Gasboy DEF Atlas User Manual
Page 14
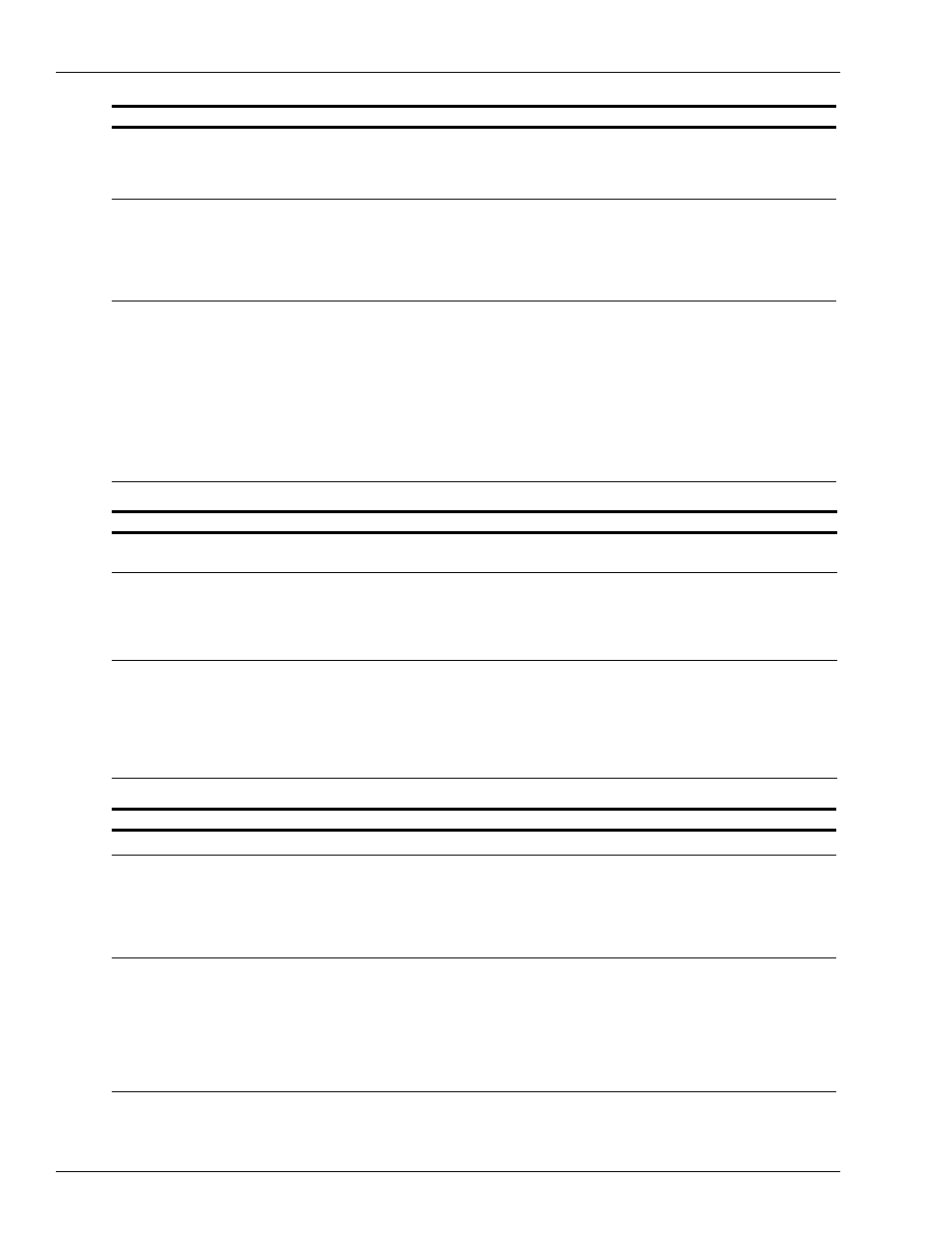
Page 4-2 MDE-5044A Atlas® DEF Operation, Diagnostics, and Recommended Spare Parts Manual · April 2014
DEF Dispenser Problems
Diagnostics, Calibration, and Troubleshooting
Problem 2: No product dispenses/flows.
Symptoms
• Dispenser electronically resets.
• Display shows all 0s.
• No error messages.
• No product dispenses.
Possible Causes
• Solenoid valve does not activate.
• 9800 CPU board does not send the AC signal to the solenoid valve or submersible motor in the tank.
• Bad submersible motor in the product’s tank.
• Bad coriolis meter interface board (possibly due to the coriolis meter).
• Bad nozzle.
• Check valve is stuck at the closed position.
Corrective Action
• Ensure to hear the solenoid valve opening.
• Feel the hose jump.
• Observe fast, slow, and sub LEDs on the 9800 CPU board.
• Check fast and slow fuses on the 9800 CPU board, replace if open.
• If the solenoid valve activates, check for proper AC signal at the sub fuse on the 9800 CPU board.
• Replace the fuse, if open. If the fuse is OK but there is no sub LED, replace the 9800 CPU board.
• If the 9800 CPU board displays a proper AC signal, open the inlet line to verify if the product flows when the
unit is on.
• Replace the submersible motor, if there is no product flow at the inlet.
• Verify if the check valve is not stuck at the closed position by loosening the inlet cap. Also, verify if the
product is present.
Problem 3: Dispenser does not calibrate.
Symptoms
• Display shows error code 993 on DEF unit.
• No product can be dispensed.
Possible Causes
• Air in product line needs to be purged.
• Product leak in the plumbing.
• Bad 9800 CPU board or program.
• Very low product level in the tank.
• Product contamination.
Corrective Action
• Verify that the tank is not low in product, request a delivery if the product level is low.
• Recalibrate the DEF unit by performing the calibration procedure described in MDE-4331 Atlas Fuel
Systems Installation Manual and MDE-4334 Commercial and Retail Series Atlas Start-up/Service Manual.
• Dispense product until there is no visual evidence of air in the product (may take two to three prover cans).
• Check for any product leaks in all the product lines and the internal plumbing. Correct the leaks, if visible.
• Verify that the filter is clean and free of debris.
• Change the 9800 CPU board, if all of the above fails.
Problem 4: DEF unit dispenses product very slowly, slow flow.
Symptoms
• No error messages appear, but the product dispenses very slowly as in slow flow mode.
Possible Causes
• Dirty filter, product contamination.
• Check valve not opening completely.
• Defective solenoid valve.
• Defective 9800 CPU board.
• Defective submersible motor in tank.
• Defective nozzle filter or the nozzle.
Corrective Action
• Remove inlet filter and replace, if dirty.
• On the 9800 CPU board, measure for 115 VAC on both sides of the fast flow fuse (F2).
• If AC is not present, perform a continuity test across the F2 fuse. Replace the fuse, if open.
• If the F2 fuse is not open, replace the 9800 CPU board.
• If 115 VAC is present on the blue and black wire on the two stage solenoid valve, replace the solenoid
valve.
• Check the submersible motor to see if the running is at full speed due to low voltage or defective motor.
• DEF nozzle could restrict the flow (remote possibility), replace the nozzle and retry dispensing the product.