Main feedback cable (feedback a) – ElmoMC ExtrIQ Digital Servo Drives-Eagle User Manual
Page 33
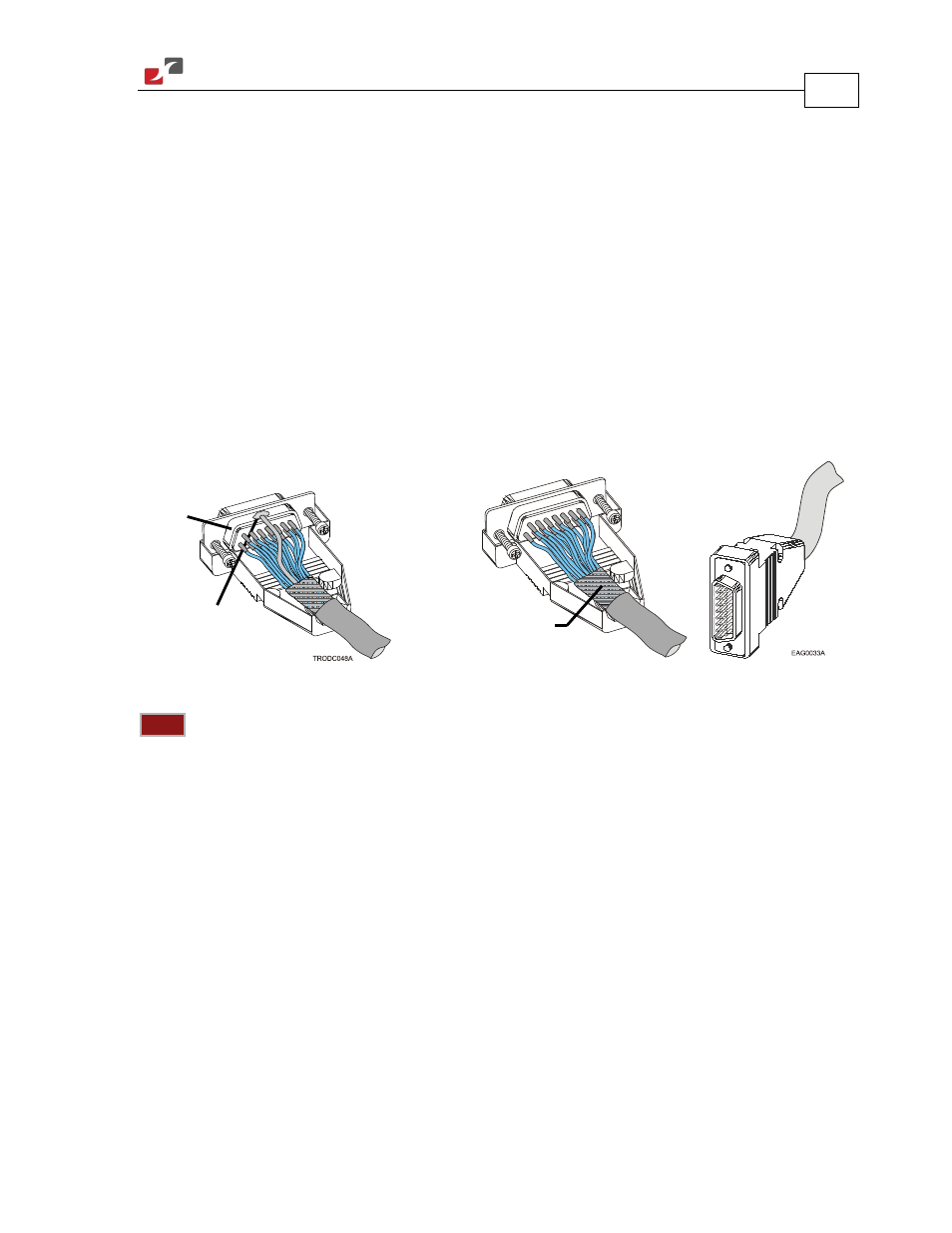
Eagle Installation Guide
Installation
MAN-EAGIG (Ver. 1.902)
33
3.4.3.
Feedback Control and Communication Cable Assemblies
The Eagle features easy-to-use D-Sub type connections for all Control and Feedback cables.
Instructions and diagrams describing how to assemble those cables are presented below.
1.
Use 24, 26 or 28 AWG twisted-pair shielded cables (24 AWG cable is recommended). For best
results, the shield should have aluminum foil covered by copper braid.
2.
Use only a D-Sub connector with a metal housing.
3.
Ideally, solder the drain wire to the connector body as shown in Figure 11.
However, the shield may also be attached without soldering, as long as the braid shield is in
tight contact with the metal housing of the D-type connector.
4.
On the motor side connections, ground the shield to the motor chassis.
5.
On controller side connections, follow the controller manufacturer’s recommendations
concerning the shield.
Figure 11: Feedback and Control Cable Assemblies
Note:
All D-Sub type connectors, used with the Eagle, should be assembled in this way.
3.4.4.
Main Feedback Cable (Feedback A)
The main feedback cable is used to transfer feedback data from the motor to the drive.
The Eagle accepts the following as a main feedback mechanism:
•
Incremental encoder only
•
Incremental encoder with digital Hall sensors
•
Digital Hall sensors only
•
Interpolated Analog (Sine/Cosine) encoder (option)
•
Resolver (option)
•
Tachometer & Potentiometer
•
Absolute Encoder
Make sure that the
braid shield is in tight
contact with the metal
housing
Connector
body
Drain wire
soldered to
the metal
housing