HEIDENHAIN iTNC 530 (340 49x-06) User Manual
Page 499
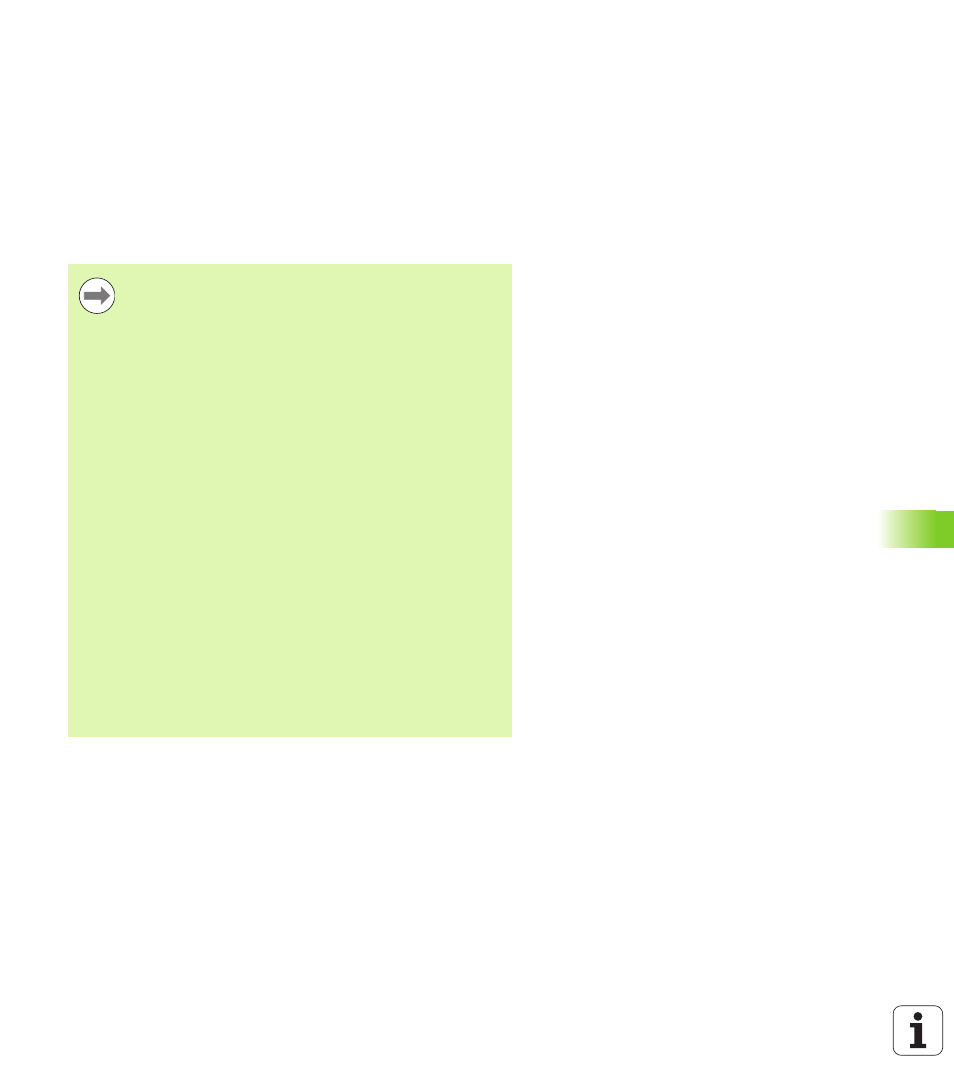
HEIDENHAIN iTNC 530
499
12.7 Cont
our Mo
v
e
ments — Spline Int
e
rp
olation (Sof
tw
ar
e Option
2)
The TNC executes the spline block according to the following third-
degree polynomials:
X(t) = K3X · t
3
+ K2X · t
2
+ K1X · t + X
Y(t) = K3Y · t
3
+ K2Y · t
2
+ K1Y · t + Y
Z(t) = K3Z · t
3
+ K2Z · t
2
+ K1Z · t + Z
A(t) = K3A · t
3
+ K2A · t
2
+ K1A · t + A
B(t) = K3B · t
3
+ K2B · t
2
+ K1B · t + B
whereby the variable t runs from 1 to 0. The incrementation of t
depends on the feed rate and the length of the spline.
Input ranges
Spline end point: -99 999.9999 to +99 999.9999
Spline parameter K: -9.99999999 to +9.99999999
Exponent for spline parameter K: –255 to +255 (whole number)
For every end-point coordinate in the spline block, the
spline parameters K3 to K1 must be programmed. The
end-point coordinates can be programmed in any
sequence within the spline block.
The TNC always expects the spline parameters K for each
axis in the sequence K3, K2, K1.
Beside the principal axes X, Y and Z, the TNC can also
process the secondary axes U, V and W, and the rotary
axes A, B and C. The respective corresponding axis must
then be programmed in the spline parameter K
(e.g. K3A+0.0953 K2A-0.441 K1A+0.5724).
If the absolute value of a spline parameter K becomes
greater than 9.99999999, then the post processor must
output K in exponential notation (e.g. K3X+1.2750 E2).
The TNC can execute a program with spline blocks even
when the working plane is tilted.
Ensure that the transitions from one spline to the next are
as tangential as possible (directional changes of less than
0.1°). The TNC otherwise performs an exact stop if the
filter functions are disabled, resulting in a jolting of the
machine tool. If the filter functions are active, the TNC
decreases the feed rate accordingly at these positions.
The spline starting point can deviate from the end point of
the previous contour by no more than 1 µm. Larger
deviations will provoke an error message.