Mg-30 pump — general information, Caution – Multiquip MG30M2D User Manual
Page 18
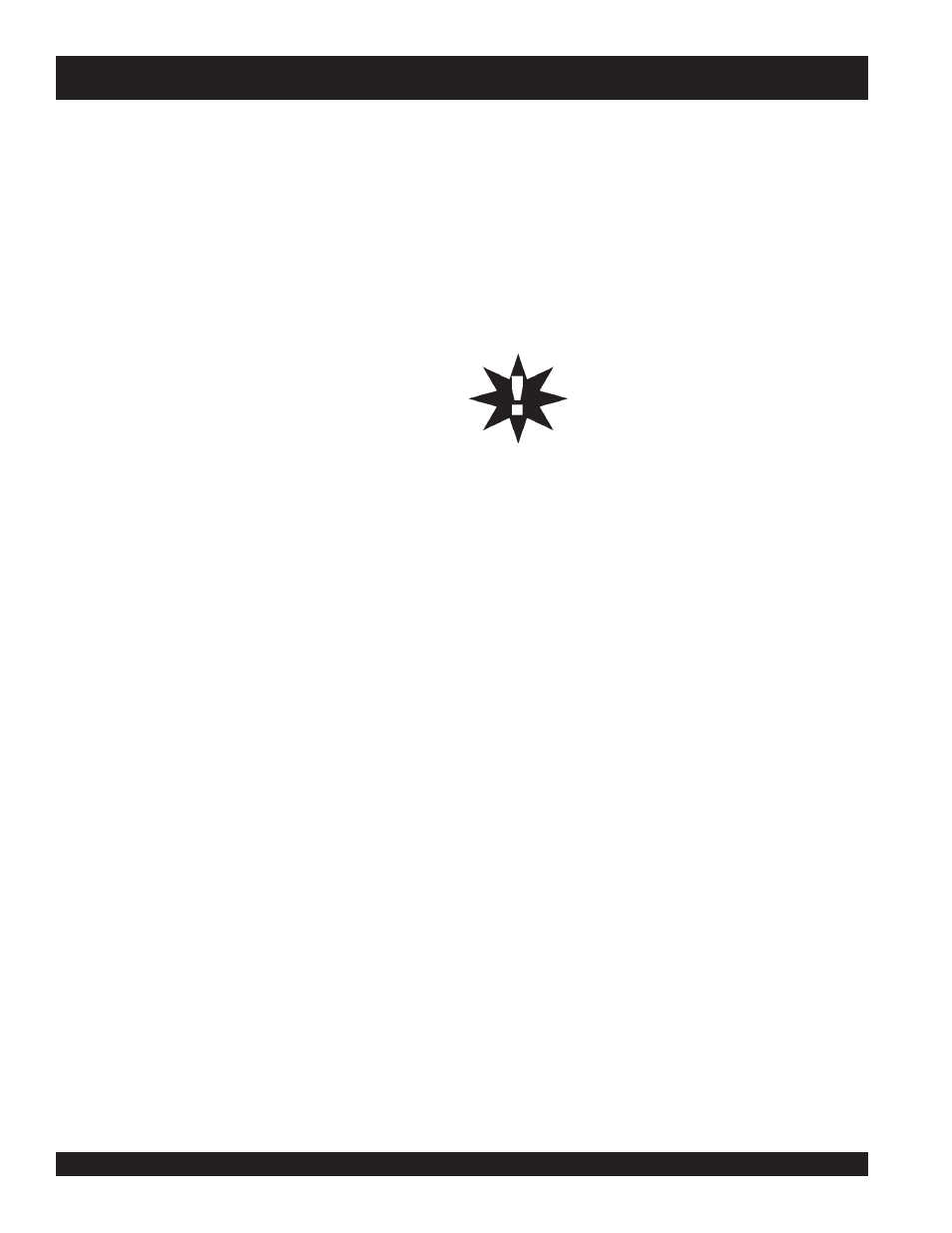
PAGE 18 — MAYCO MG-30 PUMP — OPERATION AND PARTS MANUAL — REV. #3 (09/15/11)
MG-30 PUMP — GENERAL INFORMATION
General
The MAYCO Model MG30-M and MG30T plaster-mortar,
fireproofing pumps are designed to pump material at a steady
rate of flow. This is accomplished with two pistons. One piston
does all the pumping; the other is a
slave piston
. The slave
piston is a
compensation piston
and operates in a manner
which causes the pulsating material from the pumping piston to
be pumped at a steady rate of flow.
Your MAYCO pump has been serviced and test-run at the
factory. Upon delivery and inspection the machine is ready for
operation on the job.
This pump uses a 3-1/2 inch pumping piston and therefore
develops a higher pressure than most concrete pumps. It is
extremely critical that the pump drive components, pumping lines
and components are of the finest quality and maintained in a
manner to prevent accidents. Use only
high pressure
rated
hoses and couplings.
The MG-30 has been assembled with a
pressure relief valve
installed at the discharge port on the manifold. NEVER pump
materials unless this (pressure relief valve) mechanism is
installed.
Normally, the 750 psi rated brass cap is used in plaster
applications, whereas the 1,000 psi rated unit is used for higher
pressure applications and fireproofing. The brass cap and ball
should be removed and
cleaned daily
, or more often if necessary,
to prevent material setting up around the ball.
If material hardens around the ball, it will not be effective as a
relief valve when high pressure develops. Install ball discharge
in downward position. Use the manual relief part of this valve to
relieve line pressure before disconnecting material lines or hoses
Power for the operation of this pump is supplied by a Hatz Model
2M41LZ, 35 H.P. diesel air-cooled engine. This engine transfers
power through a V-belt to a totally enclosed speed reducer and
also operates a twin-cylinder piston type air compressor.
The MG-30 is equipped with an
electrically controlled
solenoid
valve
and
gravity-feed piston oiler system
. The
electrically controlled solenoid allows the operator to
start
and
stop
the pump remotely from the nozzle.
When the solenoid valve is energized (i.e. electric current is
applied to the solenoid) the engine speed will increase to the
pre-set governed speed, engaging the
centrifugal clutch
and
pump. When the solenoid is de-energized, the engine speed
will decrease, returning to idle, disengaging the centrifugal clutch
and pump.
.
CAUTION :
If hoses or lines are
blocked
for any reason, or
if lines are
kinked
when starting up or during
pumping cycle, the pump pressure could
straighten out the kink or force out the blockage.
The rapid surge of material could cause the lines
to
whip
or move in a manner that could cause injury to personnel.
When moving hoses from one job site application to another it is
important to walk the entire system and
visually inspect
for any
kinks or sharp bends in the hose, before starting or resumong
the pumping operation.
The following definitions will help assist you in understanding
common pump terminology.
Centrifugal Clutch
The centrifugal clutch is designed to slip when the engine speed
drops due to overloading of the pump. This is a safety device to
protect other parts of the machine from damage and to prevent a
buildup of pressure in the material hose. Continued operation of
the machine when the clutch is slipping will cause damage to
the clutch. The clutch needs no adjustment or lubrication.
Pump Head Unit
The pump head unit consists of two pistons--one being the
pumping piston and the other a compensating piston, driven by
the cam and rocker arm principle.
The pump housing is equipped with inlet and outlet valve seats
and two special hard rubber or steel balls. When the piston is
retracted, the inlet valve seat opens for intake of material into the
piston chamber; when the piston is extended, the inlet valve
closes and the outlet valve opens, allowing material to be
pumped. There are three sections to the pump head unit.
ALWAYS ASSEMBLE THESE SECTIONS PRIOR TO
MOUNTING PUMP HEAD UNIT ON FRAME, MAKING SURE
THE SEAL RINGS FIT UP AIRTIGHT.
Located at the rear of the pump is the mixing unit. The drum
batch capacity of this mixing unit is between 3.5 and 4.0 bags.
The mixer section of the pump can be powered by a either a XX
HP Honda gasoline engine, 8.0 HP Hatz diesel or 2.0 HP electric
motor.
Due to the abrasive nature of the materials being pumped, some
parts of the machine are likely to be worn from use more rapidly
than others. It is therefore suggested that spare parts be kept in
ready reserve at the job site to prevent downtime.