ElmoMC SimplIQ Digital Servo Drives-Bell Getting Started User Manual
Page 93
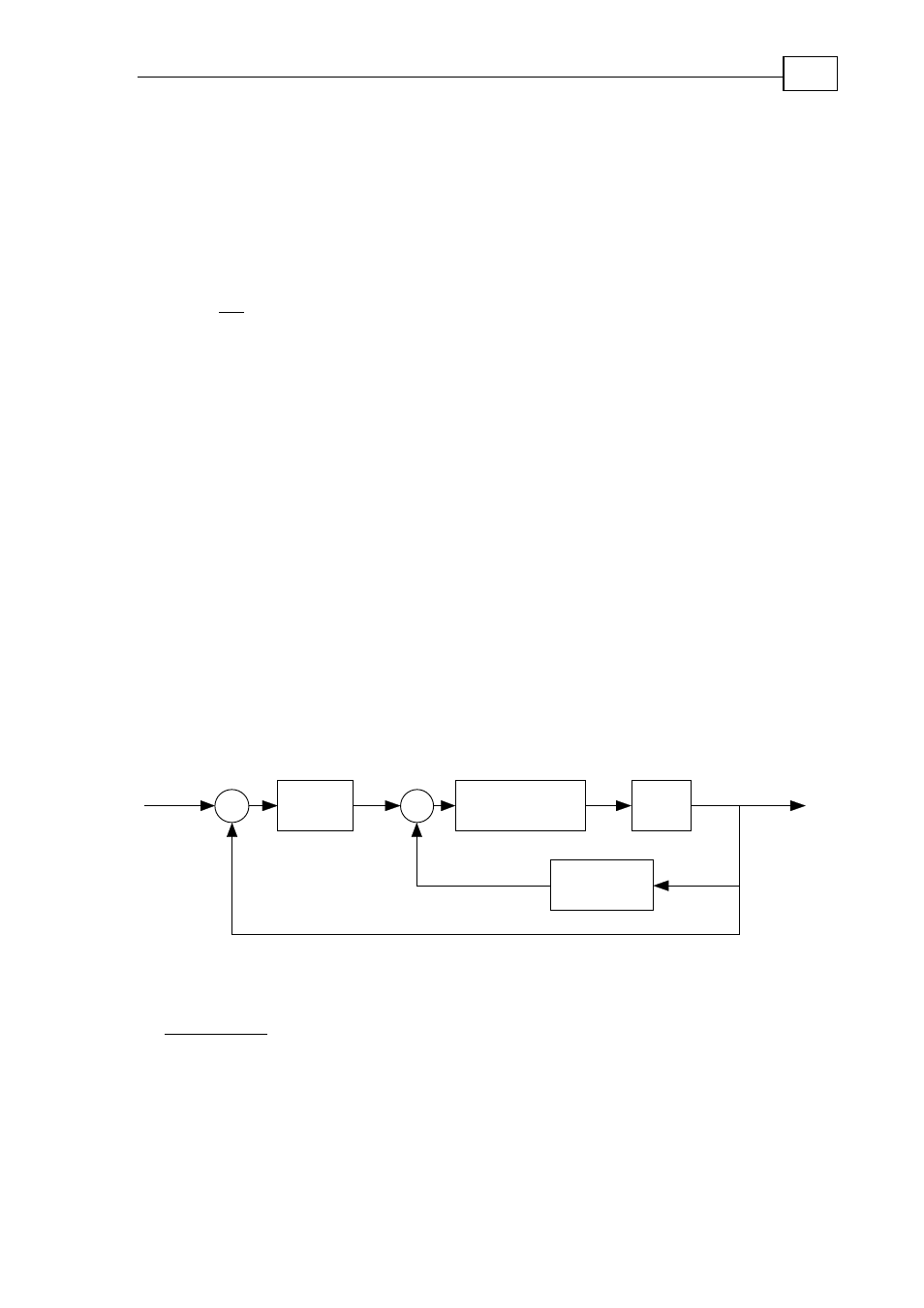
The SimplIQ for Steppers Getting Started & Tuning and Commissioning Guide
MAN-BELGS (Ver. 1.1)
93
PD controllers are not useful, as they permit steady state errors in the presence of
friction and unbalance. In the presence of friction or unbalance the controller
output
u
must be kept steadily non-zero while the tracking error vanished. A PD
controller cannot do that.
In order to enable a constant controller output when no tracking error is present
to drive the controller, we add an (integral) term to the controller; the result is the
PID controller. A PID controller is of the form
s
K
K
s
K
s
C
d
P
I
⋅
+
+
=
)
(
(18)
It means that the signals used to drive the system are the command input, plant
output, output integral and output derivative. For example, the input,
u
, to a
motor with command angle,
θ
, and measured angle,
M
θ
, will be
( )
( )
(
)
( )
( )
(
)
( )
( )
(
)
t
t
K
t
t
K
d
K
t
u
M
D
M
P
t
M
I
θ
θ
θ
θ
τ
τ
θ
τ
θ
&
& −
⋅
+
−
⋅
+
−
⋅
=
∫
∞
−
)
(
(19)
As explained above, PID controllers are superior to PD controllers, as they can
achieve a required command input ‘exactly’.
The integrator, however, reduces the phase margin and increases the difficulty of
controller tuning.
B.4.3.1
The Basic Usage of PI and PID Controllers
We use a PID controller for position control. In position controllers the derivative
term (representing speed feedback) is absolutely necessary to maintain feedback
stability.
The SimplIQ controllers "hide" the PID control as a cascaded PIP loop:
KP[2]+KI[2]/s
P(s)
s
-
Position
Speed
KP[3]
Ref
-
We observe that the transfer function of this controller is
[3]
[3
[2]
[2]
[2]
[2]
]
KI
K
KP
KP
P
KI
P
s
s
K
Ч
Ч
+
+
+
, so actually KP[2] is
D
K
,
KI[2]+KP[3]*KP[2] is
P
K
and KP[3]*KI[2] is
I
K
We must note that the SimplIQ implementation is less general than PID, because
it does not allow a complex zero pair.