Profibus user manual – BEI Sensors PHU9 Absolute Hollow Shaft Encoder User Manual
Page 24
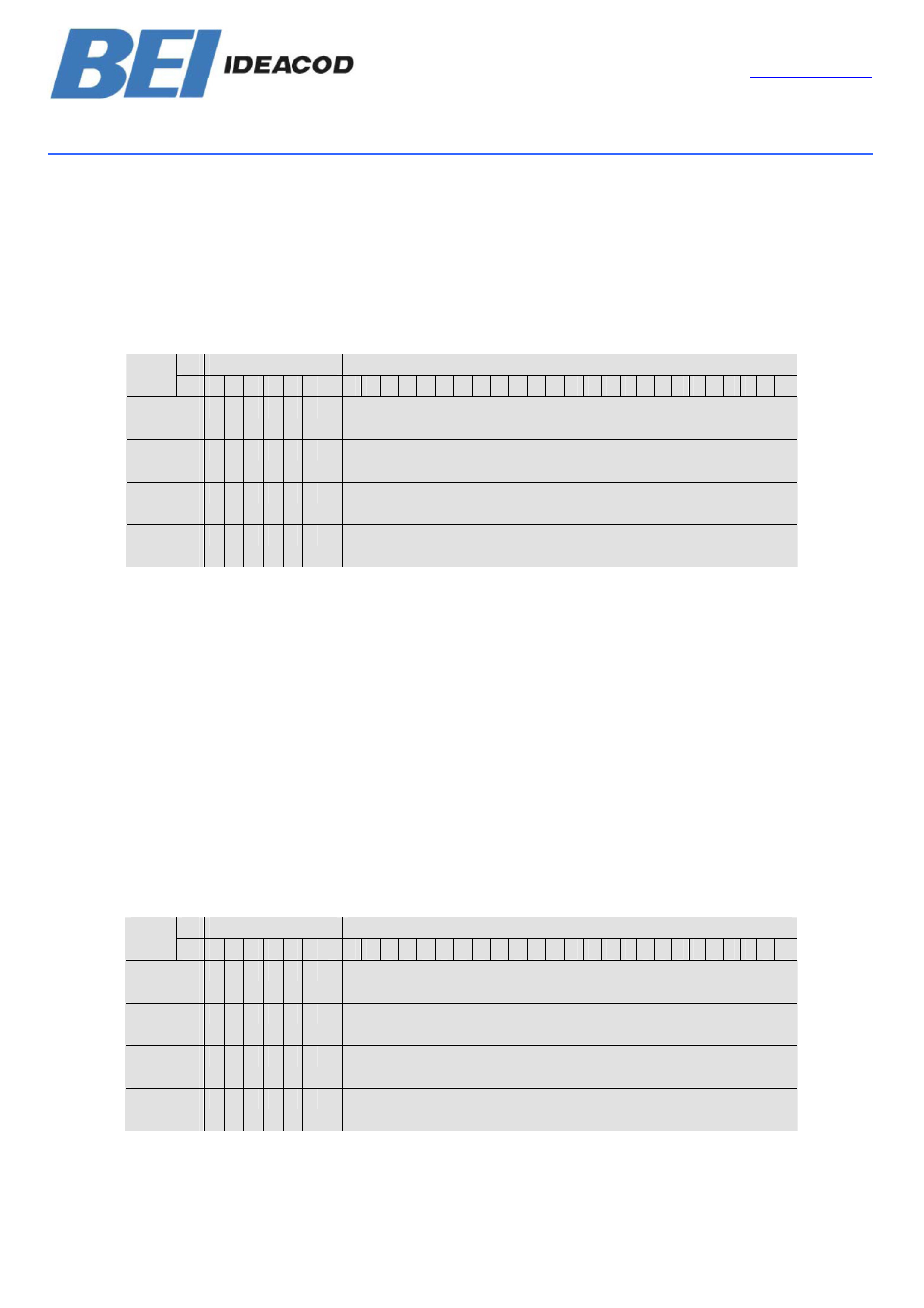
PROFIBUS USER MANUAL
24
Preliminary
BEI IDEACOD SAS
Espace Européen de l’Entreprise
9, rue de Copenhague
B.P. 70044 Schiltigheim
F 67013 Strasbourg Cedex
Tél
: +33 (0)3 88 20 80 80
Fax : +33 (0)3 88 20 87 87
Mail :
Web : www.bei-ideacod.com
5.3.2 Teach-In Start
After the machine / system has been moved
to the start-position the Teach-In-Start
command is transmitted to the encoder. The
device now starts the internal calculation of a
new scaling factor.
Status bits
Data bits
Bit
31 30 29
28 27 26 25 24 23 22 21 20 19 18 17 16 15 14 13 12 11 10 9 8 7 6 5 4 3 2 1 0
Master
slave
0
1 0 0 0 0 0 Start the Teach-In by setting bit 30 to 1
Slave
Master
0
1 0 X X 0 1 Acknowledgement of the encoder by setting bit 30 to 1
Master
slave
0
0 0 0 0 0 0 Reset bit 30
Slave
Master
0
1 0 X X 0 1 Non-calculated position value is transmitted (gearing factor = 1, no offset)
Note: The scaling factor is set to 1; the zero
point shift is set to zero.
5.3.3 Teach-In Stop
After moving the machine / system to the
stop-position the Teach-In-Stop command is
send. Together with this command the desired
number of steps over the moved measuring
range is transmitted. The user has to observe
that the physical resolution is not exceeded
(e.g. 20000 steps on a quarter of a revolution).
Positive and negative directions are taken into
account automatically, also the crossing of
the physical zero point. Note: The measuring
range must not exceed the half physical
measuring range of the encoder (i.e. a
maximum of 32767 revolutions for a multiturn
device with 65536 revolutions.
After receiving the Teach-In-Stop command
the encoder transmits the calculated total
resolution. This value should be noted and
later (when switching the device to normal
mode) entered into the parameter settings.
After this Teach-In procedure the encoder
operates with the new gearing factor (which is
stored non-volatile in the internal EEPROM).
Status bits
Data bits
Bit
31 30
29 28 27 26 25 24 23 22 21 20 19 18 17 16 15 14 13 12 11 10 9 8 7 6 5 4 3 2 1 0
Master
SLAVE
0 0
1 0 0 0 0 Number of desired measuring steps (on the traversed measuring range)
SLAVE
Master
0 1
1 X X 0 1 Transfer of the total resolution (should be noted)
Master
SLAVE
0 0
0 0 0 0 0 Reset bit 29
SLAVE
Master
0 0
0 X X 0 1 Output of the current position value, scaled with the new gearing factor