Hardy HI 1746-WS User Manual
Hardy Tools
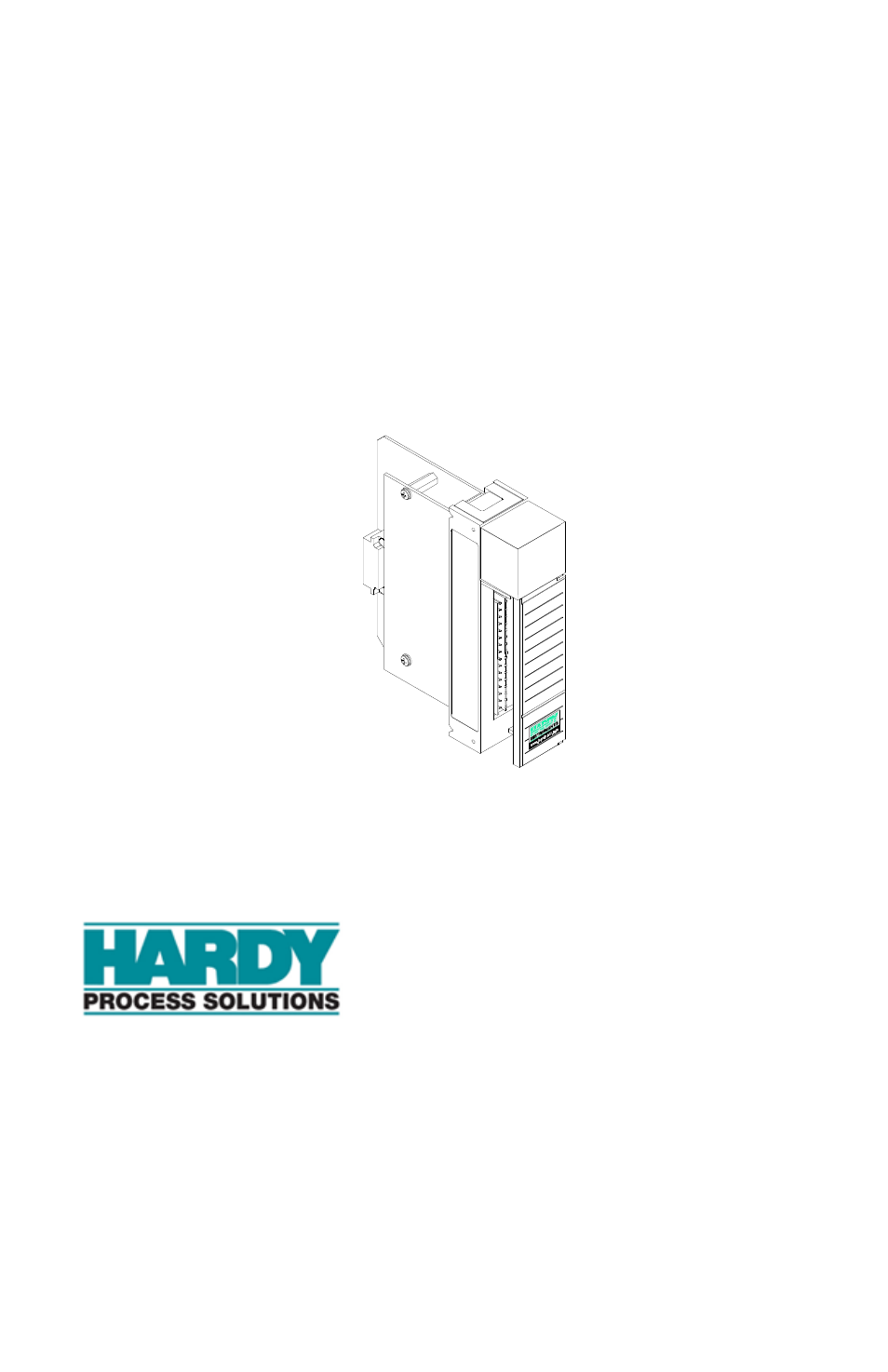
HI 1746-WS
WEIGH SCALE MODULE
OPERATION AND INSTALLATION
MANUAL
Series C
Corporate Headquarters
9440 Carroll Park Drive
San Diego, CA 92121
Phone: (858) 278-2900
FAX: (858) 278-6700
Web-Site: http://www.hardysolutions.com
Hardy Process Solutions Document Number: 0596-0234-01 Rev H
Copyright September 2011 Hardy Process Solutions, Inc. All Rights Reserved. Printed in the U.S.A. (941028)
Table of contents
Document Outline
- HI 1746-WS
- WEIGH SCALE MODULE
- Table of Contents
- Table of Illustrations
- Chapter 1 - Overview
- Chapter 2 - specifications
- A Brief Description of Chapter 2
- Specifications for a Standard HI 1746-WS Weigh Scale Module
- Modes of Operation
- Conversion Rate
- Averages
- Resolution
- Input
- Non-Linearity
- Maximum Zero Tolerance
- WAVERSAVER®
- Excitation Monitor
- Common-Mode Rejection
- Common-Mode Voltage Range
- Backplane Input Voltage
- Backplane Current Load
- Power
- C2 Calibration Input
- Cable lengths
- Load Cell Excitation
- C2 Calibration Output
- Set Point (1 & 2) Out
- Environmental Requirements
- Optional Equipment HI 215IT Junction Box
- Default Parameters
- Chapter 3 - installation
- A Brief Description of Chapter 3
- Unpacking
- Installing the HI 1746-WS into an Allen-Bradley SLC 500 Processor or Allen- Bradley Remote Rack
- Removing the Module from the SLC 500 or Remote Chassis
- Installing the Module I/ O Connector
- Load Cell Wiring Diagrams
- Installing the Hardy Configuration Software (Optional)
- chapter 4 - setup
- A Brief Description of Chapter 4
- Power Check
- Setting Up Communications Between the SLC and the HI 1746-WS Weigh Scale Module
- About M Files
- Direct M File Mapping
- M File Interface to Set Up for Local Mode of Operation
- Logical File Interface to Set Up for Remote Mode of Operation (8 Word)
- Executable Command List
- Zero Command (ZEROCMD)
- Tare Command (TARECMD)
- Write Non-Volatile Command (WRITENONVOLA TILE)
- Reload Non- Volatile (RELOADNONVOL ATILE)
- Float Integer to Integer Conversion Command (FLOAT2INT)
- Integer to Float Integer Conversion Command (INT2FLOAT)
- Cal Low Command (CALLOWCMD)
- Cal High Command (CALHIGHCMD)
- C2 Cal Command (C2CALCMD)
- Read C2 Serial Number Command (READC2SERIALN UM)
- Set Parameters Command (SETPARAM)
- Get Parameters Command (GETPARAM)
- I/O Setup Ladder Logic for Remote Mode Operation
- HI WS100 Configuration Software Interface (Remote Mode of Operation)
- Setting The Process Weighing Parameters
- About the Ladder Logic Example
- Weight Multiplier
- SETPARAM - GETPARAM Command and Non Volatile Memory
- Setting Parameters Ladder Logic Explanation
- Rung #0 Does an initial read of the M1 file. This is necessary to get the sequence number for future writes.
- Rung #1 Loads data into the write location ready to write. The data required is:
- Rung #2 Checks to see if the data was loaded from the previous rung, then writes to the M0 file.
- Rung #3 Reads the M1 file for the response.
- Rung #4 Checks the results of the read to make sure that the sequence number was incremented (write complete) and that the status is zero (no error). If the check is good, it latches a bit for the next parameter.
- Rung #5 Checks the results of the read and if the status is not zero (error occurred) restarts the process of writing this parameter.
- Rungs #6-30 Duplicate the same process as rungs #1 to #5 for the remaining parameters.
- SETPARAMS Local Mode of Operation
- SETPARAMS Remote Mode of Operation
- Error Code List
- Calibration Setup Procedures
- chapter 5 - calibration
- A Brief Description of Chapter 5
- Pre-Calibration Procedures
- b. On some single and double ended shear beam load cells there is an arrow that indicates the direction of the applied load. If the arrow is pointing in the wrong direction, change the position of the load cell so that it is mounted in the direction ...
- b. Check to see that nothing is binding the load cell. This means that nothing is draped across the scale/vessel or the load cell, such as a hose, electrical cord, tubes, or other objects.
- c. Check to see that nothing is coming in contact with the scale/vessel other than service wires and piping that have been properly mounted with flexible connectors.
- Electrical Check Procedures
- Load Cell/Point Input/Output Measurements
- b. The expected output from each load cell/point depends on the mV/V rating of the load cell/point and the weight.
- c. For example, a 2mV/V load cell/point will respond with a maximum of 10 mVDC at full weight capacity of the system which includes the weight of the vessel and the weight of the product as measured by the load cell/point.
- d. If the load cell/point weight capacity is rated at 1000 pounds, the load cell/point will be 10 mVDC at 1000 pounds, 7.5 mVDC at 750 pounds, 5 mVDC at 500 pounds and so on.
- e. A zero reference point will vary from system to system depending on the “Dead Load” of the vessel. “Dead Load” is the weight of the vessel and appurtenances only, with no product loaded. In our example we will assume the dead load to be 50...
- f. Based on the example, the operating range for this scale is 5-10 mVDC with a 500 pound weight range. Understand that after zeroing the instrument, the 0 reading refers to the zero reference point and not absolute 0 mVDC or absolute 0 weight.
- Load Cell/Point Input/Output Measurements
- Load Check
- C2 Calibration
- Data Locations Used for Ladder Logic Examples (For Local Mode of Operation Only)
- N9:0 - 24
- N9:50
- N9:51
- N10:0 - 2
- N10:40 - 46
- N10:60 - 72
- C2 Calibration Ladder Logic Explanation
- Rung #0 Does an initial read of the M1 file. this is necessary to get the sequence number for future writes.
- Rungs #1-5 Downloads a reference point value. These rungs follow the same pattern as the SETPARAMS example in Chapter 4.
- Rungs #6-12 Writes the C2CALCMD to set the reference point. These rungs follow the same pattern as setting a parameter in the SETPARAMS example in Chapter 4.
- Rungs #13-17 Writes the WRITENONVOLATILE command. This will save the new calibration to the non-volatile memory. These rungs follow the same pattern as setting a parameter in the SETPARMS example in Chapter 4.
- C2 Calibration Ladder Logic Example (For Local Mode of Operation Only)
- C2 Calibration Ladder Logic Example (For Remote Mode of Operation Only)
- Hard Calibration
- chapter 6 - operating procedures
- Index