Calibration, Serial communication, Problems with the controller – NOVUS Controller N2000S User Manual
Page 8
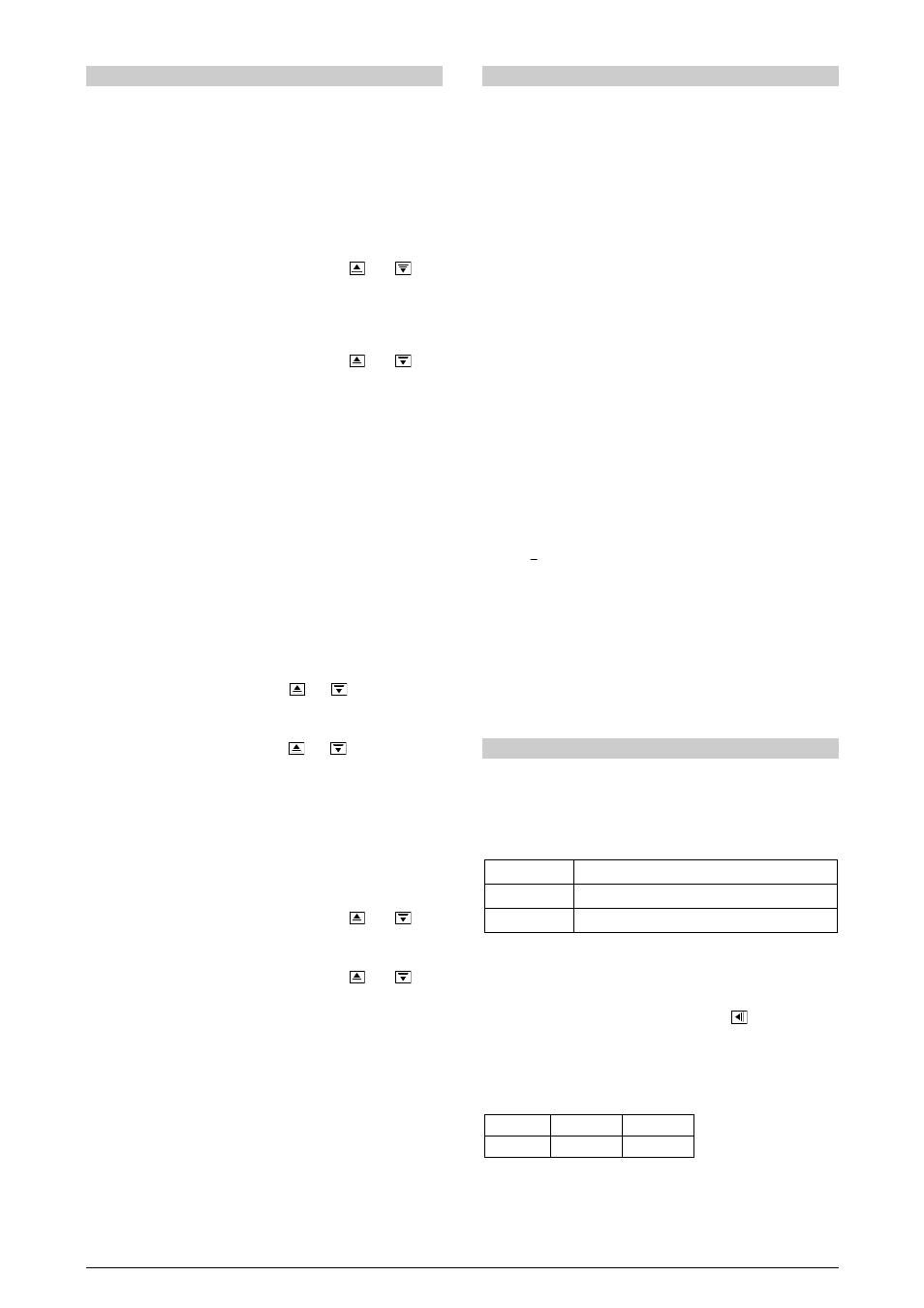
Controller N2000S
NOVUS AUTOMATION
8/9
CALIBRATION
INPUT CALIBRATION
All input and output types are factory calibrated. Recalibration is not
recommended for operators with no experience. In case recalibration
of any scale is necessary, proceed as it follows:
a) Set up the input type to be calibrated
b) Set the lower and upper limits of extreme values for the input type
c) Apply a signal to the input that corresponds to a known value and
a little bit over the lower limit of the indication.
d) Access the “inLC
inLC
inLC
inLC” parameter. By using the
and
keys
select the expected value that will appear in the parameters
display.
e) Apply a signal to the input that corresponds to a known value and
a little bit under the lower limit of the indication.
f) Access the “inLC
inLC
inLC
inLC” parameter. By using the
and
keys
select the expected value that will appear in the parameters
display.
g) Repeat c to f up to no new adjustment is necessary.
Note: When the controller is calibrated, check if the required
excitation current of Pt100 is compliant to the Pt100 excitation
current used in this instrument. 0.17 mA.
ANALOG OUTPUT CALIBRATION
1. Configure I/O 5 for 11 (0-20 mA) or 12 (4-20 mA) values.
2. Connect a mA meter in the analog control output.
3. Disable auto-tune and soft-start.
4. Program the lower limit of MV in the “ovLL
ovLL
ovLL
ovLL” prompt with 0.0 %
and the upper limit of MV in the “ovxL”
ovxL”
ovxL”
ovxL”with 100.0%.
5. Set “no
no
no
no “ for the manual mode “avto
avto
avto
avto” prompt.
6. Enable the control (YES
YES
YES
YES) at the “rvn
rvn
rvn
rvn” prompt.
7. Program MV in 0.0 % in the operation cycle.
8. Select the “ovLC
ovLC
ovLC
ovLC’’ prompt. Use the
and
keys to obtain the
0 mA (or 4 mA for type 12) reading in the mA meter.
9. Program MV in 100.0 % in the operation cycle.
10. Select the “ovxC
ovxC
ovxC
ovxC” prompt. Use the
and
keys to obtain the
20 mA.
11. Repeat 7 to 10 up to no new adjustment is necessary.
POTENTIOMETER CALIBRATION
a) Set up the input type to be calibrated
b) Set the lower and upper limits of indication for the extremes of the
input type
c) Adjust the potentiometer with the minimum value.
d) Access the “PotL
PotL
PotL
PotL” parameter. By using the
and
keys
select 0.0 in the parameters display.
e) Adjust the potentiometer with the maximum value.
f) Access the “Potk
Potk
Potk
Potk” parameter. By using the
and
keys
select 100.0 in the parameters display.
g) Repeat c to f up to no new adjustment is necessary.
SERIAL COMMUNICATION
An optional master-slave RS485 serial communication interface is
available. It is used for communication with a supervisor machine
(master). The controller is always the slave.
Communication starts only with the master, which sends a command
to the slave address with which it wants to communicate. The slave
takes the command and sends the correspondent response to the
master.
The controller accepts also broadcast commands.
FEATURES
Signals compliant to the RS-485 standard. Two-wire connection
between the master and up to 31 instruments in bus topology (it may
address up to 247 instruments). Maximum cable length: 1,000
meters. Time to disconnect from the controller. Maximum 2ms after
the last byte.
Communication signals are electrically isolated from the rest of the
device, speed options are 1200, 2400, 4800, 9600 or 19200 bps.
Number of data bits: 8, without parity
Number of stop bits: 1
Time of response transmission start: Maximum 100ms after receiving
the command.
Protocol used: MODBUS (RTU), available in most market-available
supervisory software.
RS-485 signals are:
D1 = D:
Bidirectional data line
D0 =
D:
Inverted bidirectional data line
C = GND:
Optional connection to improve communication
performance
COMMUNICATION PARAMETERS CONFIGURATION
Two parameters must be configured for serial use:
bavd
bavd
bavd
bavd: Communication speed. All equipments with the same speed.
Addr
Addr
Addr
Addr: Controller communication address. Each controller must
have an exclusive address.
PROBLEMS WITH THE CONTROLLER
Connection errors and inadequate programming are the most
common errors found during the controller operation. A final review
may avoid loss of time and damages.
The controller displays some messages to help the user identify
problems.
MESSAGE
PROBLEM
----
----
----
----
Open input. Without sensor or signal.
Err1
Err1
Err1
Err1
Connection problems in the Pt100 cable
Other error messages displayed by the controller can account for
errors in the input connections or type of selected input non compliant
with the sensor or signal applied to the input. If errors persist, even
after a review, contact the manufacturer. Inform also the device serial
number. To find out the serial number, press
for more than 3
seconds.
The controller also has a visual alarm (the display flashes) when the
PV value is out of the range set by spxl
spxl
spxl
spxl and spll
spll
spll
spll.
ORDERING INFORMATION:
N2000S -
485 -
24V
A
B
C
A: Series model:
N2000S
B: Digital communication:
blank
485 (RS485, Modbus protocol)
C: Voltage rating:
blank (100 to 240 Vac)
24V (24 Vdc/ac)