Bryant ASPAS1BBA015 User Manual
Page 112
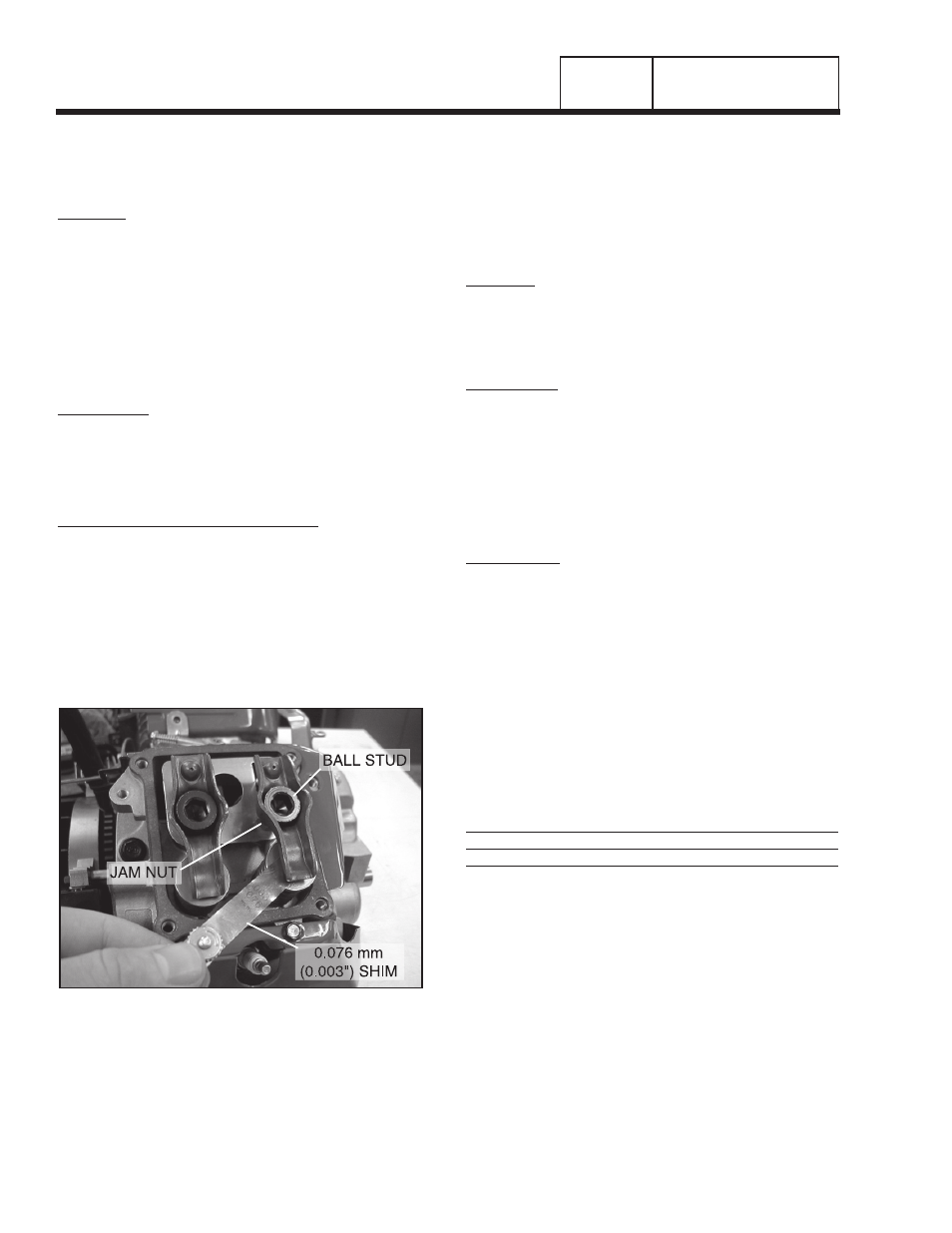
Page 112
SECTION 4.4
DIAGNOSTIC TESTS
DC CONTROL
PART 4
9. Heat the oil in the container. When the thermometer
reads approximately 274°-294° F. (134°-146° C.), the
VOM should indicate CONTINUITY.
RESULTS:
1. If the switch fails Step 4, or Steps 8-9, replace the
switch.
2. If INFINITY was not measured in Step 5, repair or
replace Wire 85 between the Circuit Board and the High
Oil Temperature Switch.
TEST 62 - CHECK AND ADJUST VALVES
DISCUSSION:
Improperly adjusted valves can cause various engine
related problems including, but not limited to, hard
starting, rough running and lack of power. The valve
adjustment procedure for both the single cylinder and
the V-twin engines is the same.
PROCEDURE (INTAKE AND EXHAUST):
Make sure that the piston is at Top Dead Center
(TDC) of it’s compression stroke (both valves closed).
The valve clearance should be 0.05-0.1mm (0.002-
0.004 in) cold.
Check and adjust the valve to rocker arm clearance
as follows:
1. Remove the four (4) screws from the rocker cover.
2. Remove the rocker cover and rocker cover gasket.
Figure 29
3. Loosen the rocker arm jam nut. Use a 10mm allen
wrench to turn the pivot ball stud and check the
clearance between the rocker arm and the valve stem
with a flat feeler gauge (see Figure 29).
4. When the valve clearance is correct, hold the pivot ball
stud with the allen wrench and tighten the rocker arm
jam nut. Torque the jam nut to 174 inch pounds. After
tightening the jam nut, recheck the valve clearance to
make sure it did not change.
5. Re-install the rocker cover gasket, rocker cover and the
four (4) screws.
RESULTS:
Adjust valve clearance as necessary, the retest.
TEST 63 - CHECK FUEL REGULATOR
DISCUSSION:
The fuel regulator is rarely the cause of a hard start or
no start condition. The most common causes are
insufficient fuel pressure supplied to the unit, or the
adjustment screws on the fuel regulator being out of
adjustment. The fuel regulator is an “ON DEMAND”
type. During cranking and running, negative pressure
from the airbox or carburetor unseats the fuel
regulator diaphragms and allows fuel flow through the
regulator.
PROCEDURE:
1. Turn off utility power to the main distribution panel in the
house. This can be done by switching the service main
breaker to the OFF or “Open” position.
2. Allow the generator to star t. Before loading the
generator, confirm that the No Load Frequency, with the
roof open and the door off, is set to 63-63.5 Hz. Transfer
load to emergency circuits.
3. Turn on appliances. lights, pumps, etc., that are on the
emergency circuits in an attempt to fully load the
generator. Be cautious not to overload the generator.
Use the following chart as a guide:
Unit
120 Volts
240 Volts
7 kW
50.0 amps
25.0 amps
12 kW
100.0 amps
50.0 amps
13/15 kW
108.3/125.0 amps
54.1/62.5 amps
4. When full load has been achieved, connect a frequency
meter to the output lugs of the generator main line
circuit breaker.
The fuel regulator is fitted with one (7 kW), or two (12 &
15 kW) adjustment screws. While watching the
frequency meter, slowly turn the adjustment screw(s)
clockwise or counterclockwise one at a time until
highest frequency is read on the meter.
Note: Only limited adjustment is available
between the set pins on 5fuel regulators. Under
no circumstance should any of the pins be
removed (see Figures 30 & 31).