Thermon TraceNet TCM 18 User Manual
Page 69
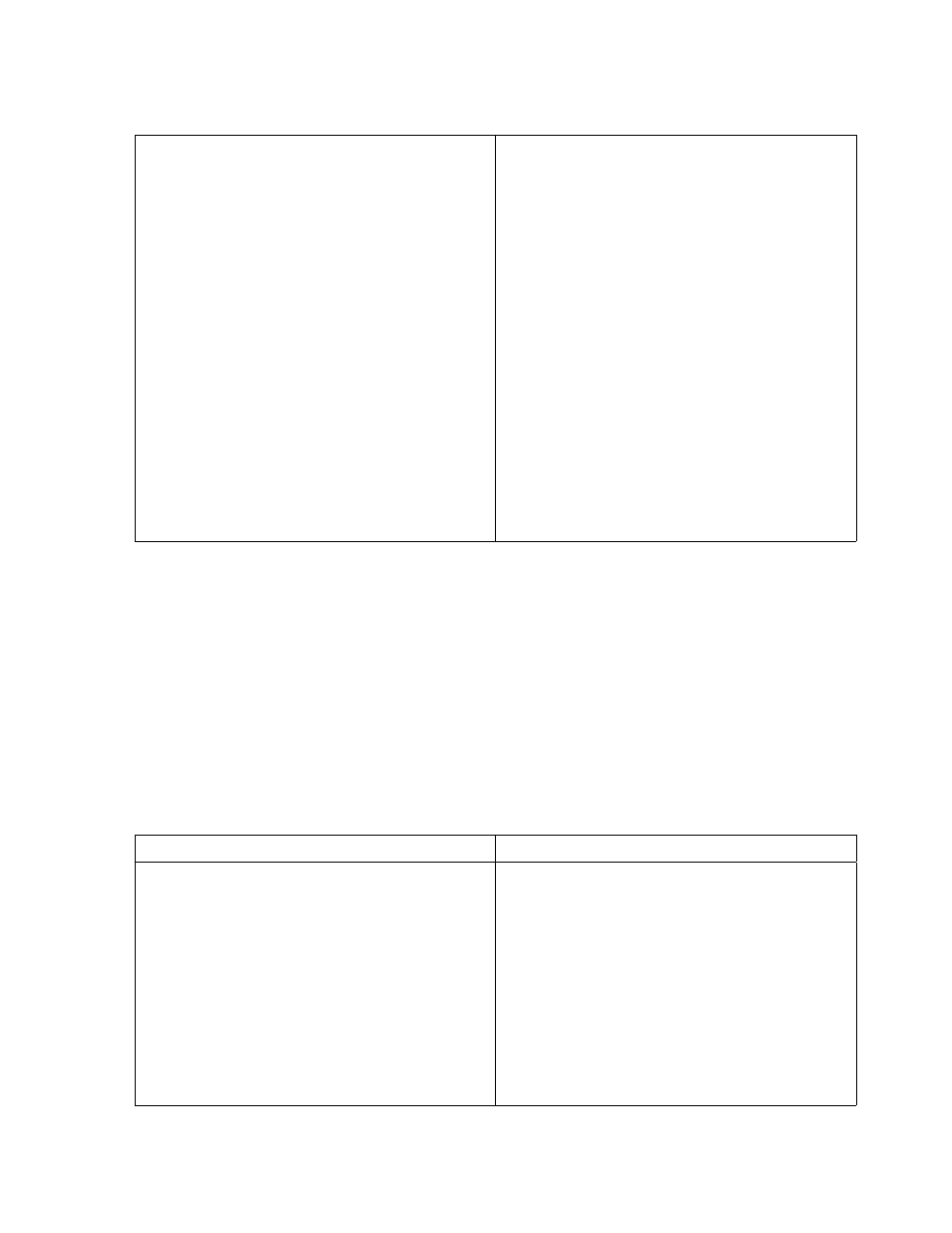
Heat tracing over designed in heat output
and or/ due to cable availability or natu-
ral design selections available. This can
result in higher than expected tempera-
tures due to overshoot (especially when
used with on-off control mode). This can
also occur in an ambient sensing control
modes.
Review design as well as installation in-
structions. Check heat tracing for pres-
ence of proper current. Since replacing
the circuit may not be a desirable op-
tion here, the first approach should be
to adjust the control method which the
TraceNet control system has been config-
ured in.
Heat tracing circuits are miswired such
that the RTD for circuit 1 is controlling cir-
cuit 2, etc.
Trace and recheck field and panel wiring.
Use circuit "turn -on " and "turn-off" tech-
nique or disconnect RTD’s one at a time to
see if the proper RTD failure alarm occurs
on the right circuit. Let process return to
normal condition or adjust alarm set point
(if approved by project engineer) to allow
for this processing condition.
Low Temperature Reading/Alarm
The following summarizes some of the possible causes and solutions for heat trac-
ing low temperature readings/alarms.
Cause
Possible Solutions
Temperature of product in process line
is below the alarm set point or expected
reading due to events other than heat
tracing-low pumping temperatures, etc.
Let process operations return to normal
conditions and then recheck for alarms.
Alternately adjust alarm set point (with
project engineers approval) to allow for
this process condition.
Low temperature alarm programmed set-
ting or expected reading did not consider
natural temperature undershoot associ-
ated with control scheme.
Move control set point up to allow for nat-
ural undershoot or lower the low temper-
ature alarm set point (when approved by
project engineer).
65
PN 50316_0514