Tweco 550i Transmig User Manual
Page 37
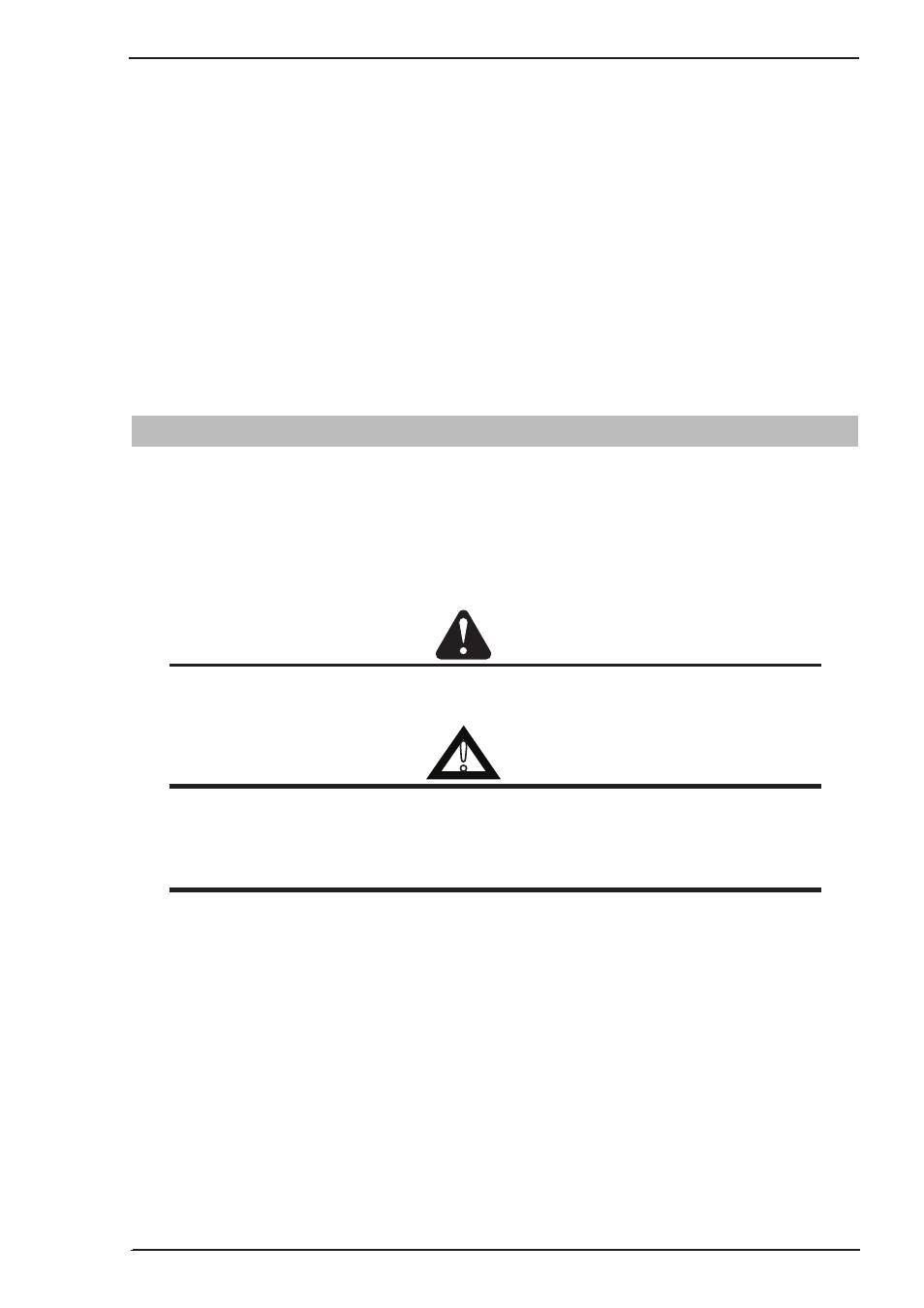
TRANSMIG 350i, 450i, 550i
Manual 0-5205 3-17
INSTALLATION, OPERATION AND SETUP
2. To reduce flow rate, allow the welding grade shielding gas to discharge from regulator by opening the
downstream valve. Bleed welding grade shielding gas into a well ventilated area and away from any
ignition source. Turn adjusting screw counterclockwise, until the required flow rate is indicated on the
gauge. Close downstream valve.
Shutdown
Close cylinder valve whenever the regulator is not in use. To shut down for extended periods (more than 30
minutes).
1. Close cylinder or upstream valve tightly.
2. Open downstream equipment valves to drain the lines. Bleed gas into a well ventilated area and away
from any ignition source.
3. After gas is drained completely, disengage adjusting screw and close downstream equipment valves.
4. Before transporting cylinders that are not secured on a cart designed for such purposes, remove
regulators.
3.08 Setup for MIG (GMAW) Welding with Gas Shielded Mig Wire
POWER SOURCE CONNECTIONS
A. Remove all packaging materials. Do not block the air vents at the front or rear of the Power Source.
B. Connect the work lead to the negative welding terminal (-) [positive welding terminal(+) for flux cored
electrode wire]. If in doubt, consult the electrode wire manufacturer. Welding current flows from the Power
Source via heavy duty bayonet type terminals. It is essential, however, that the male plug is inserted and
turned securely to achieve a sound electrical connection.
CAUTION
Loose welding terminal connections can cause overheating and result in the male plug being fused
in the terminal.
!
WARNING
Before connecting the work clamp to the work piece make sure the mains power supply is switched
off.
Secure the welding grade shielding gas cylinder in an upright position by chaining it to a suitable
stationary support to prevent falling or tipping.
C. Position a gas cylinder on the rear tray of the Power Source and lock securely to the Power Source cylinder
bracket with the chain provided. If this arrangement is not used or the Power Source is not fitted with a
gas cylinder tray then ensure that the gas cylinder is secured to a building pillar, wall bracket or otherwise
securely fixed in an upright position.
D. Select MIG mode with the process selection control button.
WIREFEEDER CONNECTIONS
A. Connect the welding power cable from the Wirefeeder's interconnection cables to the positive welding
terminal (+) [negative welding terminal (-) for flux cored electrode wire]. If in doubt, consult the electrode
wire manufacturer. Welding current flows from the Power Source via heavy duty bayonet type terminals.
It is essential, however, that the male plug is inserted and turned securely to achieve a sound electrical
connection.
B. Connect the control cable from the Wirefeeder to the 10 PIN or 19 PIN socket on the Power Source as
applicable.