Lenze MC1000 Series User Manual
Page 75
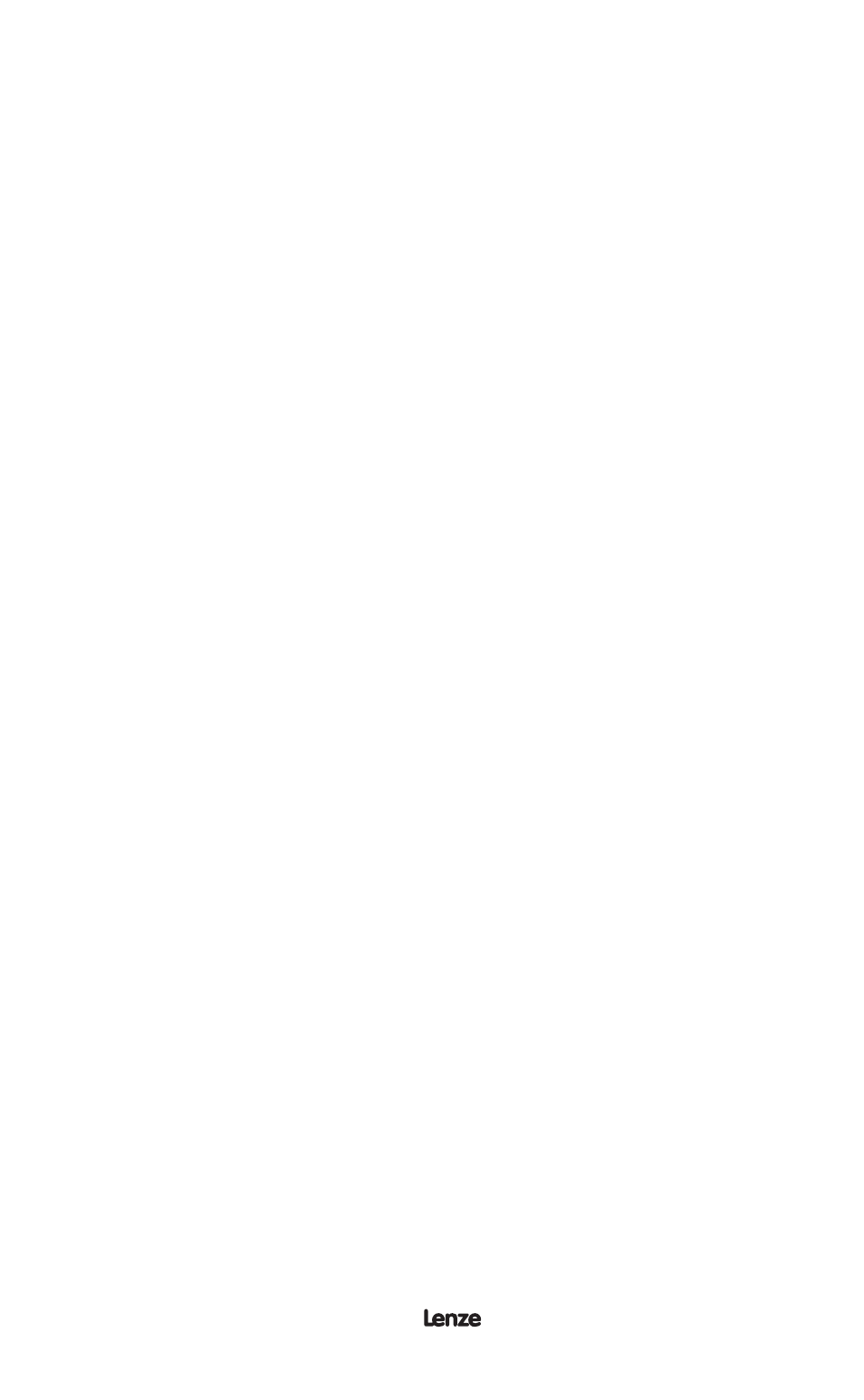
13435742_EDBM101_v24
71
Example 1: A 0-100 psi transducer outputs a 4 mA signal at 0 psi and 20 mA at
100 psi. Program Parameter 75 to 0.0 PSI, and Parameter 76 to 100.0 PSI (This
assumes that Parameter 31 - UNITS is set to pid PSI, and Parameter 33 - UNITS
DP is set to XXX.X).
For a reverse acting transducer, set Parameter 75 - FB @ MIN to the maximum
process variable feedback value, and set Parameter 76 - FB @ MAX to the minimum
process variable feedback value. In other words, Parameter 75 is set higher than
Parameter 76. See the example below:
Example 2: A 0-100 psi transducer outputs a 20 mA signal at 0 psi and 4 mA at
100 psi. Program Parameter 75 to 100.0 PSI, and Parameter 76 to 0.0 PSI (This
assumes that Parameter 31 - UNITS is set to pid PSI, and Parameter 33 - UNITS
DP is set to XXX.X).
19.2
THE SYSTEM - DIRECT AND REVERSE ACTING
The entire system can also be direct or reverse acting. In a direct acting system,
an increase in motor speed causes an increase in the process variable. This is
equivalent to requiring an increase in motor speed in response to a decreasing
process variable feedback.
In a reverse acting system, an increase in motor speed causes a decrease in the
process variable. This is equivalent to requiring an increase in motor speed in
response to an increasing process variable feedback. Examples of direct and reverse
acting systems are described in the next section.
19.3
PID CONTROL - DIRECT AND REVERSE ACTING
The PID Set point Control software can be direct or reverse acting, and must be set
to match the system. This is accomplished with Parameter 70 - PID MODE. When
set to NORMAL (for direct acting systems), the PID unit will command an increase
in motor speed if the process variable feedback decreases, and a decrease in
motor speed if the process variable feedback increases. When set to REVERSE
(for reverse acting systems), the opposite is true.
NOTE: The REVERSE setting for Parameter 70 - PID MODE is not used to
compensate for reverse acting feedback devices. If a reverse acting feedback device
is used, program Parameters 75 and 76 as described above.
An example of a direct acting system is one that maintains duct pressure. Duct
pressure is the process variable that is monitored by the feedback device. As duct
pressure rises, motor speed needs to be decreased to maintain the pressure. A
direct acting PID control will command a decrease in motor speed in response to
an increasing process variable feedback.
An example of a reverse acting system is one that maintains water temperature in
a cooling tower. Water temperature is the process variable that is monitored by the
feedback device. As the water temperature rises, motor speed needs to be increased
to lower the temperature of the water. A reverse acting PID control will command an
increase in motor speed in response to an increasing process variable feedback.