2 electrical operation, 1 control – MTS Model 506-62-72 Hydraulic Power Supply User Manual
Page 37
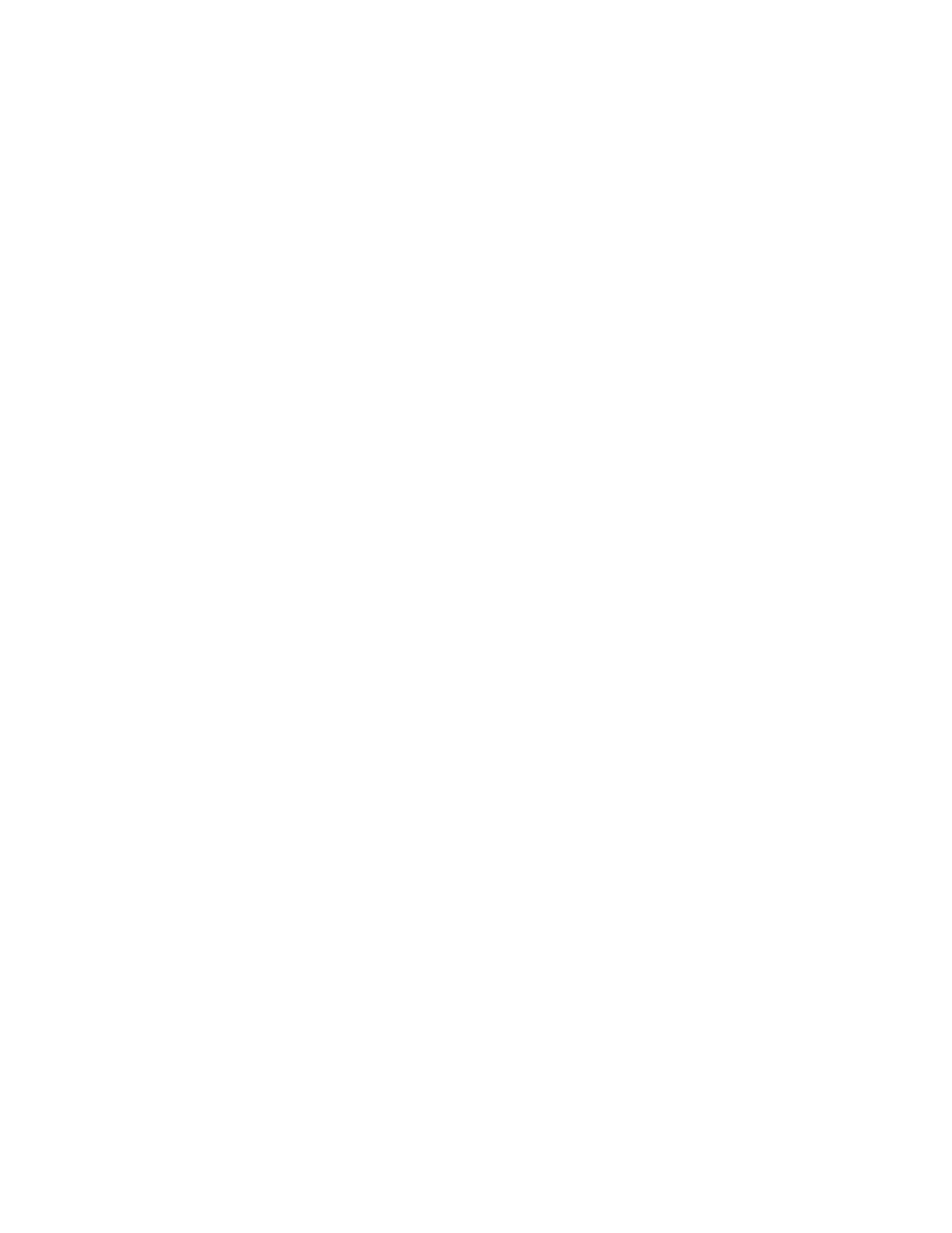
Theory of Operation 5-3
Pump protection
Pump protection is provided for the main pump by the main pump
low-inlet pressure switch that turns the supply off if supercharge
pressure drops below the recommended operating pressure. The
supercharge pump and main pump are protected by a fluid-level
switch, which turns the supply off if the level of hydraulic fluid in the
reservoir drops below a preset level.
Pressure accumulation
The pump-outlet pressure accumulator smooths the HPS output and
provides additional hydraulic pressure for high instantaneous flow
demands. It is precharged with dry nitrogen to a pressure proportional
to HPS output pressure. The optional slow turn-on accumulator slows
the rate at which the backup relief valve shifts from low to high
pressure. The precharge must be adjusted proportionally to the HPS
output pressure. If it is above or below the recommended level, the
effect of the accumulator is reduced.
5.2
Electrical Operation
This section provides the HPS electrical theory of the operation.
Figure 5-2 is a typical electrical schematic for the 506.62/.72 HPS.
HPS operation is controlled by a PLC (programmable logic controller).
It is designed so that a desired circuit in relay ladder logic can be
programmed. The PLC provides logic functions previously
accomplished by relays, timers and sequencers. It contains an I/O
section that receives input data from various switches and contacts that
are hardwired to the input terminals. The PLC sends output commands
to motors, motor starters, solenoid valves and indicator lights that are
hardwired to the output terminals. The PLC operating program is
retained by an EPROM memory module. A back-up battery is not
required.
5 . 2 . 1
Control
When the disconnect switch is closed, the HPS control panel Power On
indicator lights to show that electrical power to the HPS is on.
Inlet pressure
When the High/Low/Start switch is positioned to Start, relay 1M at
PLC output 111 energizes to start the supercharge motor. Contacts 1M
provide the supercharge motor status to PLC input 013. The
supercharge motor provides inlet pressure for the main pump. When
the inlet pressure is reached (typically 15 psi), pressure switch 1PS
(connected from the outlet of the supercharge pump to PLC input 012)
closes to start the pump motor.
Start control
The start signal is sent to input 002 of the PLC. If various conditions
(such as interlocks) are satisfied, the start signal is routed to output 104
of the PLC to energize the main pump motor start control relay (1CR).