Fine tuning the flow sensor calibration number, Fine tuning the flow sensor calibration number -5 – TeeJet ARC-6000 User Manual
Page 15
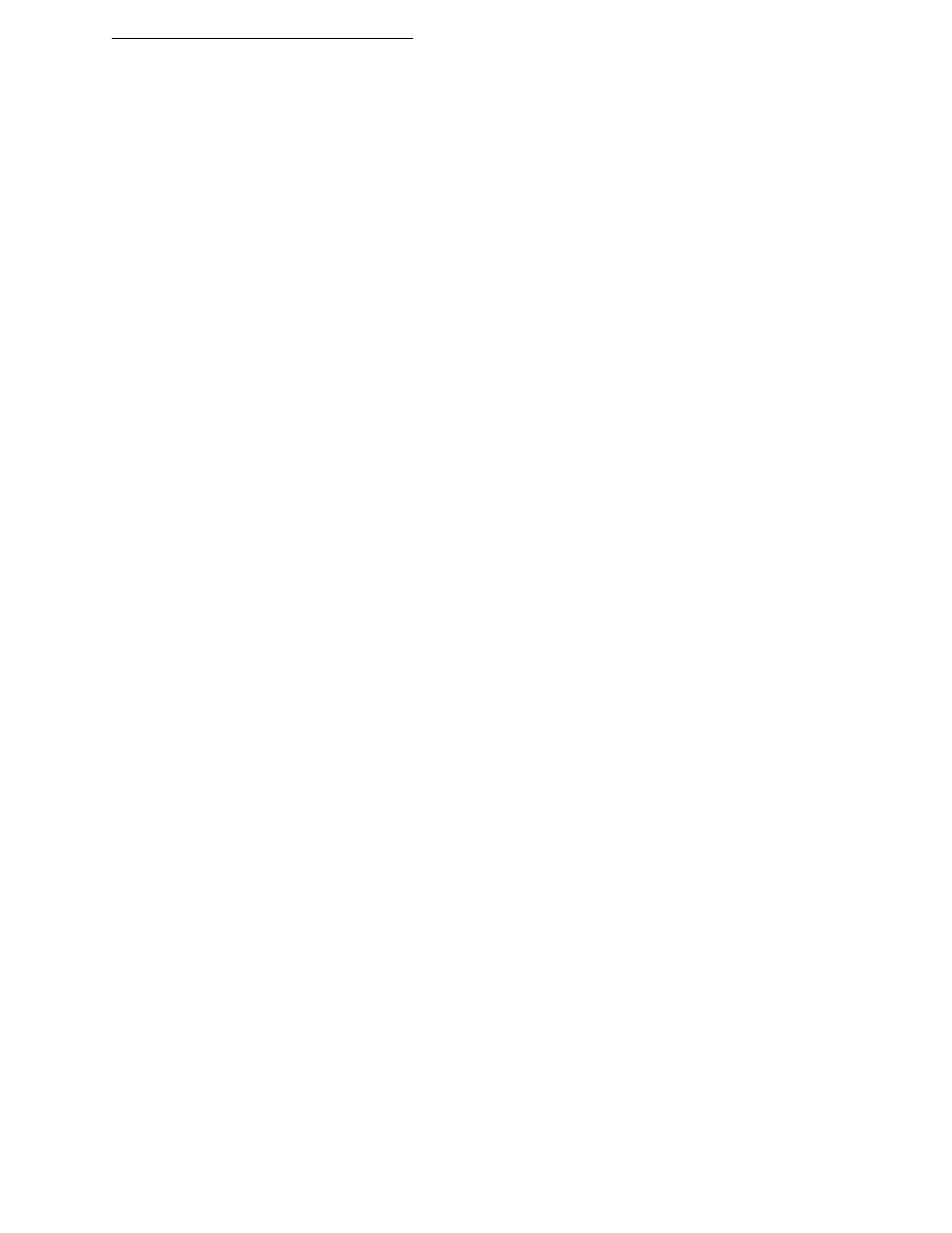
2-5
98-0501
Rev.- 1
ARC 6000
CE & S
TANDARD
V
ERSION
B. Hold INC/DEC switch to DEC until console reads PSi 0
Note: A display reading of "PSi - -" indicates that the pressure sensor is not connected. A reading of "PSi - 0" indi-
cates a reading of less than 0 PSI. This suggests that the sensor may need to be recalibrated to 0 pressure.
SETTING THE HIGH SIDE:
A. Set the console to the following positions;
Power Switch
ON
Setup/Operate Switch
OPERATE
Display Selector Switch
PRIME
Master Switch
ON
Supply Pump
ON
Ground speed
0 (zero)
B. Hold the INC/DEC switch to INC for about 3 seconds. The display will read "OPEN". Release the INC switch. Push
the INC switch again and hold it for about 3 seconds. The display will read "PSi xxx". The xxx is a pressure. The INC/
DEC switch can now be used to adjust the pressure reading on the console to match the reading on the pressure gauge. If
no switch changes are detected after 3 seconds, the console will read "OPEN" again. Actuating the DEC switch when the
console reads "OPEN" will cause the console to read "CLOSE" and the valve will close.
2.6.1.4. FINE TUNING THE FLOW SENSOR CALIBRATION NUMBER
NOTE: We recommend that these tests be done using water, and only after neutralizing the tank and system.
Once the initial calibration number has been determined and entered into the console, a calibration run should be made to adjust
the number for maximum accuracy. The hardest part of the calibration procedure will be accurately measuring the actual discharge
of large volumes of liquid. The more accurately the discharge is measured, the more accurate the calibration will be. Since each
operator's facilities are different, it is not possible to prescribe a standard method of measuring discharge. Operators have
successfully performed the task using a second, calibrated flow meter, using a truck scale and calculating volumes based on weight
and density of the liquid discharged, and by discharging into a marked, calibrated tank.
It is necessary to pump and measure at least 100 gallons, and as much as 300 gallons, depending on the accuracy required. For
example: if the actual measurement is accurate to within 3 gallons, using 300 gallons will yield an accuracy of 1 %.
If only 100 gallons are pumped and measured, the calibration can be off as much as 3%. The better the measurement accuracy
of actual discharge and the more material pumped, the more accurate will be the resulting calibration.
A method similar to the following is recommended.
1. If using Psi mode, enter the appropriate Correction Factor for the material that you will be using for the test (Not
applicable for rEFLO or STnrd applications) (see section 2.4.1).
2. Turn the Mode Switch to "OPERATE", the Display Selector to "APPLICATION RATE". Enter the desired
application rate.
3. Verify that the boom switches are "OFF", select the "SETUP" mode; rotate the display selector switch to
"TOTAL APPLIED".
4. For Psi mode applications, the current pressure sensor calibration number will be displayed. Verify that it is the
recommended initial calibration number for the nozzles installed in the system. For rEFLO or STnrd applications,
the flowmeter calibration number will be displayed (rEFLO mode requires all booms be on to view cal. #.) Use the
INC/DEC switch to adjust as necessary.
5. Select "OPERATE" with the mode selector switch. Hold the DEC switch down for three to five seconds to zero
the accumulated gallons.
6. Make sure there is enough liquid in the main tank to do the test. Weigh the sprayer and load of water. Position
the sprayer in an appropriate area to do the calibration test.