Chapter 1: introduction, 1 overview – Sensoray 2600 User Manual
Page 6
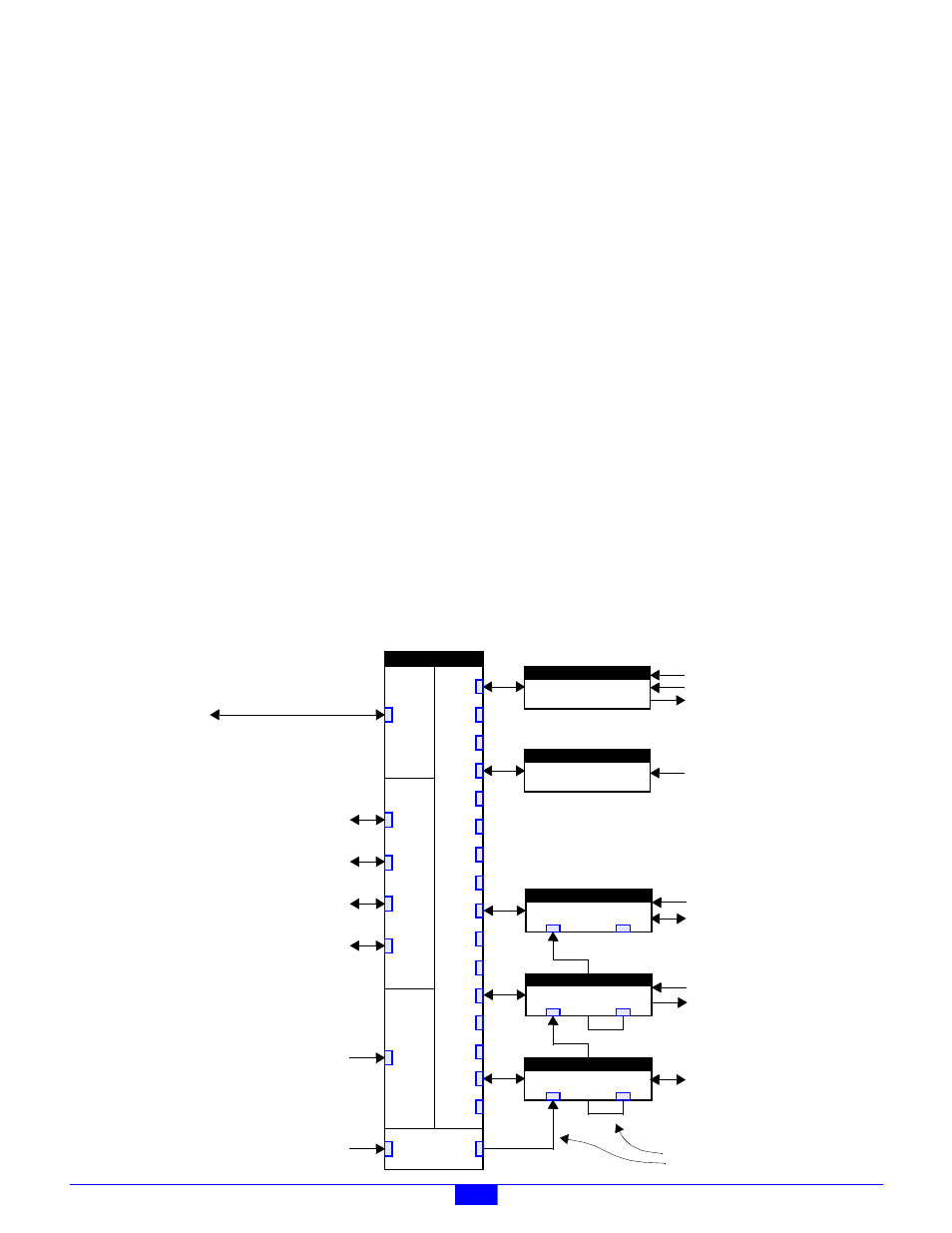
2600 Family Instruction Manual
1
Chapter 1 : Introduction
Chapter 1: Introduction
1.1 Overview
The Sensoray Model 2600 Real-Time Industrial I/O Network
is a low-cost, flexible system of DIN-rail mountable modules
that are interconnected by standard Category-5 cables. The
module system employs an Ethernet-based, client-server
architecture, in which a Main Module (MM) behaves as both a
four-channel serial communication server and as a gateway to
a cluster of up to sixteen intelligent I/O Modules (IOMs). A
virtually unlimited number of MMs may be connected to a
network.
The module system connects to an Ethernet client by means of
a low cost, 10BaseT/100BaseTX Ethernet interface. In
addition to providing a platform-independent interface, the
transformer-isolated Ethernet circuitry provides excellent noise
immunity by eliminating client-server ground loops.
A typical system (see Figure 1) consists of a MM and as many
as sixteen IOMs. Although the diagram depicts a specific
combination of IOMs, virtually any combination of IOMs may
be utilized in a system.
The MM employs a star topology to ensure that IOM faults
will not take down the network. Each of the MM’s sixteen
IOM ports distributes communications and fuse-protected
power to one IOM through a standard Category-5 cable. The
IOM port’s communication circuitry uses optical isolation to
eliminate ground loops, leading to superior reliability and
performance. IOMs may be safely connected to or
disconnected from the MM while power is applied to the
system.
In addition to its sixteen IOM ports, the MM provides four
asynchronous serial communication ports with RS-232,
RS-422 and RS-485 physical layer capabilities. Each port is
allocated 1KB transmit and 1KB receive buffers and operates
at standard baud rates up to 115.2 Kb/s.
Multiple power supply voltages and application interlock
contacts are easily accommodated by means of an interlock
power daisy-chain. Every module that requires auxiliary
power includes connectors for daisy-chaining the power to
other modules via cable assembly 2600C1. The MM includes
circuitry that enables the Ethernet client to monitor auxiliary
power status.
All modules incorporate robust, two-piece mating connectors
for quick, direct connection to field wiring. No external
termination boards are required.
Application software development is simplified with the aid of
distribution media that is supplied with module hardware at no
additional cost.
Figure 1: System Block Diagram
CT Module
8 SSRs
AIO Module
16 Analog Ins
4 Counters
SSR Module
24VDC
Thermocouples
±10V/100mV/4-20mA
RS-232/RS-422/RS-485
0-230V AC/DC
SSR I/Os
Encoders
4 Analog Outs
0-10V
8 Relays
RLY Module
0-230V AC/DC
Relay Outputs
DIO Module
48 Digital I/Os
Digital I/Os
MM Module
Ethernet
Client(s)
Cat5
Cat5
Cat5
Cat5
Cat5
Cat5
I
O
M
P
o
r
t
s
1
0
/
1
0
0
M
b
/
s
E
t
h
e
r
n
e
t
S
e
r
i
a
l
C
o
m
P
o
r
t
s
Interlock
Monitor
Interlock Power
P
o
w
e
r
S
u
p
p
l
y
a
n
d
D
i
s
t
r
i
b
u
t
i
o
n
Interlock Power
Daisy Chain (2600C1)
RS-232/RS-422/RS-485
RS-232/RS-422/RS-485
RS-232/RS-422/RS-485