Mg-30 pump — maintenance (pump) – Multiquip MG30M2D User Manual
Page 50
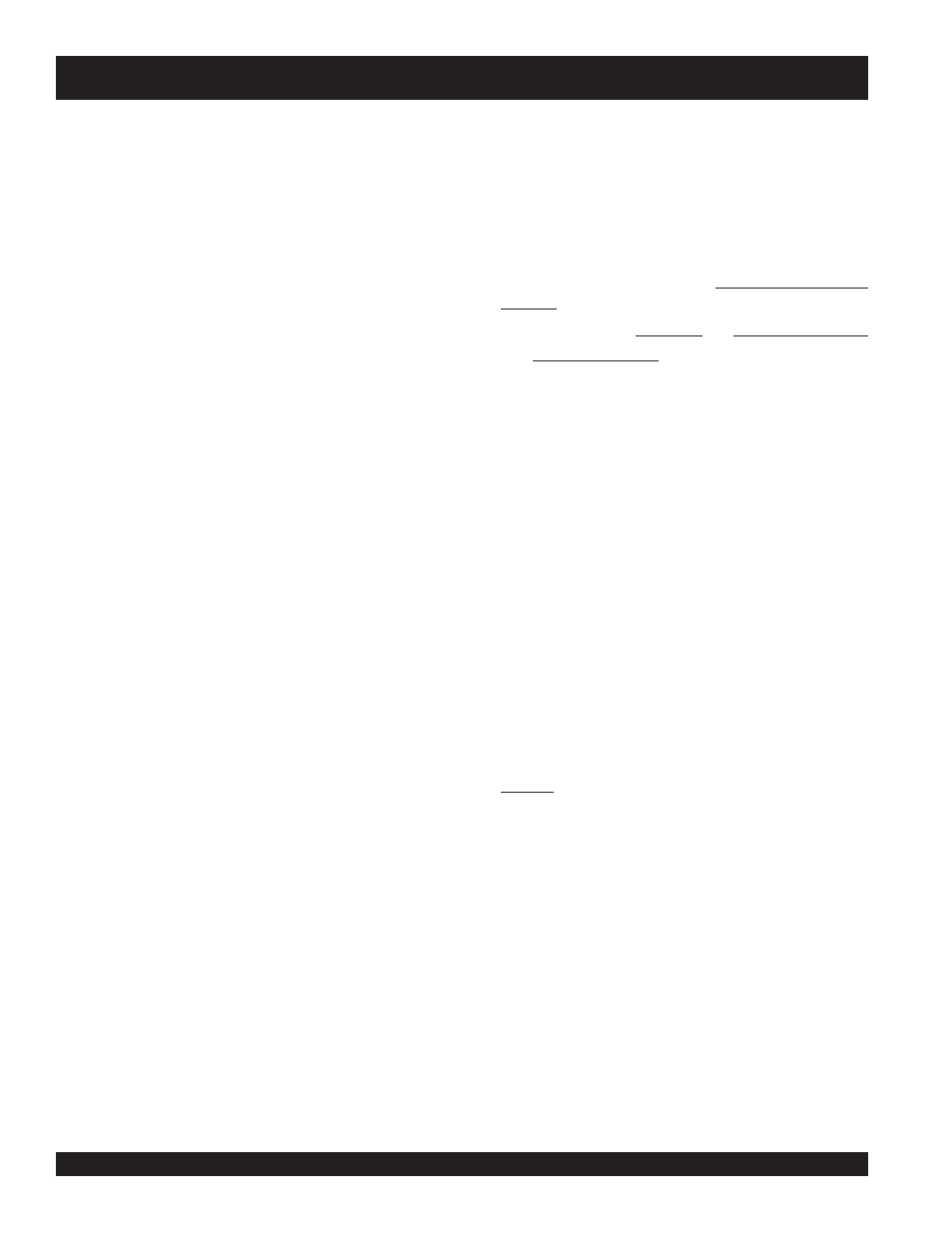
PAGE 50 — MAYCO MG-30 PUMP — OPERATION AND PARTS MANUAL — REV. #3 (09/15/11)
MG-30 PUMP — MAINTENANCE (PUMP)
CLEANING THE PUMP
When changing from one material to another, or when shutting
down the machine for a period of time, or at the end of the working
day, the machine should be washed out and the hoses cleaned
to prevent the material from setting and causing difficulties when
operation is resumed. FOLLOWING IS A SUGGESTED
PROCEDURE FOR CLEANING THE MACHINE AND HOSES:
1. Dump all material from the
mixer into the hopper and
pump material form hopper. Scrape down the sides of
the hopper to clean off as much material as possible.
Shut off pump; open pressure release valve to relieve
hose pressure and disconnect material hose from
machine.
2. Add
15 to 20 gallons of water to the hopper. Start the
pump and flush water through the pump to remove all
material and sand from the pump. Shut off pump; insert
a wet sponge into the open end of the material hose and
connect the hose to the pump.
3. Add
15 to 20 gallons of water to the hopper. Remove
the nozzle from the end of the hose, start the pump,
and force the sponge through the hose. The sponge
scrubs down the inside of the hose and acts as a divider
between the water and the material. It prevents the
water from channeling through the hose, removing the
cement or gypsum while leaving a portion of the sand
still in the hose. Sand or any other material left in the
hose will cause the hose to pack up when next used.
4. Repeat Steps 2 and 3 until no additional material is
flushed from the hose. Avoid dumping the dirty water
produced by cleaning the mixer into the pump hopper.
The sand can settle out and clog the pump.
5. Wash and wire-brush nozzle and oil it. Clean screen
and hose down machine with water.
6. Spray entire machine with regular motor oil. This will
assist you in keeping it clean
ENGINE (Hatz Model 2M41LZ Diesel)
The Model MG30-2 is equipped with a Model 2M41LZ, 35 H.P.
air-cooled diesel engine. For information concerning the
procedure in checking, removing, cleaning, etc. of the various
engine parts or any other information on the engine not contained
herein, refer to the engine manufacturer’s instruction manual.
CRANKCASE
1. The crankcase oil should be
CHECKED EVERY 8
HOURS of operation.
2. The old oil should be
DRAINED and FRESH OIL ADDED
after
EVERY 40 HOURS of operation. To drain oil, remove
plug located on engine base. Drain engine crankcase
oil when oil is warm it will flow more freely.
AIR CLEANER
1. The air cleaner, mounted on the side of the engine, is
an essential engine component. It filters the air entering
the carburetor. Depending on the conditions under which
the engine is operated, servicing of the air cleaner will
vary from a
few days of operation in comparatively clean
conditions to
twice a day in dusty conditions.
FUEL STRAINER
1. The fuel strainer is very necessary in preventing
sediment, dirt and water from entering the carburetor.
This strainer is equipped with a glass bowl and should
be inspected at least
once a week and cleaned if dirt or
water is present.
AIR COMPRESSOR
1. A
weekly check should be made of the compressor's
crankcase oil level to make sure it is at the
full mark, or
at least between the two marks on the dipstick (Figure 29).
NEVER allow the oil to fall below the lower mark. (Refer
to Table 7) for proper oil recommendation.) Crankcase
oil capacity is 1.5 pints ( .709 liters)
2. The oil should be completely changed approximately.
every
30 days; sooner if oil becomes dirty or diluted.
The crankcase should be thoroughly cleaned with each
oil change. Refer to the Quincy Compressor
Maintenance Manual for further information concerning
lubrication, adjustment and maintenance of the air
compressor.
3. An air filter has been installed on the air compressor.
This filter should be checked and cleaned
WEEKLY under
normal conditions. If extremely dusty conditions prevail,
it is advisable to clean the air filter at least once a day.
4. To clean air filter, soak sponge element in solvent and
let it dry out; then dip element in clean oil, permit oil to
drip off and reinstall on unit.