to automatic (Au), the Boiler 2 contact is closed for the Fire Delay time or a minimum of 10 seconds.
Step 4 – Boiler 1 and Boiler 2 contacts are opened.
– If DHW MODE is set to 1 or 2, the DHW Pmp / Vlv contact is closed and the primary pump contact is opened.
– If DHW MODE is set to 3 or 4, the DHW Pmp / Vlv contact is closed and the primary pump contact remains closed.
Step 5 – After the test sequence is completed, the control resumes its normal operation.
Test sequence when in MODE 2 - One Modulating Boiler and Pump:
Step 1 – The primary pump contact is closed.
Step 2 – The boiler pump contact is closed.
Step 3 – The Boiler 1 contact is closed and the modulation output is set to the Minimum Modulation setting.
Step 4 – If there is a demand present, the modulation output increases to Maximum Modulation according to the Motor Speed setting.
Step 5 – If there is a demand present, the modulation output decreases to Minimum Modulation according to the Motor Speed setting.
Step 6 – The Boiler 1 and boiler pump contacts are opened.
– If DHW MODE is set to 1 or 2, the DHW Pmp / Vlv contact is closed and the primary pump contact is opened.
– If DHW MODE is set to 3 or 4, the DHW Pmp / Vlv contact is closed and the primary pump contact remains closed.
Step 7 – After the test sequence is completed, the control resumes its normal operation.