Function description, Device properties, 1 integrated protection mechanisms – Pilz PNOZ ma1p 2 Analog Input User Manual
Page 15: 4function description, 1 device properties
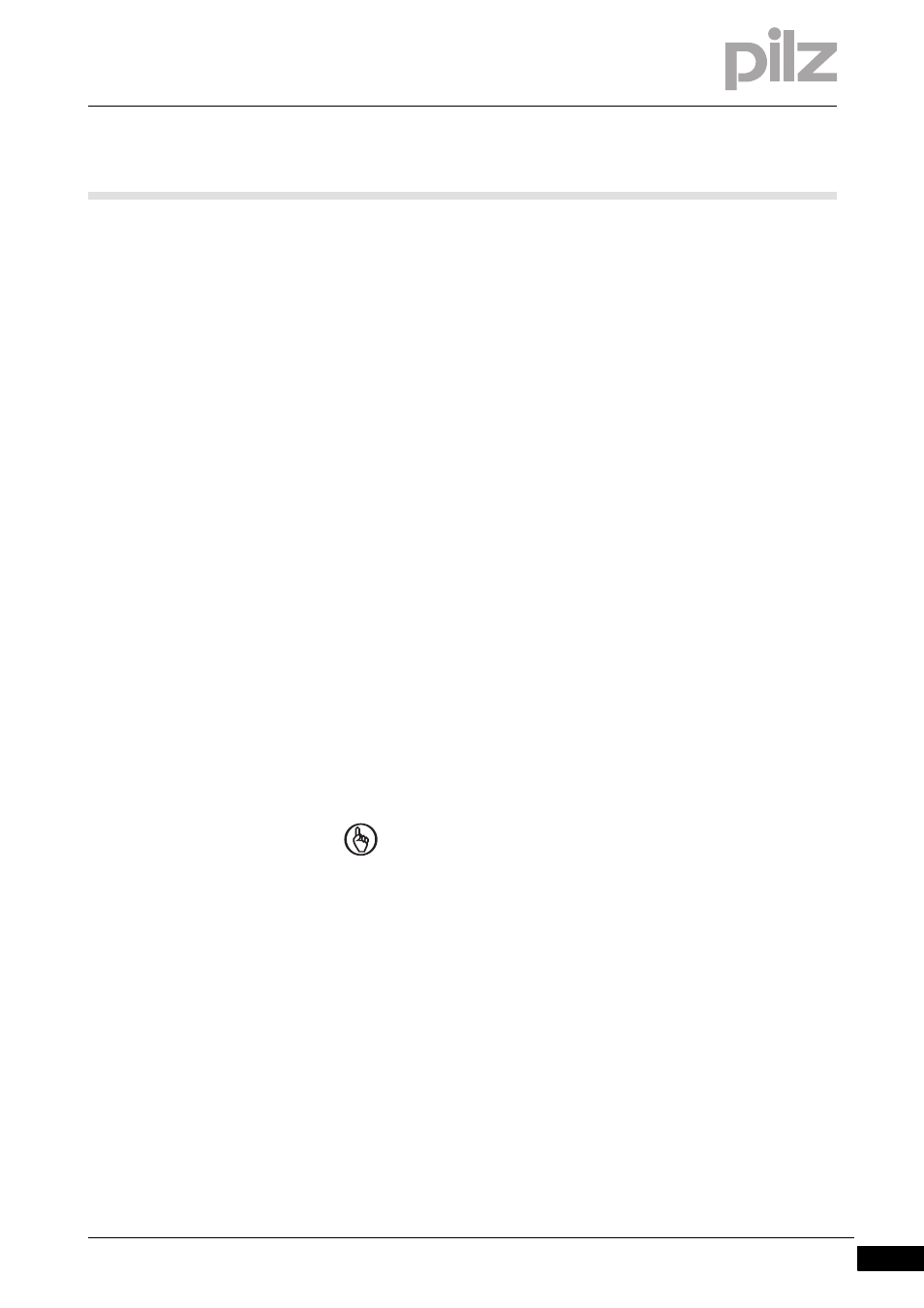
Pilz GmbH & Co. KG, Felix-Wankel-Straße 2, 73760 Ostfildern, Germany
Telephone: +49 711 3409-0, Telefax: +49 711 3409-133, E-Mail: [email protected]
4-1
4.1
Device properties
4
Function Description
4
4000
Function Description
Function Description
4-
4.1
Device properties
4100
Device properties
4-
4.1.1
Integrated protection mechanisms
Integrated protection mechanisms
4-
Sicherheitseigenschaften_multi_allgemein
The relay conforms to the following safety criteria:
`
The circuit is redundant with built-in self-monitoring.
`
The safety function remains effective in the case of a component fail-
ure.
Schutzmechanismen_Analogeingangsmodul_SIL
The analogue input module can be used for applications up to SIL3.
For applications in accordance with SIL2 or SIL3, input devices must be
attached that are certified for SIL2 in accordance with IEC 61508. The
output signal of the input device must be monitored, i.e. actual and set
value must be compared with one another. In the event of a deviation, a
reaction must occur that the PNOZmulti recognises and to which it re-
acts.
`
SIL2 applications:
SIL2 applications are only possible for current measurement. If the
analogue input module is to be used for current measurement on SIL2
applications, both inputs can be used independently for current
measurement.
`
SIL3 applications:
If the analogue input module is to be used for SIL3 applications, both
inputs must be configured. They will then be combined to form a SIL3
input. To do this, connect a suitable encoder to each input. The ana-
logue input module will then check the feasibility of the input signals,
i.e. the values measured from both input signals are compared.
Schutzmechanismen_Analogeingangsmodul_Zuatz_Wichtig_BA
NOTICE
For SIL3 applications, set a maximum permitted deviation
between the measured values of both input signals (tolerance) in
the PNOZmulti Configurator. A tolerance is only entered to bal-
ance out the imprecision of the signal recording, the encoder
and the analogue input module. To maintain safety, the toler-
ance should be set as low as possible. Please note that the
maximum safety-related measurement error for the overall
system is composed of the following measurement errors:
Error during signal recording
+ Sensor measurement error
+ Max. measurement error in the event of a potential module
error
To ensure that your application switches off safely in the event of
a critical process variable, the configuration of the range limits/
threshold values must be increased/decreased to take into
account the maximum measurement error.