Lenze MC1000 Series User Manual
Page 71
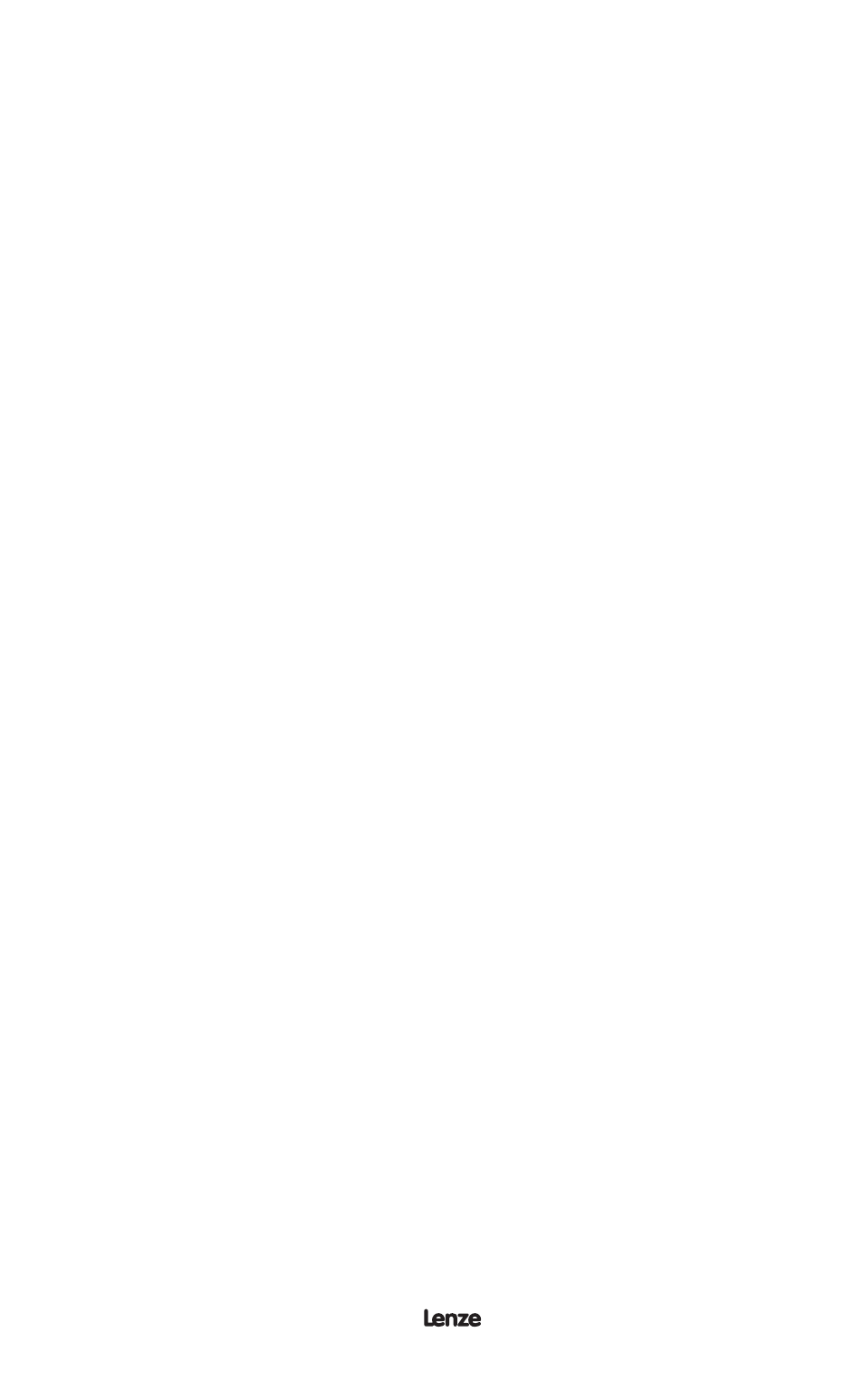
13435742_EDBM101_v24
67
When PID is enabled, and the drive is in LOCAL and AUTO mode, the drive will
also operate in a CLOSED LOOP fashion. However, in this case, the only set point
reference available is the keypad, and the SPEED REFERENCE SOURCE indication
in the CONTROL display will indicate AKB.
When PID is enabled, and the drive is in MANUAL and LOCAL or REMOTE mode,
the drive will operate in an OPEN LOOP fashion, responding directly to speed
commands from the keypad only. The SPEED REFERENCE SOURCE indication
in the CONTROL display will indicate MKB.
When PID is disabled, the drive will operate in an OPEN LOOP mode, responding
directly to speed commands from either the keypad (MANUAL mode) or an analog
input signal or preset speed (AUTO mode).
74
PID FB
(PID FEEDBACK SOURCE)
This parameter selects the terminal to be used for the feedback signal, and can be
set to TB-5A or TB-5B. TB-5A is used for 0-10 VDC signals, and TB-5B is used for
4-20 mA signals.
NOTE: The MC1000 has only one analog input of each type, so the same type of
signal cannot be used for feedback and set point reference. For example, a 4-20
mA signal from a transducer could not be used as a feedback signal if the set point
is being controlled by a 4-20 mA signal from a PLC.
75
FB @ MIN
(MINIMUM FEEDBACK VALUE)
This parameter should be set to the value of the process variable that corresponds
to the minimum transducer feedback signal (0 VDC or 4 mA).
76
FB @ MAX
(MAXIMUM FEEDBACK VALUE)
This parameter should be set to the value of the process variable that corresponds
to the maximum transducer feedback signal (10 VDC or 20 mA).
NOTE: If a reverse acting feedback device is being used, FB @ MIN should be
set to the maximum process variable value, and FB @ MAX should be set to the
minimum process variable value.
77
P GAIN
(PROPORTIONAL GAIN)
This parameter setting represents the speed command output (in % of maximum
speed) that results from each 1% of error (1% of the feedback range; FB @ MAX
minus FB @ MIN).
Example: If P GAIN is programmed for 5%, and the error (difference between set
point and feedback) is 10%, the speed command output of the Proportional term is
50% (10 x 5 = 50) of maximum speed.
78
I GAIN
(INTEGRAL GAIN)
This parameter setting represents the ramp rate of the speed command output (in
% of maximum speed per second) that results from each 1% of error.
Example: If I GAIN is programmed for 0.5 seconds, and the error is 5%, the rate
of rise of the speed command output of the Integral term is 2.5% (0.5 x 5 = 2.5) of
maximum speed per second.
79
D GAIN
(DIFFERENTIAL GAIN)
This parameter setting represents the speed command output (in % of maximum
speed) that results from each 1% per second change in the error.