Flow regulation, Flushing, Warning – Carrier AQUAZONE PCV015-060 User Manual
Page 32
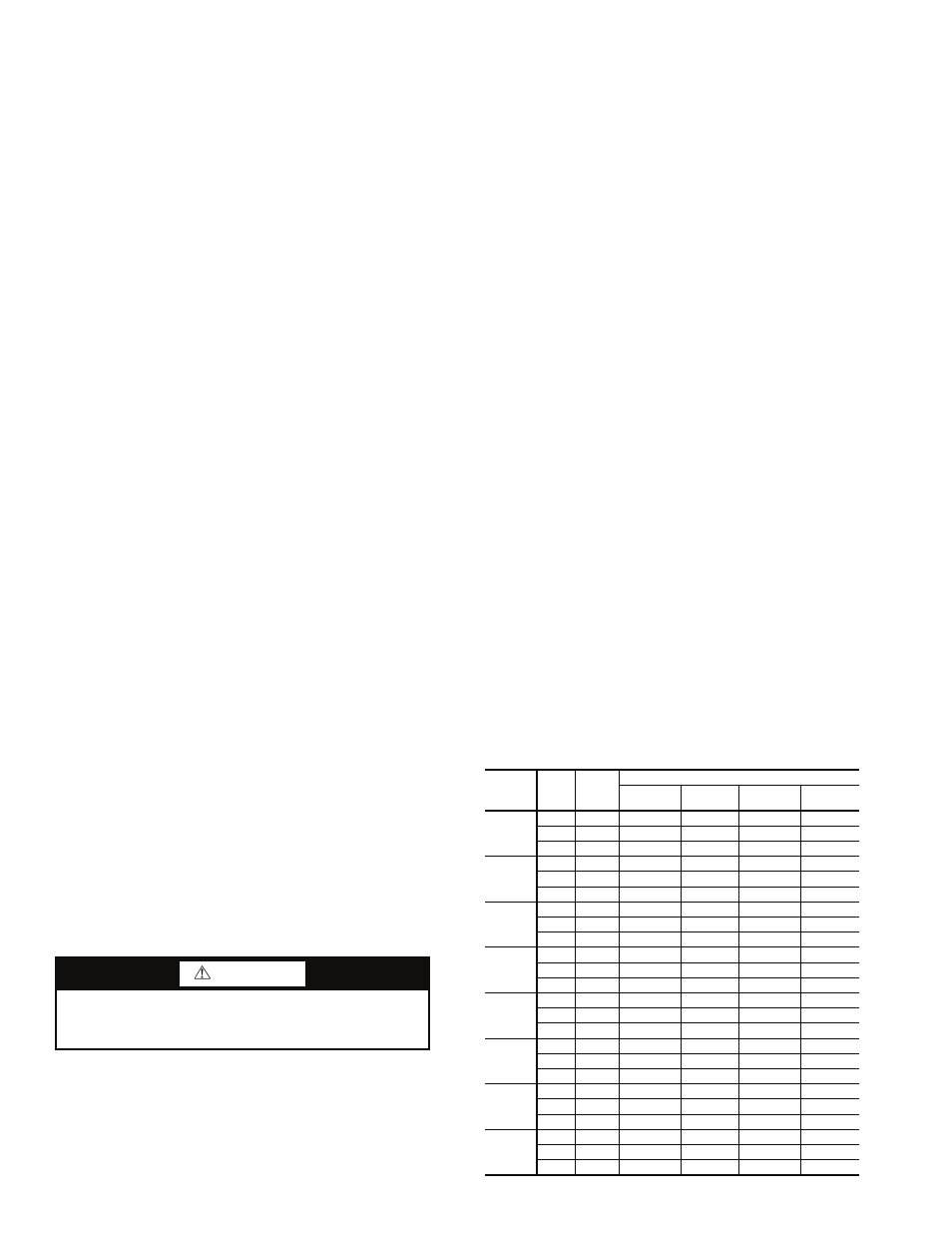
32
• The condenser water limit needs to be verified
depending on design parameters and application,
whether geothermal or boiler/tower.
7. To view unit configuration settings:
a. Select the Unit Configuration softkey, then select
Unit.
b. Scroll through the unit settings by using the up and
down arrow keys. Unit settings include:
• Fan Mode: Default Continuous
• Fan Delay:
• Minimum SAT Cooling: Default 50 F
• Maximum SAT Heating: Default 110 F
• Filter Service Alarm: Must be set from 0 to 9999 hr
8. To set local schedules:
a. Select the Schedule softkey from the Configuration
screen, then press enter.
b. Select Weekly, then press enter (7 schedules
available).
c. Select day and press enter.
d. Press enter again and select ADD or DEL (DECR
or INCR) set schedule.
e. Enter ON/OFF time, then press continue.
f. Press OK to apply and save to a particular day of
the week.
g. Continue to add the same or different schedule spe-
cific days of the week.
To add exceptions to the schedule:
i. Press Add softkey.
ii. Select exception type from following:
• Date
• Date Range
• Week-N-Day
• Calender Reference
9. Go back to Home Screen.
10. Remove BACview
6
cable from SPT sensor by reversing
the process in Step 1.
11. Perform system test.
Flow Regulation —
Flow regulation can be accom-
plished by two methods. Most water control valves have a flow
adjustment built into the valve. By measuring the pressure drop
through the unit heat exchanger, the flow rate can be deter-
mined. See Table 23. Adjust the water control valve until the
flow of 1.5 to 2 gpm is achieved. Since the pressure constantly
varies, two pressure gages may be needed in some
applications.
An alternative method is to install a flow control device.
These devices are typically an orifice of plastic material de-
signed to allow a specified flow rate that are mounted on the
outlet of the water control valve. Occasionally these valves
produce a velocity noise that can be reduced by applying some
back pressure. To accomplish this, slightly close the leaving
isolation valve of the well water setup.
Flushing —
Once the piping is complete, units require final
purging and loop charging. A flush cart pump of at least 1.5 hp
is needed to achieve adequate flow velocity in the loop to purge
air and dirt particles from the loop. Flush the loop in both
directions with a high volume of water at a high velocity. Fol-
low the steps below to properly flush the loop:
1. Verify power is off.
2. Fill loop with water from hose through flush cart before
using flush cart pump to ensure an even fill. Do not allow
the water level in the flush cart tank to drop below the
pump inlet line to prevent air from filling the line.
3. Maintain a fluid level in the tank above the return tee to
avoid air entering back into the fluid.
4. Shutting off the return valve that connects into the flush
cart reservoir will allow 50 psig surges to help purge air
pockets. This maintains the pump at 50 psig.
5. To purge, keep the pump at 50 psig until maximum
pumping pressure is reached.
6. Open the return valve to send a pressure surge through
the loop to purge any air pockets in the piping system.
7. A noticeable drop in fluid level will be seen in the flush
cart tank. This is the only indication of air in the loop.
NOTE: If air is purged from the system while using a 10 in.
PVC flush tank, the level drop will only be 1 to 2 in. since
liquids are incompressible. If the level drops more than this,
flushing should continue since air is still being compressed in
the loop. If level is less than 1 to 2 in., reverse the flow.
8. Repeat this procedure until all air is purged.
9. Restore power.
Antifreeze may be added before, during or after the flushing
process. However, depending on when it is added in the
process, it can be wasted. Refer to the Antifreeze section for
more detail.
Loop static pressure will fluctuate with the seasons. Pres-
sures will be higher in the winter months than during the
warmer months. This fluctuation is normal and should be con-
sidered when charging the system initially. Run the unit in
either heating or cooling for several minutes to condition the
loop to a homogenous temperature.
When complete, perform a final flush and pressurize the
loop to a static pressure of 40 to 50 psig for winter months or
15 to 20 psig for summer months.
After pressurization, be sure to remove the plug from the
end of the loop pump motor(s) to allow trapped air to be
discharged and to ensure the motor housing has been flooded.
Be sure the loop flow center provides adequate flow through
the unit by checking pressure drop across the heat exchanger.
Compare the results to the data in Table 23.
Table 23 — Coaxial Water Pressure Drop
WARNING
To avoid possible injury or death due to electrical shock,
open the power supply disconnect switch and secure it in
an open position before flushing system.
50PC
UNIT
SIZE
gpm
L/s
PRESSURE DROP, psi (kPa)
30 F
(-1 C)
50 F
(10 C)
70 F
(21 C)
90 F
(32 C)
015
1.9
0.12
1.0 (6.9)
0.6 (4.4)
0.5 (3.4)
0.4 (2.8)
2.8
0.18
1.8 (12.4)
1.4 (9.3)
1.1 (7.6)
1.0 (6.9)
3.8
0.24
3.3 (22.7)
2.5 (17.5)
2.1 (14.7)
1.9 (13.1)
018
2.3
0.14
2.1 (14.5)
1.4 (9.9)
1.1 (7.6)
0.9 (6.2)
3.4
0.21
3.4 (23.4)
2.6 (17.6)
2.1 (14.7)
1.8 (12.4)
4.5
0.28
5.9 (40.6)
4.6 (31.5)
3.9 (26.9)
3.4 (23.4)
024
3.0
0.19
2.2 (15.2)
1.7 (11.6)
1.4 (9.6)
1.2 (8.3)
4.5
0.28
4.0 (27.6)
3.2 (22.2)
2.8 (19.3)
2.5 (17.2)
6.0
0.38
7.2 (49.6)
5.9 (40.6)
5.2 (35.8)
4.7 (32.4)
030
3.8
0.24
1.3 (9.0)
0.9 (6.1)
0.7 (4.8)
0.6 (4.1)
5.6
0.35
2.3 (15.8)
1.8 (12.5)
1.5 (10.3)
1.4 (9.6)
7.5
0.47
4.2 (28.9)
3.4 (23.2)
2.9 (20.0)
2.6 (17.9)
036
4.5
0.28
1.8 (12.4)
1.4 (9.6)
1.2 (8.3)
1.0 (6.9)
6.8
0.43
3.1 (21.4)
2.4 (16.8)
2.1 (14.7)
1.9 (13.1)
9.0
0.57
5.4 (37.2)
4.4 (30.0)
3.8 (26.2)
3.4 (23.4)
042
5.3
0.33
2.3 (15.8)
1.8 (12.1)
1.5 (10.3)
1.3 (9.0)
7.9
0.50
4.3 (29.6)
3.5 (24.2)
3.1 (26.4)
2.8 (19.3)
10.5
0.66
7.9 (54.4)
6.5 (44.8)
5.7 (39.3)
5.2 (35.8)
048
6.0
0.38
1.8 (12.4)
1.5 (10.1)
1.3 (9.0)
1.2 (8.3)
9.0
0.57
3.4 (23.4)
3.0 (20.4)
2.7 (18.6)
2.6 (17.9)
12.0
0.76
6.2 (42.7)
5.5 (37.9)
5.1 (35.1)
4.8 (35.1)
060
7.5
0.47
3.4 (23.4)
2.8 (19.2)
2.4 (16.5)
2.2 (15.2)
11.3
0.71
6.8 (46.9)
5.9 (40.8)
5.4 (37.2)
5.0 (34.5)
15.0
0.95
12.6 (86.8) 11.1 (76.8) 10.3 (71.0)
9.6 (66.1)