DME Hydraulic Locking Core Pull Cylinders User Manual
Page 4
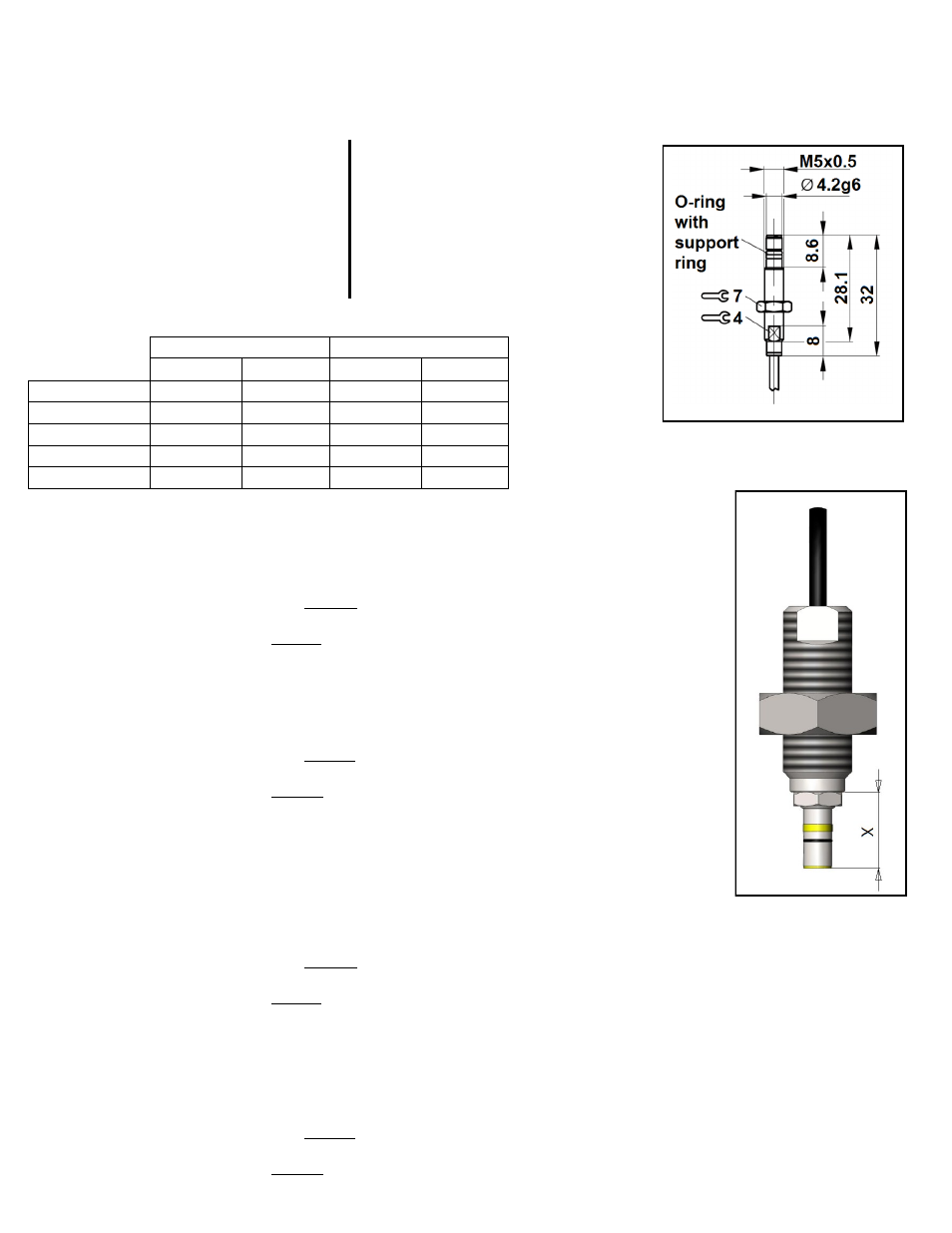
DME HYDRAULIC LOCKING CORE PULL CYLINDERS
Specification No. ME-E32-0001(C)
Part No. HLCP-PS01
Page 4 of 12
PROXIMITY SWITCH ELECTRICAL DATA:
Switching Output:
BHS006Y = NPN (Standard), BHS006U = PNP (Special)
Connection
2 m Cable (PUR)
Utilization category
DC 13
Ripple max. of Ue
10 %
Rated operational voltage (Ue)
24 DC V mm
Operating frequency (f)
3000 Hz
Load current capacity (Ie)
100 mA
Voltage drop max. static
2.5 V
Hysteresis max (H)
15 %
No-load supply current damped
10 mA
Switching element function
NO
No-load supply current undamped
7 mA
Time delay before availability
25 ms
Off-state current max (Ir)
100 μA
Electrical type
DC
Supply voltage max. (Ub)
30 V
Load capacitance max
0.4 μF
Supply voltage min. (Ub)
10 V
PROXIMITY SENSOR INSTALLATION INSTRUCTIONS:
TABLE 2.0:
DIMENSION “X”
NOTE: These sensors require power to produce a signal. This includes during installation/setup and during normal
operation. Refer to power requirements (above). Customer is responsible to provide power service to operate sensors.
If only dry contacts are present on the injection molding machine, see next page for suggested wire-up.
A) HLCP060 & HLCP100
Rear sensor in the CAP:
1. Make sure the CYLINDER ROD is in the fully extended position.
2. Install the SENSOR into the CAP and slowly advance until the signal is lost. Be careful not to overshoot the lost position.
3. Return the CYLINDER ROD to the fully retracted position.
4. If the signal is still lost, continue to advance the SENSOR until it produces the signal again.
Advance the SENSOR one additional quarter turn.
5. Tighten the 7mm nut on the SENSOR to a torque setting of 1.0 Nm (8.9 in. lbs) to secure the SENSOR to the CAP
B) HLCP060 & HLCP100
Front sensor in the BODY:
1. Make sure the CYLINDER ROD is in the fully retracted position.
2. Install the SENSOR into the BODY and advance until the signal is lost. Be careful not to overshoot the lost position.
3. Return the CYLINDER ROD to the fully extended position.
4. If the signal is still lost, continue to advance the SENSOR until it produces the signal again.
Advance the SENSOR one additional quarter turn.
5. Tighten the 7mm nut on the SENSOR to a torque setting of 1.0 Nm (8.9 in. lbs) to secure the SENSOR to the BODY.
C) HLCP150 - HLCP750
Rear sensor in the CAP:
1. Assemble the SENSOR into the CAP SENSOR BUSHING as shown in DETAIL 2.1. The X dimension is found in
TABLE 2.0. Once the X dimension is set, use a torque setting of 1.0 Nm (8.9 in. lbs.) to secure the position of
the SENSOR inside the CAP SENSOR BUSHING.
2. Make sure the CYLINDER ROD is in the fully extended position.
3. Install the SENSOR and CAP SENSOR BUSHING into the CAP and tighten until the signal is lost. Be careful not to overshoot the lost position.
4. Return the CYLINDER ROD to the fully retracted position.
5. Continue to tighten the CAP SENSOR BUSHING until it produces the signal again. Tighten the SENSOR BUSHING one additional quarter turn.
6. Tighten the nut on the CAP SENSOR BUSHING to a torque setting of 17.0 Nm (12.6 ft. lbs) to secure the CAP SENSOR BUSHING to the CAP.
D) HLCP150 - HLCP750
Front sensor in the BODY:
1. Assemble the SENSOR into the BODY SENSOR BUSHING as shown in DETAIL 2.1. The X Dimension is found in TABLE 2.0. Once the X dimension is
set, use a torque setting of 1.0 Nm (8.9 in. lbs.) to secure the position of the SENSOR inside the CAP SENSOR BUSHING.
2. Make sure the CYLINDER ROD is in the fully retracted position.
3. Install the SENSOR and BODY SENSOR BUSHING into the BODY and advance it until the signal is lost. Be careful not to overshoot the lost position.
4. Return the CYLINDER ROD to the fully extended position.
5. Continue to advance the BODY SENSOR BUSHING until it produces the signal again. Advance the SENSOR BUSHING one additional quarter turn.
6. Tighten the nut on the BODY SENSOR BUSHING to a torque setting of 17.0 Nm (12.6 ft. lbs) to secure the BODY SENSOR BUSHING to the BODY.
DETAIL 2.1: PROXIMITY
SENSOR BUSHING & X DIMENSION
REAR (CAP END)
FRONT (FLANGE END)
[mm]
[inches]
[mm]
[inches]
HLCP150
11.1
0.44
11.1
0.44
HLCP200
18.8
0.74
11.1
0.44
HLCP300
11.1
0.44
14.4
0.57
HLCP500
14.5
0.57
18.5
0.73
HLCP750
13.5
0.53
15.0
0.59
DETAIL 2.0: PROXIMITY
SENSOR DIMENSIONS
(Shown in
Millimeters)