Mg-30 pump — general information – Multiquip MG30M2D User Manual
Page 20
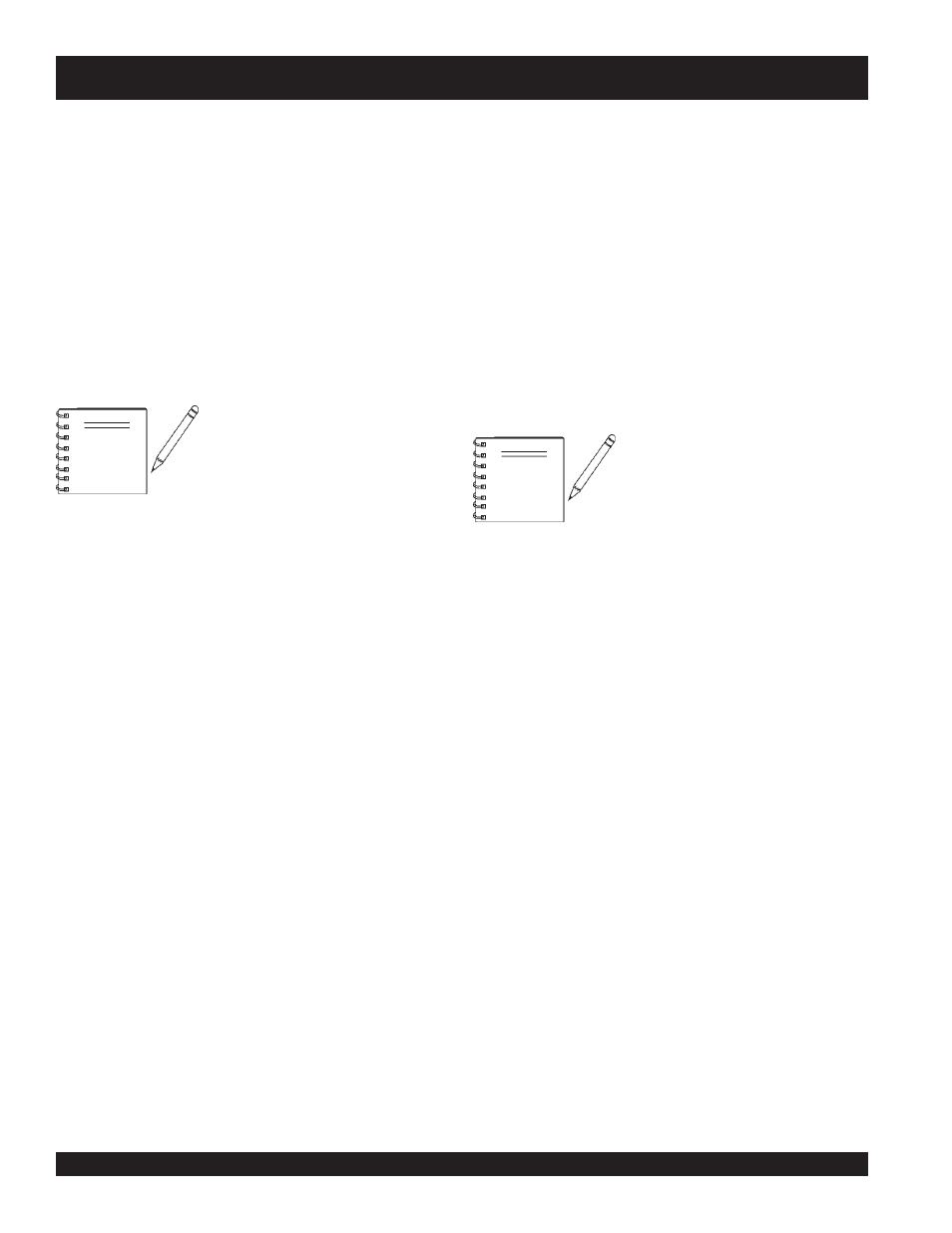
PAGE 20 — MAYCO MG-30 PUMP — OPERATION AND PARTS MANUAL — REV. #3 (09/15/11)
O-Rings
O-Rings have been installed at sealing points throughout the
pump head unit. These O-rings act as seals and are very
important for the efficiency of the machine. Great care should be
taken when assembling or disassembling those parts where “O”
rings have been installed. Always clean O-ring groove thoroughly
grease O-ring before installing.
Inspection of O-rings should be made regularly. It should be
done each time a part containing an O-ring has been
disassembled. Carefully remove and check O-ring to see it is
not chipped, broken, peeled or has any other signs of deformity.
If any of these conditions exists, the O-ring should be replaced.
MG-30 PUMP — GENERAL INFORMATION
USE ONLY "O-RINGS" OBTAINED
FROM THE FACTORY
, as they are
manufactured of a special hardened
rubber to meet this specific application.
NOTE
Valve Seats
The valve seats are a loose fit in the pump housing. There are no
set screws holding them in place. When the valve seat has been
worn to a point where a
new
rubber check ball strikes the bar in
the valve seat (keeping the ball from seating properly), the valve
seat should be replaced.
Sand Packs
Washed sand left in the material hose can cause a sand pack
(clog) in the hose. When the material hose is washed out, make
sure all of the loose sand is washed out of the hose. If loose sand
is allowed to remain in the hose, the new material coming through
the hose will push the sand ahead until it forms a clog in the
hose.
Separation
Separation in the pump or the material hose is caused by water
being forced out of the material through a loose connection.
Make sure that none of the gaskets or o-rings in the pumping
system leak. Loose hose connections are one of the most
common causes of separation.
Whenever water leaks out through a hose connection, the
material will build up slowly. In an hour or so, depending on how
bad the leak, a restriction will form at the connection causing the
pump to work much harder to force the material through the
restriction. This also slows down the output production of the
pump. If this condition is not corrected, the pump will jam and
stop.
Pump Overloading
If at any time the pump is jammed from separation or a sand
pack in the hose, the clutch on the engine will slip. This will
protect the moving mechanical parts of the pump from being
overloaded and damaged. The capability allows the pump to
shut itself down in the event an operator is not near pump if a
sand pack or jam-up occurs.
When the drive belt is moved from the largest pulley on the
clutch to the smallest, the output power of the pump is increased
by a factor of three. So, when operating the pump at the lower
speed, the RPM of the engine should also be reduced. This will
allow the clutch to slip in the event of a separation or sand pack,
and therefore will safeguard the hoses and the mechanical
working parts of the pump from damage.
Operating the pump at lower speeds
(placing the drive belt in either of the two
pulley groves next to the engine) will
develop high pressure in the material
hoses when the pumping of stiff materials is required. Make sure
that all hoses are in good condition and that all connections are
air tight. When using the lower pumping speeds, run the engine
at a lower speed.
Leaks
Water can become separated from the material being pumped.
This is usually caused by loose connections or damaged seals.
When separation occurs, a restriction caused by a buildup of
material around the leak forces the pump to work harder. As a
result, pump output is lowered and eventually the pump will
stop.
Hose and Fittings
Due to the high pressure which the machine is capable of
producing we recommend the use of specially constructed
MAYCO hose. This hose has been designed to withstand the
pressures required to pump the material.
MAYCO hoses are available in 25 ft. and 50 ft. lengths. Each size
is equipped with a male insert on each end.
It is suggested to use all 2-inch (5.08 cm.) hose with the exception
of the last 25 or 50 ft. This should be 1.5 inch (3.81 cm.) hose, to
be used as a whipline.
Wheels
The machine is equipped with
pneumatic (air) type wheels
,
rotating on tapered roller bearings. These bearings have been
packed at the factory and need not be repacked for approximately
6 months, at which time they should be removed, cleaned and
repacked with a good grade of wheel bearing grease.
NOTE