Hpr800xd auto gas revision changes (806500) – Hypertherm HPR800XD Auto Gas Rev.2 User Manual
Page 367
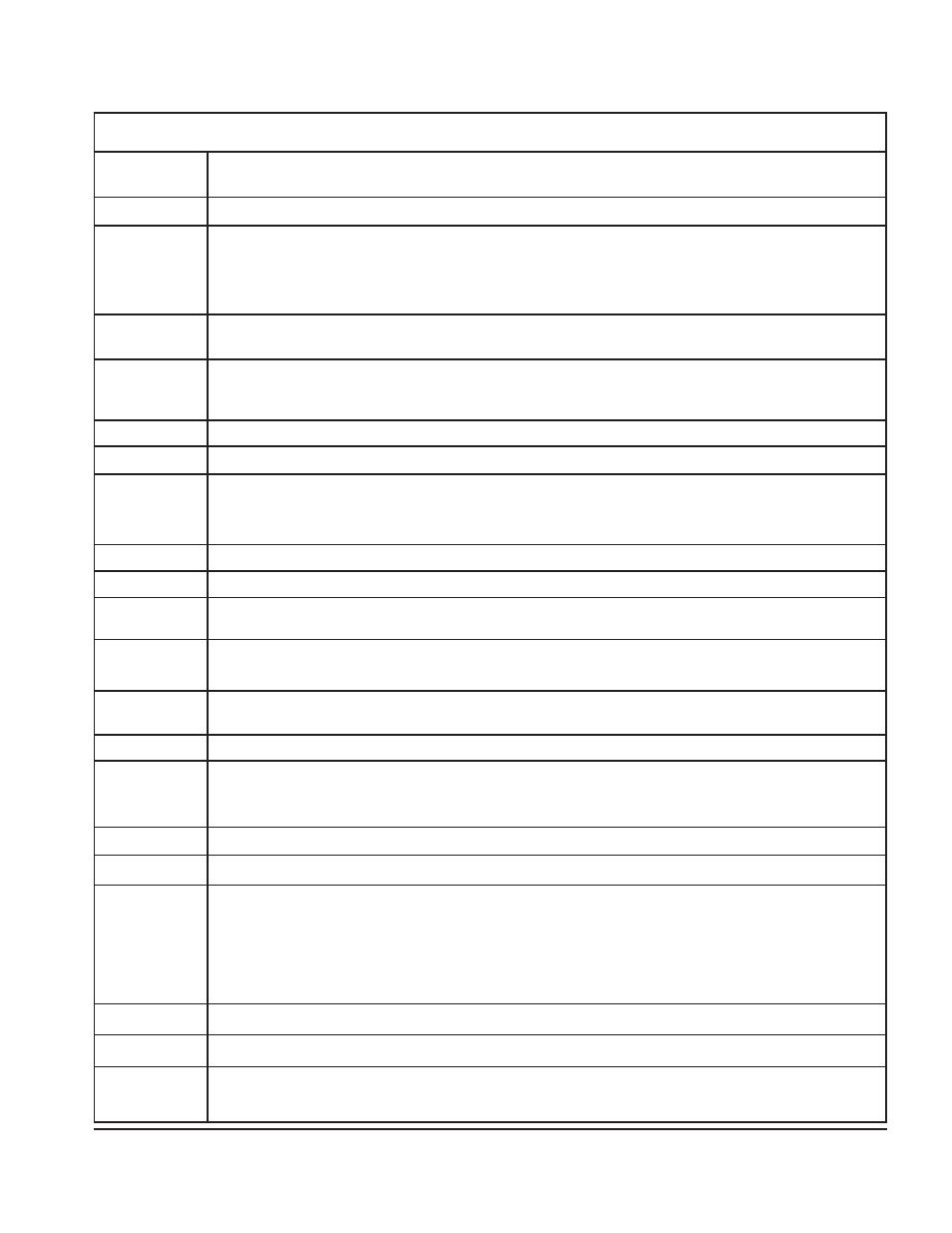
HPR800XD Auto Gas –
806500
1
HPR800XD auto gas revision changes (806500)
changed
Page
Description of changes for revision 2 (date of revision - 9/2011)
Global
Inch marks (“) have been replaced by the abbreviation (in).
EMC-1 through
W-2
Updated the format and information for both the Electromagnetic compatibility and Warranty sections.
Added Certification test marks, Differences in national standards, Higher-level systems, laser and
Automation products, and Proper disposal of Hypertherm products information to the
Warranty section.
Safety sections Updated the format and content of the safety information. Added Dry dust collection and Laser
radiation information.
2-4
Removed the note under the gas quality and pressure requirements table that said “Oxygen, nitrogen,
and air are required for all systems. Nitrogen is used as a purge gas.” The statement was inaccurate.
Corrected the kPa pressure from 827 kPa to 793 kPa.
2-5
Changed kW to kVA in the last column, “power”.
2-13
Added IEC symbol graphics and descriptions.
3-11
Added a paragraph before the bullet points with some details about moving the power supply with
a fork lift. Added “HPR400XD power supplies with serial number HPR400-000560 or later can be
upgraded to a HPR800XD primary or secondary power supply.” below the bullet points.
3-22
Corrected the communication cable part numbers.
3-23
Added part numbers for the pilot arc lead. They were accidentally left out in revision 0.
3-26, 33, 41,
57 and 59
Added caution box about not using PTFE tape.
3-55
Removed the note “Oxygen, air and nitrogen are required for all systems. Nitrogen is used as a purge
gas.” The statement is inaccurate. Removed the reference to methane because it is not used.
3-57
Added reference to supply gas hoses that are listed at the end of the section. Removed the reference
to methane because it is not used.
4-6 through 4-9 Updated CNC screen examples.
4-10
Added “When using the argon marking processes, mark and cut individual parts. Marking the entire
nest prior to cutting may lead to reduced consumable life. For better results intersperse cuts and
marks.” under Marking.
4-17 and 4-18 Expanded “Inspect consumables” from one page to 2. Increased size of graphics for clarity.
4-20
Added Torch quick disconnect receptacle graphic.
4-25
Added “(for example: 30 amp O
2
/O
2
and 50 amp O
2
/O
2
processes). The pierce complete signal
must be turned off for processes with shield gas preflow pressures that are lower than the cutflow
pressures (for example: 600 amp and 800 amp processes).” to the second paragraph. Added third
bullet point. Added “moving pierce”, (800 amp SST piercing can be extended to 100 mm (4 in), and
“an edge start is recommended unless the operator is experienced with this technique.” to the last
bullet point.
4-29 and 4-30 Updated kerf width compensation data. Populated empty boxes with N/A for not available.
4-31 and 4-32 Updated kerf width compensation table data. Populated empty boxes with N/A for not available.
4-41 and 4-42
Added “on the shield” to the note - They are only recommended for use if you have a problem with
excessive slag on the shield, or problems with the torch misfiring, when using the standard bevel
consumables.