DME Hydraulic Locking Core Pull Cylinders User Manual
Page 7
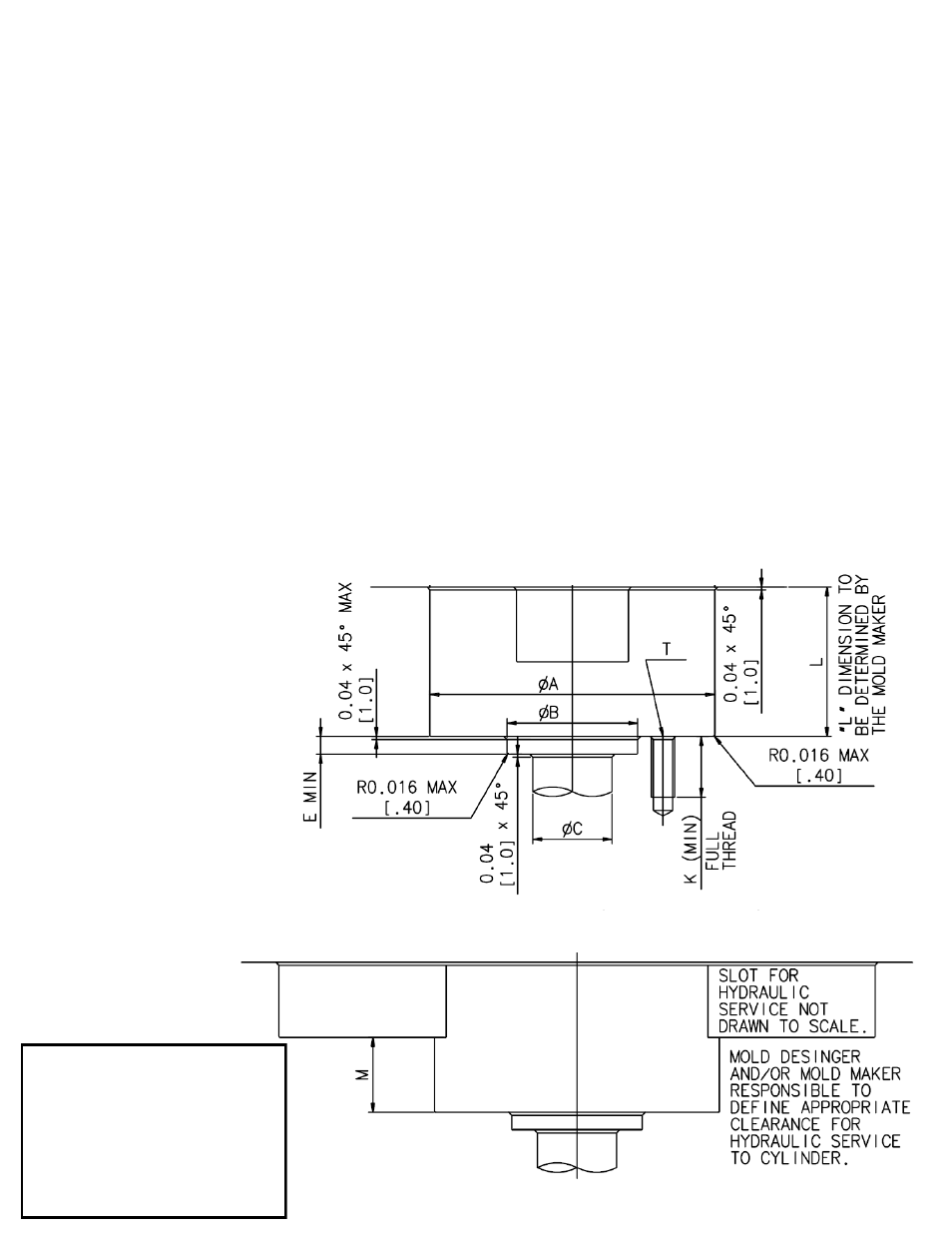
DME HYDRAULIC LOCKING CORE PULL CYLINDERS
Specification No. ME-E32-0001(C)
Part No. HLCP-PS01
Page 7 of 12
NOTICE:
DME shall not be liable for misuse or failure
to follow the enclosed instructions and
specifications. DME hereby disclaims all
implied warranties, including merchantability
and fitness for a particular purpose. In no
event shall DME be responsible for loss of
use, revenue or profit, or for incidental or
consequential damages.
Important:
The suggested installation pocket
details show two “slots” (please refer
to Section B-B and the appropriate
Plan View). The slot described for the
proximity switch (signaling full forward
position of the piston rod) is a minimum
requirement but can be made larger if
required. The slot shown for hydraulic
service is only a representation, and
the mold maker and/or mold designer
is responsible to provide appropriate
clearance for the actual hydraulic
service (fittings, hoses, etc) that will
be used with the intended mold and/or
application.
DETAIL 3.4: SUGGESTED POCKET DETAIL — SECTION VIEW B-B (ALL SIZES)
INSTALLATION INSTRUCTIONS:
If preload is required on the piston rod and sliding core (when shutting off on an opposing core face or wall), ensure the spacer disk provided has been
properly adjusted to ensure the recommended preload is achieved.
Insert the modified (adjusted) spacer disk into the cylinder assembly installation pocket in the mold plate.
Insert the cylinder assembly into the installation pocket, and fasten the cylinder assembly to the mold plate using the mounting screws provided. Take
care to use recommended torque settings.
If the sliding core must be attached to the piston rod after the cylinder assembly has been attached to the mold plate, please connect the sliding core to
the piston rod at this time.
Attach all hydraulic service hoses and fittings to the cylinder assembly. Attached service hoses to the hydraulic service system or equipment. Ensure
870 PSI minimum hold pressure is available at all times.
If proximity sensors are included and used with this device, ensure the sensors are connected to the desired monitoring equipment and/or to the injection
molding machine. If different limit switches are used in place of the product’s proximity sensors, make sure that those limit switches are installed and
connected to the desired monitoring equipment and/or to the injection molding machine. For either method, it is important to ensure that the proximity
sensors or limit switches are functioning and monitored properly. Note: Power (electrical service) is required to operate the proximity sensors.
For cylinder sizes larger than the HLCP060 and HLCP100 sizes, a cap sensor bushing (with nut) and body sensor bushing (with nut) are used to retain
the proximity sensors to the cylinder assembly. Ensure sufficient pocket clearance is present.
Details 3.0 through 3.2 show the suggested plan view pocket installation. The suggested installation varies by cylinder assembly size, as different sizes
use different quantities of mounting screws. See chart on following pages for all suggested dimensions and mounting screw thread size.
Recommended torque values for assembly and mounting screws are shown in the BOM (Bill of Materials) for each HLCP cylinder size and stroke.
DETAIL 3.3: SUGGESTED POCKET DETAIL — SECTION VIEW A-A (ALL SIZES)
NOTE:
IN DETAILS 3.3 — 3.4,
WHERE SHOWN,
DIMENSIONS ARE IN
INCHES [MILLIMETERS]
SLOT FOR
PROXIMITY
SENSORS