5 regulator routine – Rockwell Automation 9329 Drive Application Software Tension Control Gen. Units User Manual
Page 21
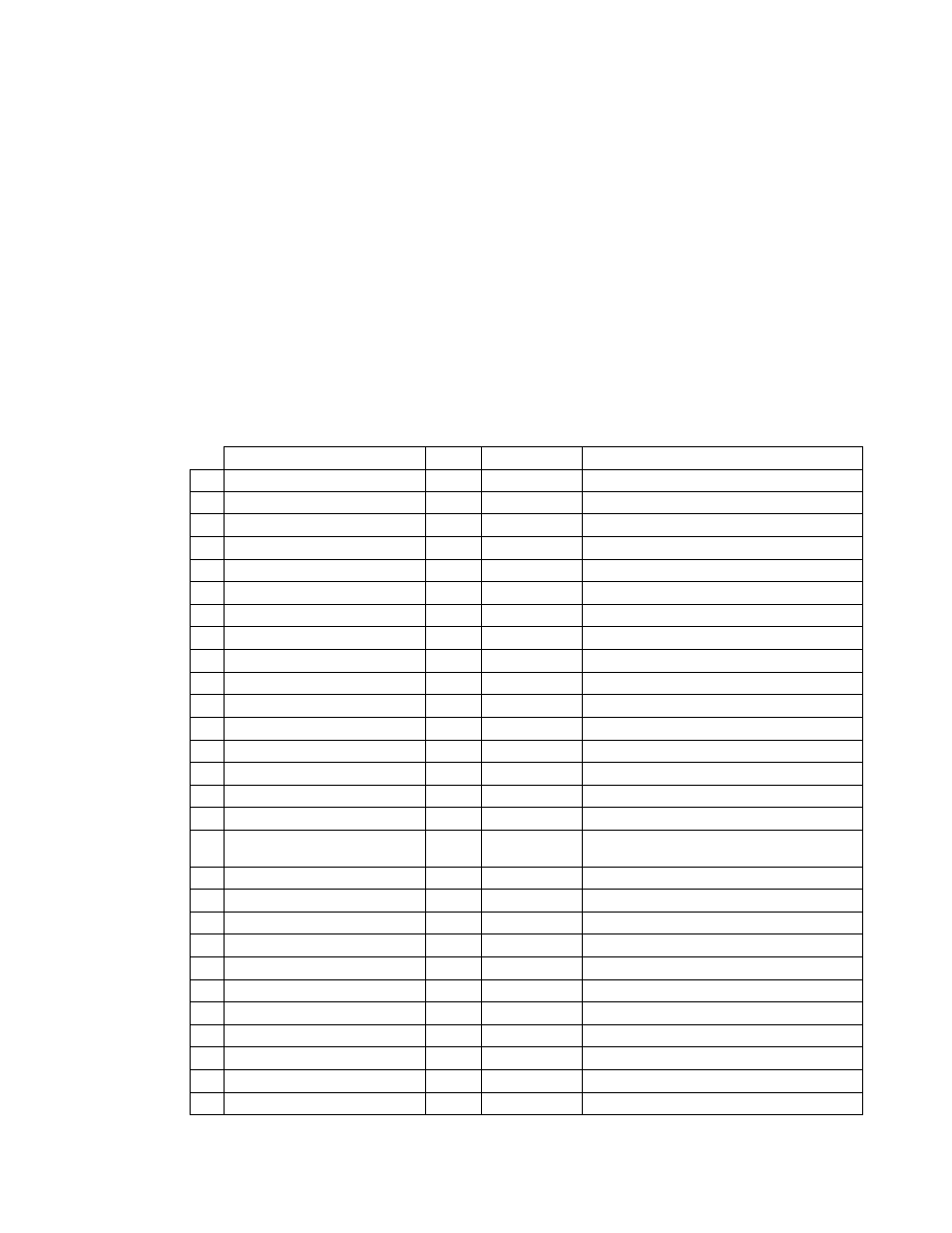
FM – Tension Control
Drive Application Software – page 21 of 52
4.5 Regulator routine
The regulator routine is responsible for closing the tension, position or torque loop. This
routine is also responsible for switching between stall and run reference. When enabled, the
regulator will ramp the reference set point from the feedback value to the set point.
This routine accepts the feedback directly from the analog input module. The routine will
then scale the feedback from minimum tension reference to a maximum tension reference.
This routine also generates a feed forward torque reference based on the tension set point,
roll radius, gear ratio and motor rated torque.
The closed loop system consists of a lead-lag filter and a PI regulator. This has the ability to
close all three types of tension regulation loops (tension, position or torque). When the
regulator is configured for tension, the feedback is actual tension from a load cell. When the
regulator is configured for position, the feedback is the actual position feedback of a dancer.
There is a signal generated in the routine that may be optionally used to apply loading
pressure to the dancer. When the regulator is configured for torque, the feedback is the
torque feedback from the drive.
Input Parameters
Name
Type
Range
Description
1 TenStp_DC
REAL
NA
Tension set point [Data Counts](RAW)
2 TenStpMin_DC
REAL
NA
Min Tension set point [Data Counts]
3 TenStpMax_DC
REAL
NA
Max Tension set point [Data Counts]
4 TenRfStall_Pct
REAL
0 to 100
Tension Reference Stall Percent
5 TenRfStallMin_Pct
REAL
0 to 100
Tension Reference Stall Min Percent
6 TenRfTaper_Pct
REAL
0 to 100
Tension Reference Taper %
7 DanStpt_Pct
REAL
0 to 100
Dancer Set point [% of Full Storage]
8 RfRate_PctSec
REAL
0 to 100
Reference Rate [% per Second]
9 TenDanFb_DC
REAL
NA
Tension/Dancer Fdbk [Data Counts]
10 TenDanFbMin_DC
REAL
NA
Minimum Tension/Dancer Feedback
11 TenDanFbMax_DC
REAL
NA
Maximum Tension/Dancer Feedback
12 TrqFb_PU
REAL
-2.0 to 2.0 Torque Feedback [Per Unit]
13 TrimKP
REAL
0 to 50
Trim Regulator Proportional Gain
14 TrimWld_Rad
REAL
0 to 5
Trim Regulator Lead Frequency
15 TrimLimSpd_Pct
REAL
0 to 100
Speed Trim Limit [% Max Line Speed]
16 TrimLimSpdZero_Pct
REAL
0 to 100
Speed Trim Limit at Zero Speed
17 LineSpdTrimLimSpd_Pct
REAL
0 to 100
Line Speed where full speed trim will
be available
18 TrimLimTrq_Pct
REAL
0 to 100
Torque Trim Limit [% of Max Tension]
19 TrimRate_PctSec
REAL
0 to 100
Trim Rate [% Unit/Second]
20 TrimFbWLead_Rad
REAL
0 to 10
Feedback Lead Frequency [Rad/Sec]
21 TrimFbWLag_Rad
REAL
0 to 200
Feedback Lag Frequency [Rad/Sec]
22 DrvTrqRfJLoss_PU
REAL
-2.0 to 2.0 Inertia & Losses Torque Ref to Drive
23 LineSpd_EU
REAL
NA
Line Speed [Engineering Units]
24 LineSpdMax_EU
REAL
NA
Line Speed Maximum
25 MtrSpdBase_RPM
REAL
NA
Base Speed from Motor Name Plate
26 Constant_RPMperEU
REAL
XXX
Converstion Constant
27 BuildUpRate
REAL
XXX
Build Up Ratio
28 TrqRf_Pct
REAL
-100 to 100 Torque Reference [% Rated Torque]