NORD Drivesystems BU0210 User Manual
Page 51
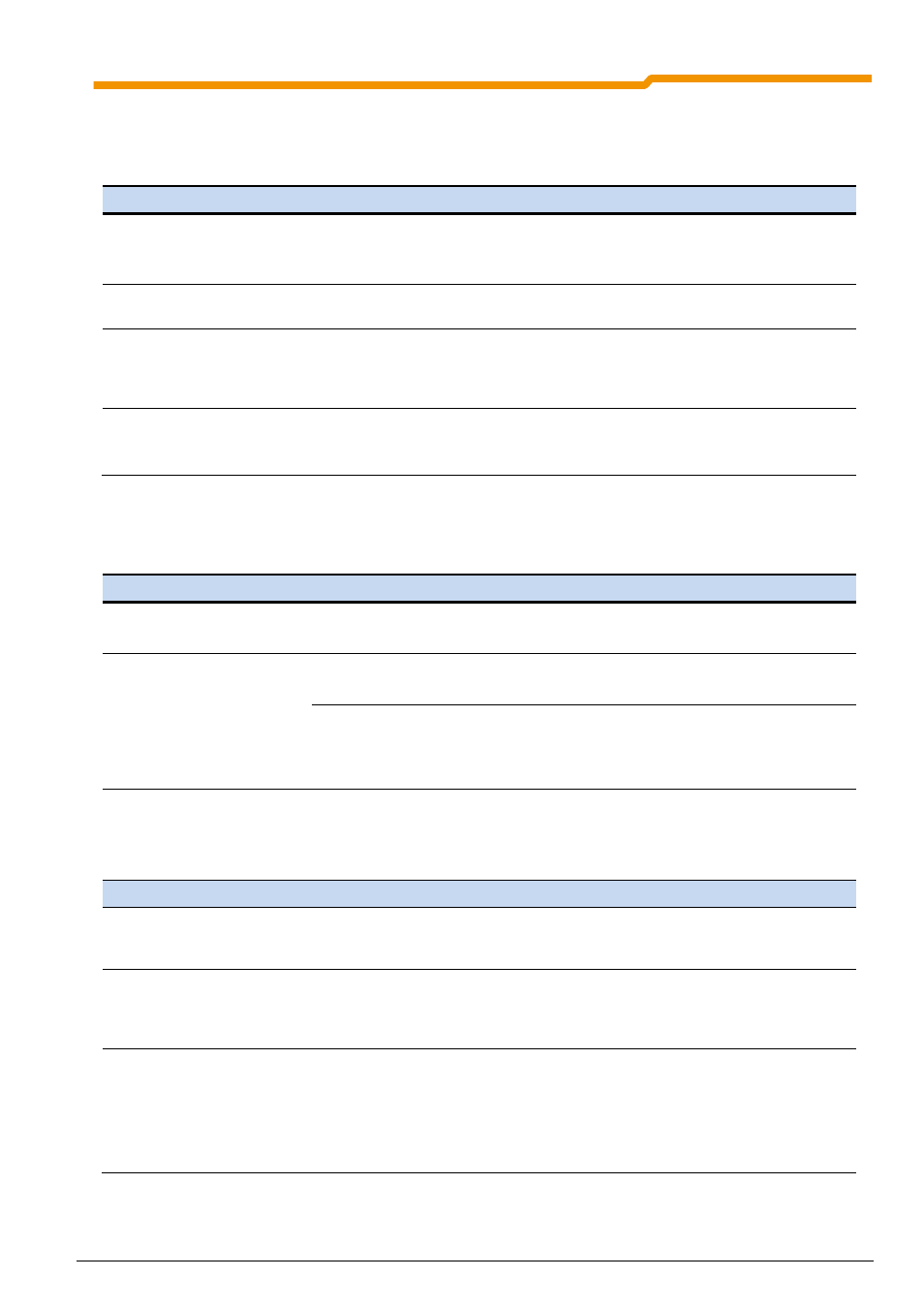
7 Troubleshooting
BU 0210 GB
Subject to technical amendments
51
7.2.2
General causes of faults
Symptom
Additional test
Possible cause
Position exceeded
Position control P amplification considerably too large
Speed control (servo mode) not optimally adjusted (Set
I-amp. to approx. 3%/ms, P-amp. to approx. 120%)
Drive oscillates at the
position
Position control P amplification considerably too large
Drive moves in the wrong
direction (away from the
setpoint position)
The direction of rotation of the absolute encoder does
not match the direction of rotation of the motor =>
parameterise an negative value for the speed ratio
(P607)
Drive unit sags away after
enabling is removed (lifting
gear)
Setpoint delay missing (control parameter);
for servo mode = "OFF" the control must be locked
immediately by the event "End Point Reached"
7.2.3
Special sources of faults for position control with incremental encoders
Symptom
Additional test
Possible cause
Position drifts away
Interference pulse in the encoder cable
No reproducible precision
when approaching the
position,
even at low speeds
(n < 1000 1/min)
Interference pulse in the encoder cable
only at high speeds
(n > 1000 1/min)
Pulse number in combination with the encoder
cable length / Cable type too large (Pulse frequency
too large)
Loose encoder / Installation fault
7.2.4
Special sources of faults for position control with absolute encoders
Symptom
Additional test
Possible cause
Actual position value always
runs to the same value and
then no longer changes
Encoder
connection
faulty
Position not always found at
the same place, axis
sometimes jumps
backwards and forwards.
Mechanical unevenness?
Axis stiff, axis jams etc.
Loose encoder / Installation fault
if the position value does not
match the encoder rotation
or jumps
Check absolute encoder
(remove, set parameter speed
and reduction ratio to 1, rotate
encoder manually: the displayed
position must match the rotations
of the encoder)
Encoder
defective