Measurement Computing CIO-EXP-GP User Manual
Page 36
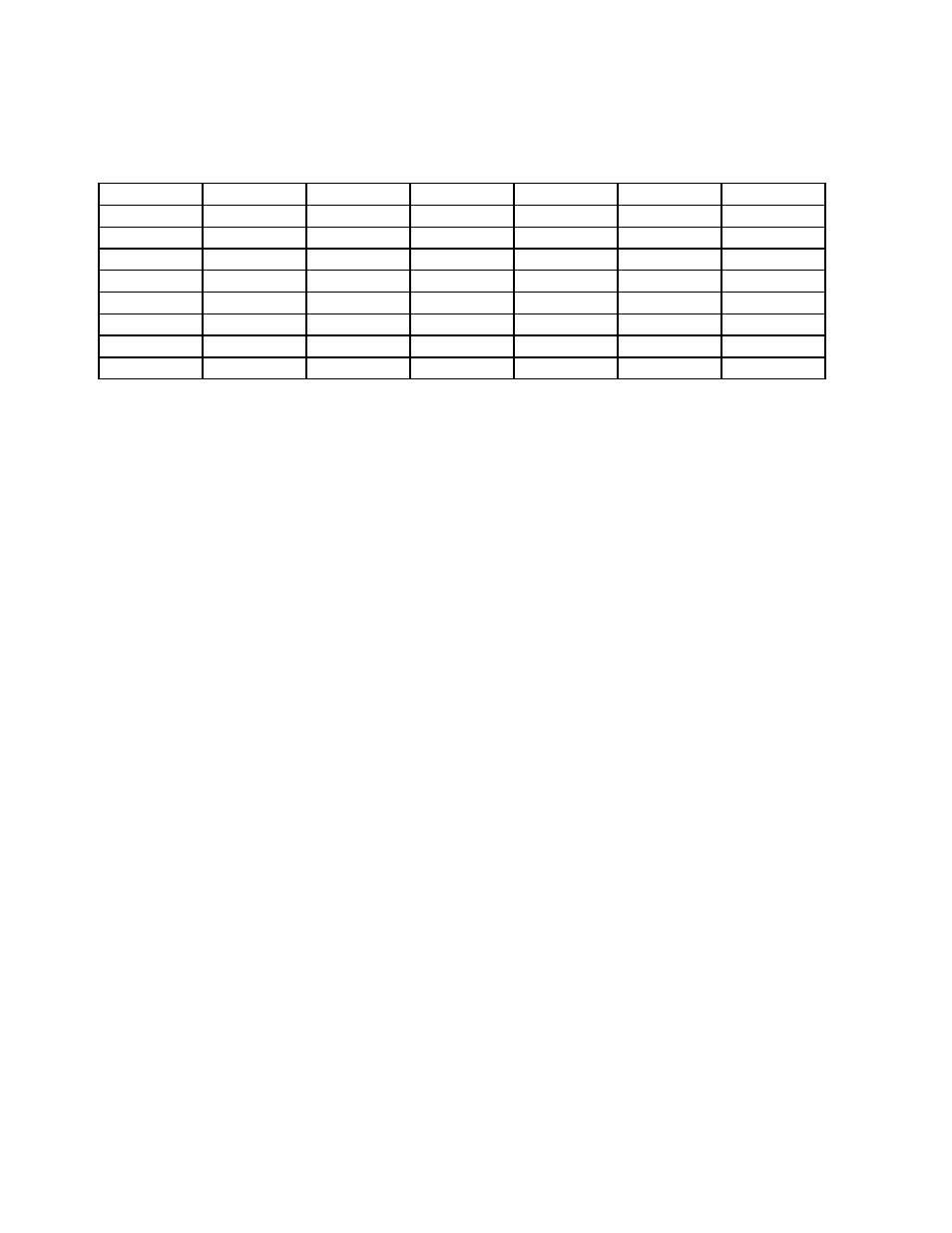
Referring back to Figure 7-6, the legs of the bridge are labeled A, B, C and D. Table 7-3 below matches
the legs of the bridge to the resistor number nomenclature that appears on the CIO-EXP-GP.
Table 7-3. Bridge Completion Resistor Identities
RX59
RX48
RX46
RX45
RX44
RX43
7
RX58
RX42
RX40
RX39
RX38
RX37
6
RX57
RX36
RX34
RX33
RX32
RX31
5
RX56
RX30
RX28
RX27
RX26
RX25
4
RX55
RX14
RX22
RX21
RX20
RX19
3
RX54
RX18
RX16
RX15
RX14
RX13
2
RX53
RX12
RX10
RX9
RX8
RX7
1
RX52
RX6
RX4
RX3
RX2
RX1
0
Arm
Null Pot
Bridge D
Bridge C
Bridge B
Bridge A
Channel
Some values of precision resistors are available from Measurement Computing Corp.
7.8.2
Nulling Potentiometers & Arm Resistor
Each circuit has a position for a nulling potentiometer and associated arm resistor. The purpose of the
nulling arm is to allow you to zero the reading of strain at a given strain position. There is no formula to
use to select the nulling potentiometer and arm resistor. Bridge resistor values and total gain selected for
the CIO-EXP-GP will affect adjustability for a given nulling circuit. An average value for the arm
resistor is 10k ohms. Start with that and adjust as required.
7.8.3
Strain Gauge Bridge Configuration Examples
Following are three typical strain gauge bridge configurations. They are by no means the only way to
connect a strain gauge to the CIO-EXP-GP. For example, there is no rule that says the ‘A’ leg must be
the strain gauge on a ¼ bridge implementation.
The examples below show how to translate strain to input voltage for the strain gauge
configuration used to measure simple bending strain. Other types of stress and strain: axial,
torsion, shearing , etc. are beyond the scope of this description.
These examples can be used to as a
guide for calculating the bridge voltage in your own application, and thus help you select the proper
amplifier gain and excitation voltage.
The use of quarter bridge, half bridge and full bridge strain gauge configurations are described.
The Application:
In these examples, imagine a beam extending out from a fixed point on a wall. Force is applied to deflect
the end of the beam downward. We know that the maximum strain to be measured will be 250µ
ε
(250
micro strain). Knowing the amount of force required and the size of the beam is not necessary, since
strain relates to the change in length of the surface of interest.
The Strain Gauge will be a metal foil type, 350 ohms resistance, Gauge Factor = 2. Refer to the
Appendix for information on these specifications.
The following example shows a bending strain measurement example. It can be used to calculate
the bridge voltage, and thus help the user select the proper amplifier gain and excitation voltage.
The use of one, two and four strain gauges will be examined.
32