Horner APG XLe OCS HE-XE102-62 User Manual
Page 3
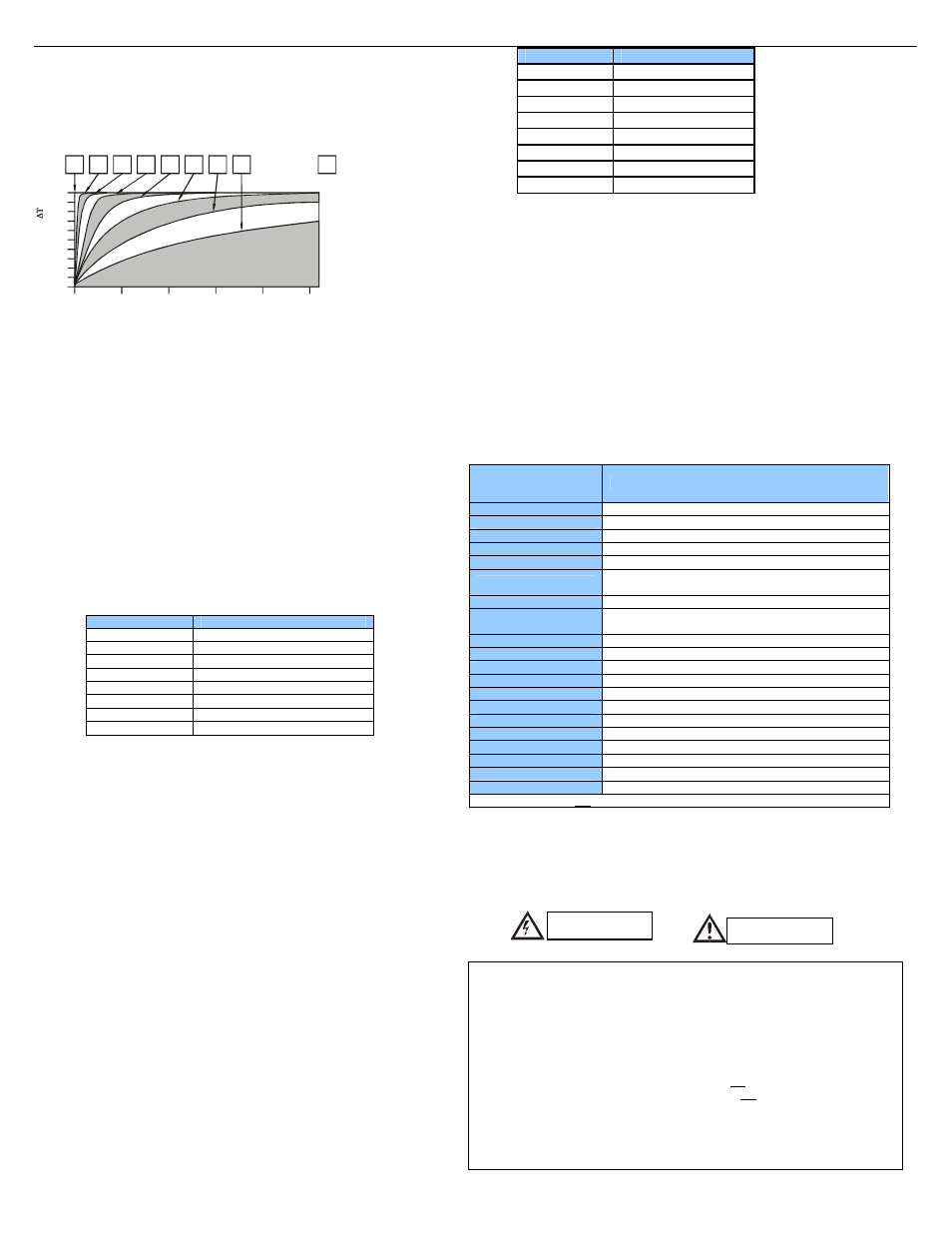
MAN0907-01-EN
Specifications / Installation
__________________________________________________________________________________________________________________________________________________________________________
7/22/2009 Page 3 of 4 ECN # 958
7
Analog Conditioning
7.1
Filter
Filter Constant sets the level of digital filtering according to the following chart.
Digital Filtering. The illustration above demonstrates the effect of digital filtering
(set with Filter Constant) on module response to a
temperature change.
It is recommended that the filter constant for the HE-XE103-10 be set to a value
of 7. This will minimize noise and jitter, improve effective resolution, and provide
adequate speed for most temperature monitor and control applications.
7.2
Sensor Linearization
7.2.1
ES2T-250/300 Channel 1
Linearization must be performed by the user in the ladder application code, using
26 internal %R registers per channel. The example below uses %R1-26 to
linearize one channel - %AI1. Linearization consists of the following example
steps.
1)
1) Load the desired linearization coefficients into a table on first scan
using a Move Constant Data block.
Registers (Real)
Degrees F
R0011
-1.56518643899245e-27
R0013
+1.85504500007145e-22
R0015
-8.93939520118636e-18
R0017
+2.24997847156420e-13
R0019
-3.16779760556092e-09
R0021
+2.49133478160033e-05
R0023
-1.08497438404356e-01
R0025
+3.42114564669736e+02
2)
Load %AI0001 into %R0001 as a Real.
3)
Perform the Real Math Expression
4)
%R3 = (((%R11*%R1+%R13)*%R1+%R15)*%R1+%R17)
5)
Perform the Real Math Expression %R5 =
(((%R3*%R1+%R19)*%R1+%R21)*%R1+%R23)*%R1+%R25
6)
Load %R0005 result into another register such as %R0007 to save
the temperature value.
7)
Steps 2 though 5 can be on a single rung.
7.2.2
ESP-100 Channel 2
Linearization must be performed by the user in the ladder application code, using
26 internal %R registers per channel. The example below uses %R31-57 to
linearize one channel - %AI2. Linearization consists of the following example
steps.
1) Load the desired linearization coefficients into a table on first scan using
a Move Constant Data block.
Registers (Real)
PSIG
R0031
+3.78384517359524e-28
R0033
-1.95900825431083e-23
R0035
+4.60841168052757e-19
R0037
-5.69061024051414e-15
R0039
+4.02188808100642e-11
R0041
-2.87389870540659e-07
R0043
-6.13292635022654e-03
R0045
+1.28157611098246e+02
2) Load %AI0002 into %R00051 as a Real.
3) Perform the Real Math Expression
4) %R53 = (((%R31*%R51+%R33)*%R51+%R35)*%R51+%R37)
5) Perform the Real Math Expression %R55 =
(((%R53*%R51+%R39)*%R51+%R41)*%R51+%R43)*%R51+%R45
6) Load %R00055 result into another register such as %R00057 to save the temperature
value.
7) Steps 2 though 5 can be on a single rung.
Contact Horner APG Technical Support for an example file containing the above program.
8
I/O Register Map
Registers
Description
%I1 to %I24
Digital Inputs
%I32
Output Fault
%I25 to %I31
Reserved
%Q1 to %Q16
Digital outputs
%Q17
Clear HSC1 accumulator to 0
%Q18
Totalizer: Clear HSC2
Quadrature 1-2: Accumulator 1 Reset to max – 1
%Q19
Clear HSC3 Accumulator to 0
%Q20
Totalizer: Clear HSC4
Quadrature 3-4: Accumulator 3 Reset to max – 1
%Q21 to %Q32
Reserved
%AI1 to %AI4
Analog inputs
%AI5, %AI6
HSC1 Accumulator
%AI7, %AI8
HSC2 Accumulator
%AI9, %AI10
HSC3 Accumulator
%AI11, %AI12
HSC4 Accumulator
%AQ1, %AQ2
PWM1 Duty Cycle
%AQ3, %AQ4
PWM2 Duty Cycle
%AQ5, %AQ6
PWM Prescale
%AQ7, %AQ8
PWM Period
%AQ9 to %AQ14
Analog outputs
Note: Not all XLe units contain the I/O listed in this table.
9
Safety
60
20
100
40
80
20
0
10
100
90
80
70
60
50
40
30
Scans
0
1
2
3
4
5
6
0
7
%
C
o
m
p
le
te
[
]
Filter
Constant
WARNING: To avoid the risk of electric shock or burns, always connect the safety (or
earth) ground before making any other connections.
WARNING: To reduce the risk of fire, electrical shock, or physical injury it is strongly
recommended to fuse the voltage measurement inputs. Be sure to locate fuses as
close to the source as possible.
WARNING: Replace fuse with the same type and rating to provide protection against
risk of fire and shock hazards.
WARNING: In the event of repeated failure, do not replace the fuse again as a
repeated failure indicates a defective condition that will not clear by replacing the fuse.
WARNING: Only qualified electrical personnel familiar with the construction and
operation of this equipment and the hazards involved should install, adjust, operate, or
service this equipment. Read and understand this manual and other applicable
manuals in their entirety before proceeding. Failure to observe this precaution could
result in severe bodily injury or loss of life.
Warning: Consult
user documentation.
Warning: Electrical
Shock Hazard.
When found on the product, the following symbols specify: