Unit start-up heating mode, Flow regulation, Flushing – Carrier AQUAZONE RVC User Manual
Page 34
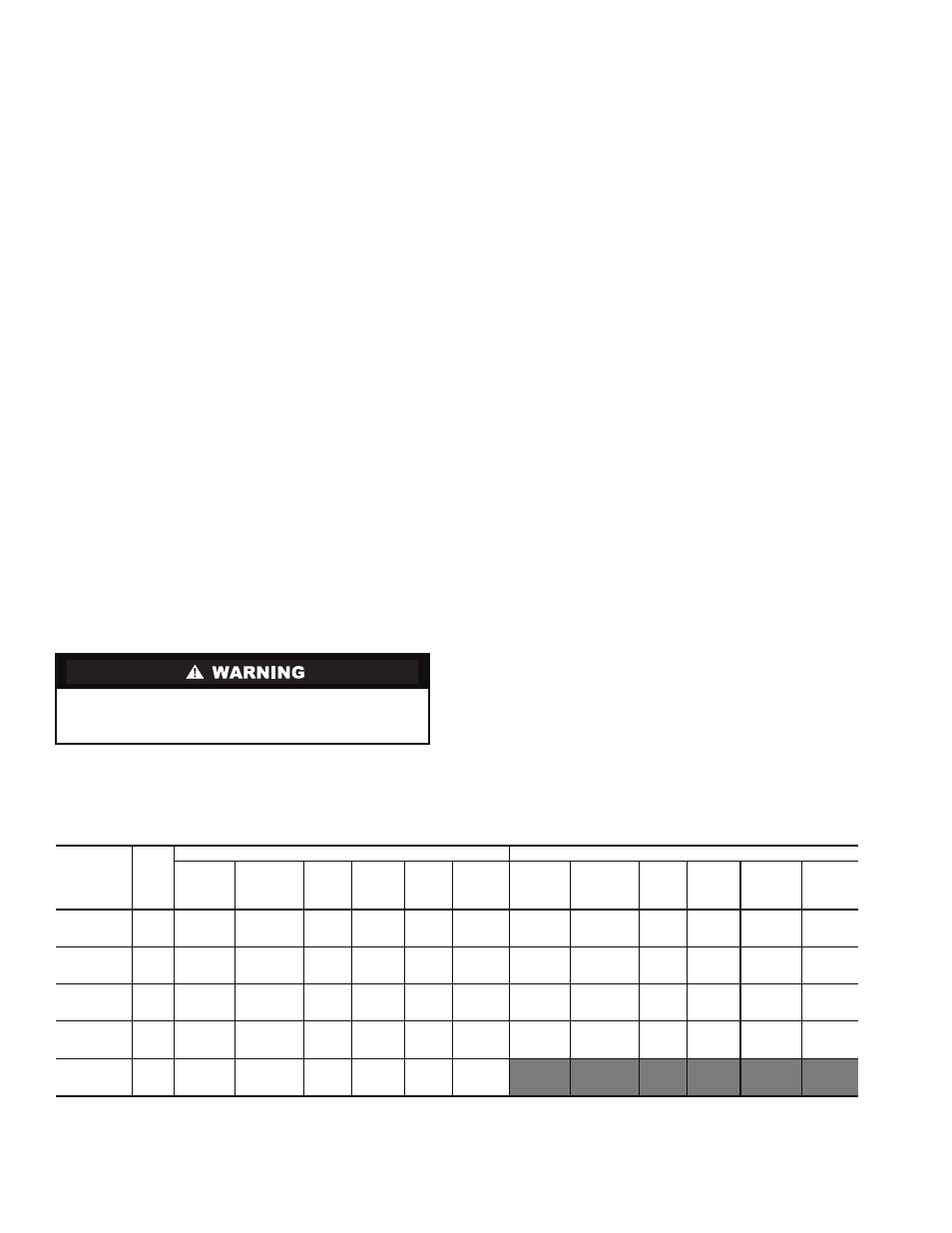
34
Unit Start-Up Heating Mode
NOTE: Operate the unit in heating cycle after checking the
cooling cycle. Allow 5 minutes between tests for the pressure
or reversing valve to equalize.
1. Turn thermostat to lowest setting and set thermostat
switch to HEAT position.
2. Slowly turn the thermostat to a higher temperature until
the compressor activates.
3. Check for warm air delivery at the unit grille within a few
minutes after the unit has begun to operate.
4. Check the temperature of both supply and discharge wa-
ter. Compare to Table 21. If temperature is within range,
proceed. If temperature is outside the range, check the
heating refrigerant pressures in Table 21.
5. Once the unit has begun to run, check for warm air deliv-
ery at the unit grille.
6. Check air temperature rise across the coil when compres-
sor is operating. Air temperature rise should be between
20 and 30 F after 15 minutes at load.
7. Check for vibration, noise and water leaks.
Flow Regulation —
Flow regulation can be accom-
plished by two methods. Most water control valves have a flow
adjustment built into the valve. By measuring the pressure drop
through the unit heat exchanger, the flow rate can be deter-
mined. See Tables 22-24. Adjust the water control valve until
the flow of 1.5 to 2 gpm is achieved. Since the pressure con-
stantly varies, two pressure gages may be needed in some
applications.
An alternative method is to install a flow control device.
These devices are typically an orifice of plastic material de-
signed to allow a specified flow rate that are mounted on the
outlet of the water control valve. Occasionally these valves
produce a velocity noise that can be reduced by applying some
back pressure. To accomplish this, slightly close the leaving
isolation valve of the well water setup.
Flushing —
Once the piping is complete, units require final
purging and loop charging. A flush cart pump of at least 1.5 hp
is needed to achieve adequate flow velocity in the loop to purge
air and dirt particles from the loop. Flush the loop in both
directions with a high volume of water at a high velocity. Fol-
low the steps below to properly flush the loop:
1. Verify power is off.
2. Fill loop with water from hose through flush cart before
using flush cart pump to ensure an even fill. Do not allow
the water level in the flush cart tank to drop below the
pump inlet line to prevent air from filling the line.
3. Maintain a fluid level in the tank above the return tee to
avoid air entering back into the fluid.
4. Shutting off the return valve that connects into the flush
cart reservoir will allow 50 psi surges to help purge air
pockets. This maintains the pump at 50 psi.
5. To purge, keep the pump at 50 psi until maximum pump-
ing pressure is reached.
6. Open the return valve to send a pressure surge through
the loop to purge any air pockets in the piping system.
7. A noticeable drop in fluid level will be seen in the flush
cart tank. This is the only indication of air in the loop.
NOTE: If air is purged from the system while using a 10 in.
PVC flush tank, the level drop will only be 1 to 2 in. since
liquids are incompressible. If the level drops more than this,
flushing should continue since air is still being compressed in
the loop. If level is less than 1 to 2 in., reverse the flow.
8. Repeat this procedure until all air is purged.
9. Restore power.
Antifreeze may be added before, during or after the flushing
process. However, depending on when it is added in the
process, it can be wasted. Refer to the Antifreeze section for
more detail.
Loop static pressure will fluctuate with the seasons. Pres-
sures will be higher in the winter months than during the
warmer months. This fluctuation is normal and should be con-
sidered when charging the system initially. Run the unit in
either heating or cooling for several minutes to condition the
loop to a homogenous temperature.
When complete, perform a final flush and pressurize the
loop to a static pressure of 40 to 50 psi for winter months or 15
to 20 psi for summer months.
After pressurization, be sure to remove the plug from the
end of the loop pump motor(s) to allow trapped air to be
discharged and to ensure the motor housing has been flooded.
Be sure the loop flow center provides adequate flow through
the unit by checking pressure drop across the heat exchanger.
Compare the results to the data in Tables 22-24.
Table 21 — Typical Unit Operating Pressures and Temperatures
LEGEND
To avoid possible injury or death due to electrical shock,
open the power supply disconnect switch and secure it in
an open position before flushing system.
ENTERING
WATER
TEMP (F)
(EWT)
GPM/
TON
COOLING
HEATING
Suction
Pressure
(psig)
Discharge
Pressure
(psig)
Super-
heat
(F)
Sub-
cooling
(F)
Water
Temp
Rise
(F)
Air
Temp
Drop (F)
DB
Suction
Pressure
(psig)
Discharge
Pressure
(psig)
Super-
heat (F)
Sub-
cooling
(F)
Water
Temp
Drop (F)
DB
Air
Temp
Rise (F)
30
1.5
75-85
90-105
25-40
12-20
21-24
21-26
34- 39
167-186
12-16
1-4
7.6- 8.4
14-20
2.3
74-84
80- 95
25-40
11-18
13-16
21-26
37- 43
172-191
12-16
1-4
4.8- 5.6
16-22
3.0
73-83
70- 85
25-40
10-16
6-11
21-26
40- 46
177-196
12-16
1-4
3.4- 4.2
16-22
50
1.5
75-85
125-155
12-20
10-18
20-23
20-25
50- 60
180-210
10-17
1-5
10.8-11.9
23-29
2.3
74-84
120-142
12-20
9-16
12-15
20-25
53- 62
185-215
10-17
1-5
6.7- 8.1
24-30
3.0
73-83
115-138
12-20
8-14
8-12
20-25
55- 65
190-220
10-17
1-5
5.1- 5.9
25-31
70
1.5
75-85
179-198
9-16
8-15
19-22
19-24
71- 82
205-230
14-19
1-5
14.0-15.2
28-34
2.3
74-84
168-186
9-16
8-14
12-17
19-24
73- 85
210-238
14-19
1-5
9.0-10.2
30-37
3.0
73-83
158-175
9-16
8-12
7-12
19-24
76- 88
215-242
14-19
1-5
6.7- 7.9
31-38
90
1.5
75-85
229-251
9-17
8-15
18-21
17-23
85- 95
220-260
18-28
2-5
14.4-16.6
32-39
2.3
74-84
218-241
9-17
8-14
10-14
17-23
90-100
225-265
18-28
2-5
10.8-12.4
33-41
3.0
73-83
208-230
9-17
8-12
6-11
17-23
95-105
230-270
18-28
2-5
7.2- 8.3
35-42
110
1.5
77-87
280-320
8-15
10-25
17-20
15-20
2.3
76-86
270-310
8-15
10-24
9-13
15-20
3.0
75-85
260-300
8-15
10-22
5-10
15-20
DB
— Dry Bulb
EAT
— Entering Air Temperature
NOTES:
1. Based on nominal 400 cfm per ton airflow, 70 F EAT heating and 80/67 F
EAT cooling.
2. Cooling air and water numbers can vary greatly with changes in humidity.
3. Subcooling is based upon the head pressure at compressor service port.
4. Unit should not be operated in heating mode with an EWT of 110.