13 description, 1 introduction, 2 functional modules – Bronkhorst FLOW-SMS Series User Manual
Page 10: 3 flow modules
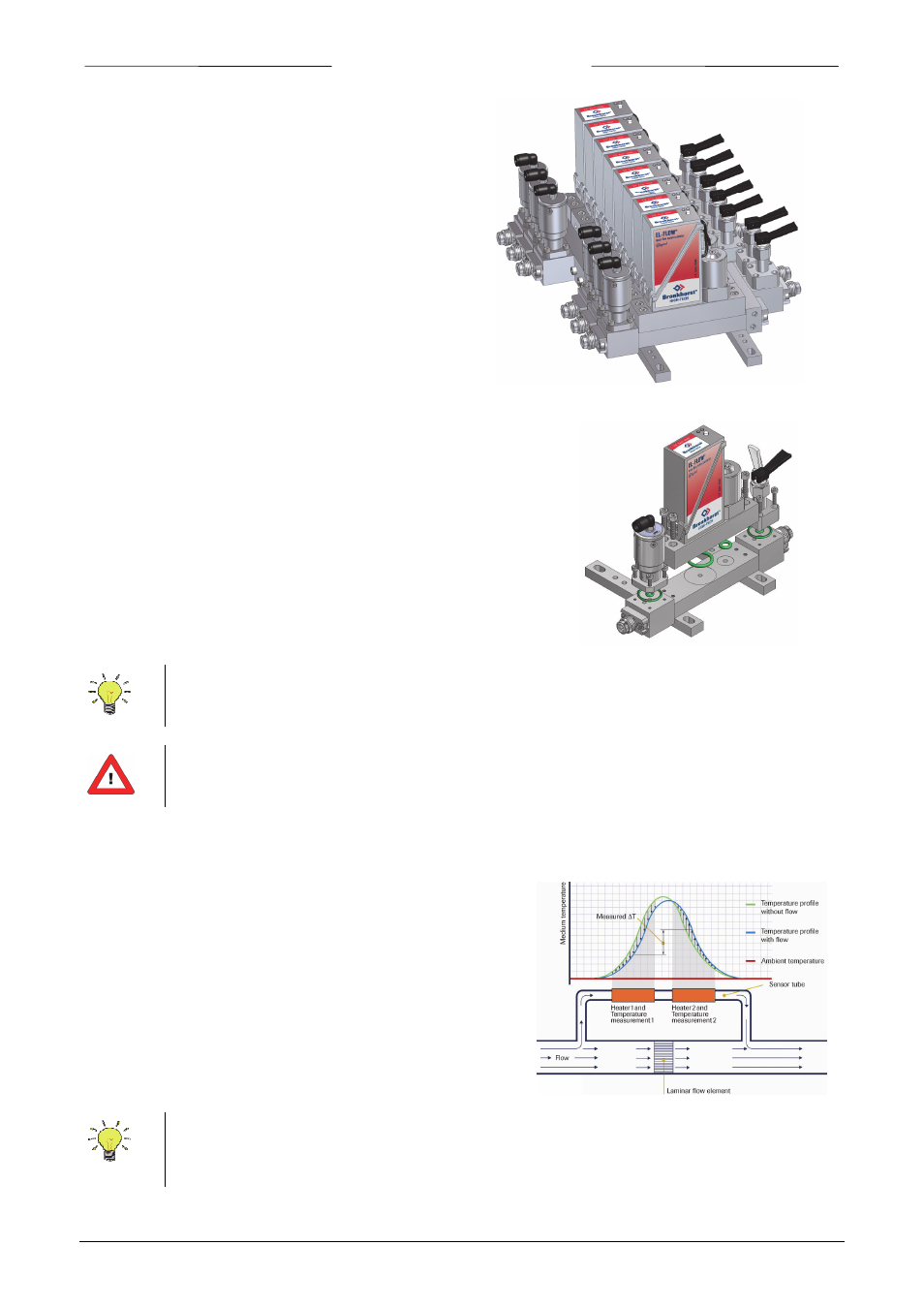
BRONKHORST HIGH-TECH B.V.
9.17.057
page 10
2.13 Description
2.13.1 Introduction
FLOW‐SMS systems are compact mounting rail assemblies,
containing one or more mass flow or pressure sensor
modules, that can be combined with control valves,
shut‐off valves, mixing chambers, filters or any other
functional module as per customer's request.
Also the manifold on which the functional modules are
mounted consists of a modular assembly of support rails,
base bodies and adapter or blind plates.
2.13.2 Functional modules
The pictures on the right side illustrate the modular concept
of the FLOW‐SMS system. It offers great flexibility for the end‐user
with respect to modifications and serviceability. The functional
modules are ‘top‐mount’, so they can easily be exchanged without
removing the total assembly.
In the following paragraphs we have laid down the instructions
for removal and replacement of functional modules.
Bronkhorst High‐Tech recommends to clean or to replace gaskets and hexagon bolts before
reassembling functional modules.
FLOW‐SMS manifold components (base bodies, distribution and mixing chamber, etc.) should only be
removed or replaced by qualified personnel.
2.13.3 Flow modules
-
General information
The gas flow sensor operates on a principle of heat transfer by
sensing the temperature difference along a heated section of
a capillary tube. Part of the total flow is forced through the
capillary by means of a laminar flow element in the main stream
generating a pressure difference. The design of the laminar flow
device is such that flow conditions in both the capillary and
laminar flow device are comparable, thereby resulting in
proportional flow rates through the meter. The ΔT sensed by the
upstream and downstream temperature sensors on the capillary
depends on the amount of heat absorbed by the gas flow.
Each instrument has been calibrated and adjusted for customer process conditions. The performance
and accuracy may be affected tremendously if physical fluid properties such as heat capacity and
viscosity change due to changing process conditions. For operation on other gases see paragraph 4.1.