Safety instructions, 1 hazard levels, When is a central vacuuming system used – Karcher IV 100 - 55 M B1 User Manual
Page 5: Target groups for a central vacuuming system, Advantages of a stationary vacuuming system, Abstract of the system planning, Components of a stationary vacuuming system, 1 suction unit, 2 collection and disposal container, 3 filter
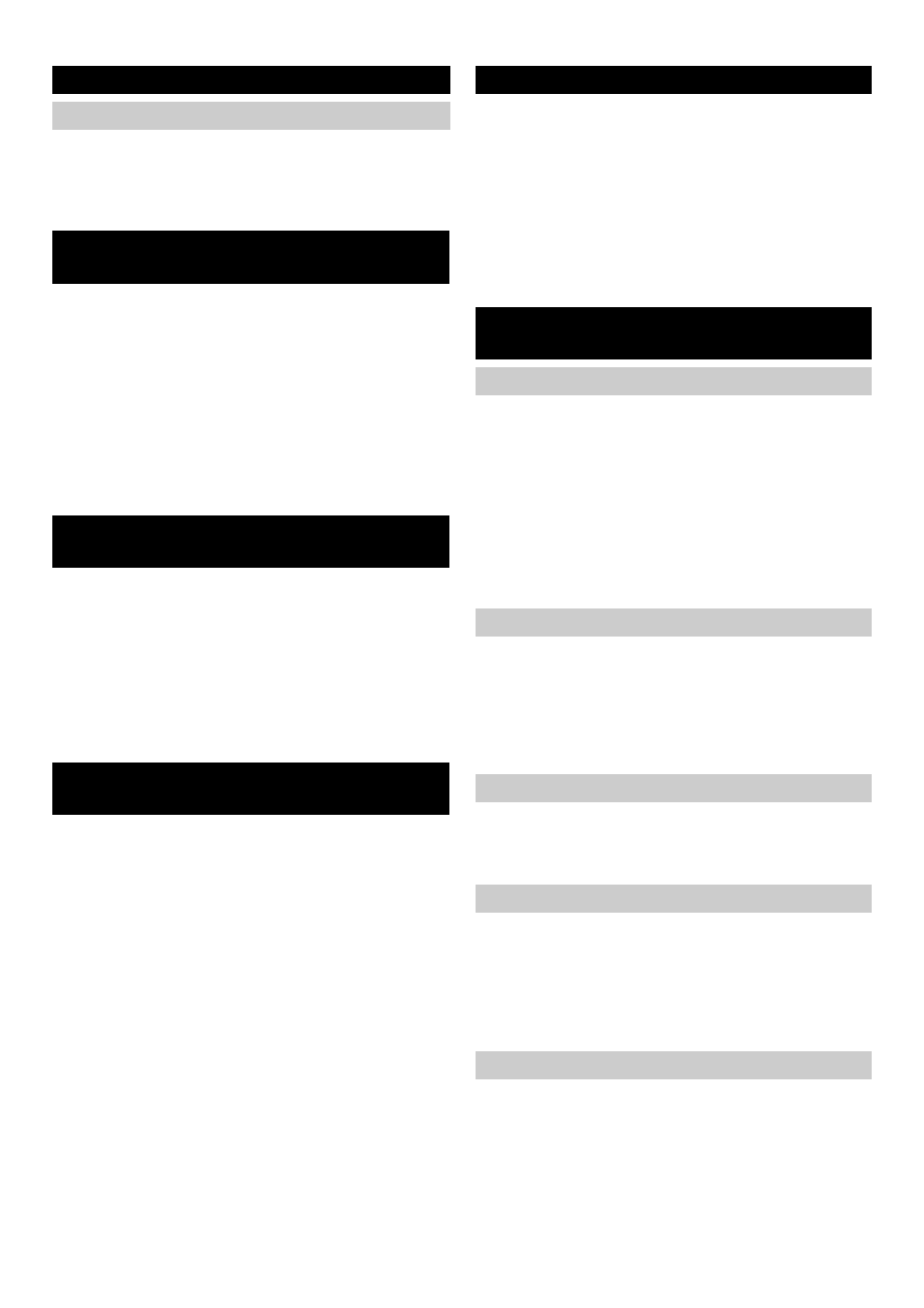
English 5.906-587.0 Rev. 00 (05/14)
5
CAUTION
Possible hazardous situation that could lead to mild injury
to persons or damage to property.
Note
Indicates useful tips and important information.
–
If the area to be vacuumed is locally fixed.
–
If there is little space available at the working area.
–
If the working areas are laid out over a large area and
several vacuuming points are therefore required.
–
If the possible cleaning times must be limited due to the
production continuity
–
If set-up and maintenance times are to be minimised.
–
If the work environment must be kept hygienically
clean.
–
If engine noises must be minimised in the working area.
–
If large amounts of dust or fluid must be continuously
disposed of.
Typical target groups for stationary vacuuming systems:
–
Food industry
–
Processing of metal and steel
–
Processing of glass and stone
–
Production of paper
–
Production of starch and tobacco
–
Textile industry
–
Automobile industry
–
Construction
–
Transport
–
Immediately ready for operation, no set-up times.
–
Space-saving, only the vacuuming accessories are at
the work station.
–
Comfortable to use and safe to operate.
–
Central suction unit and emptying at one point, thus,
space-saving and time-saving during maintenance.
–
Long service life as parts transporting materials are
made of robust, sturdy material.
–
Saving of costs thanks to the lower maintenance cost
of the entire system compared to several single sys-
tems.
–
Saving of costs thanks to the acquisition costs com-
pared to single systems.
1 Description of the requirements and evaluation of the
situation of the customer.
2 Based on the known amount of material and material
characteristics to be vacuumed up, the number and
size of the vacuuming points and the resulting required
air speed is determined.
3 Planning of the routing.
4 Calculation of the pressure loss in the network with the
objective to optimise the line design
5 Matching with the vacuum cleaner types and detailed
planning of the routing.
–
All Kärcher industrial vacuums.
–
Wet / dry vacuum cleaner and liquid aspirator.
–
Explosion-proof vacuum cleaners are only certified for
the operation with defined hose lines.
The certification comprises a test of the total resistance
in the system (vacuum cleaner without accessories)
For a stationary system this can not be performed in ad-
vance.
If a customer requires an explosion-proof stationary
system, the installed system must be certified in a sin-
gle acceptance inspection by the named authority.
–
Container sizes and types as per the current main cat-
alogue.
–
The pre-separator system (as per main catalogue) with
80 l container or for drums can also be used as a dis-
posal container (observe nominal diameter).
–
Disposal bags in various designs as per main cata-
logue.
–
All IV- and IVC vacuum cleaners have an integrated cy-
clone preseparator.
–
Filter data of the main filters such as surface, material,
order number, etc. as per main catalogue.
–
4 Standard diameter:
DN 60, DN 80, DN 100 and DN 120
–
Modular system with flanged pipes and tension ring
connections.
Thus, flexible replacement and extension.
–
In galvanised steel or stainless steel (1.4301)
–
System is suitable for dusts, chips and fluids.
–
Hose suspension with limit switch for the automatic
switch-on of the vacuum cleaner.
–
Kärcher remote control for controlling the suction unit at
the vacuuming point.
1
Safety instructions
1.1
Hazard levels
2
When is a central vacuuming system
used?
3
Target groups for a central
vacuuming system
4
Advantages of a stationary
vacuuming system
5
Abstract of the system planning
6
Components of a stationary
vacuuming system
6.1
Suction unit
6.2
Collection and disposal container
6.3
Filter
6.4
Formed parts pipeline
6.5
Hose connections and switches