Installation – tekmar 371 House Control User Manual
Page 10
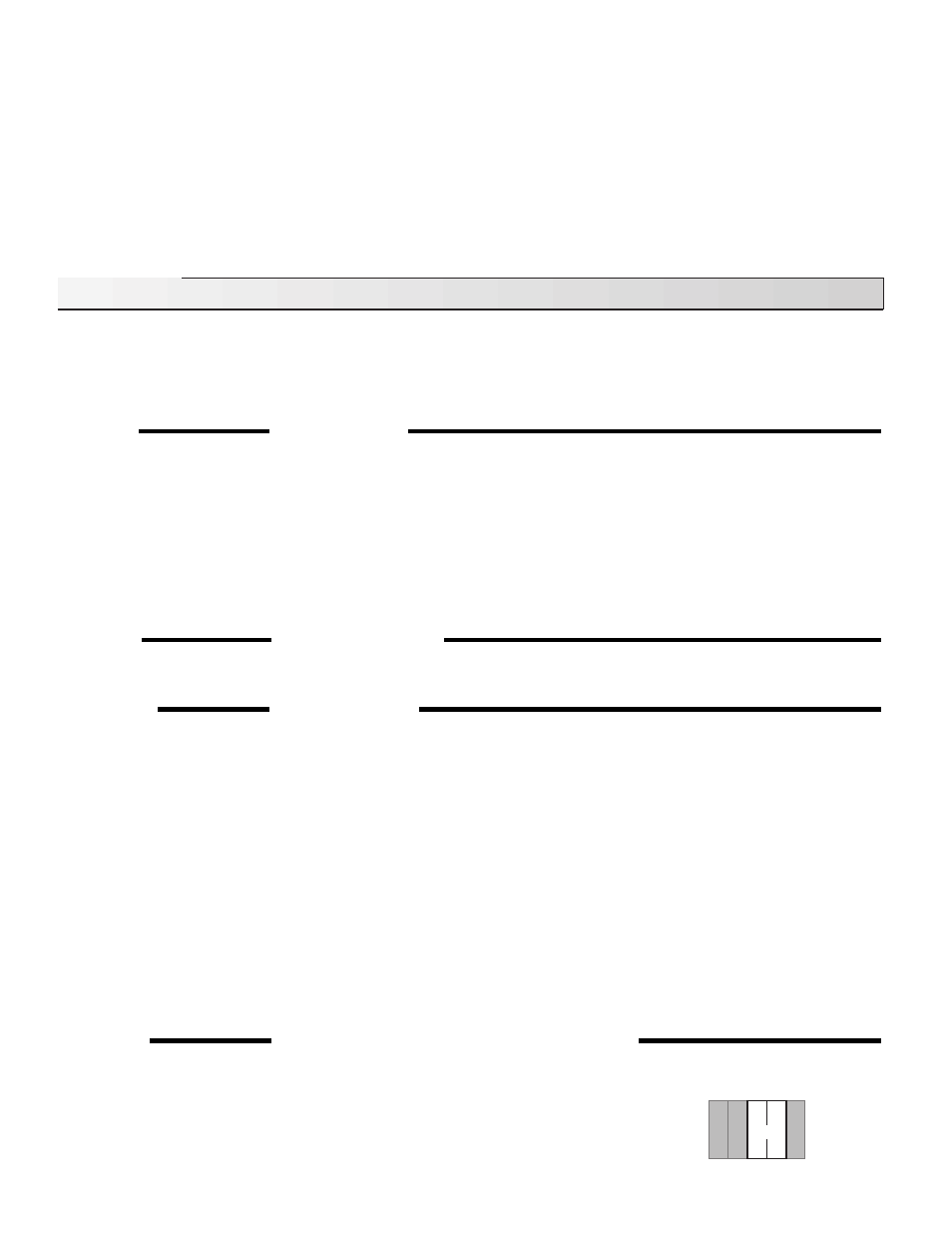
10
Exercising Procedure
The 371 first exercises the zone valves or pumps. If a zone valve or zone pump has not been operated in the past 3 days, the 371
turns on the zone relay for 10 seconds.
Note The zone relay exercising time is increased to 3 minutes if the DIP switch is set to
Thermal Motor.
After the zone valves or pumps have been exercised, the 371 exercises the mixing system pump (P2) and the boiler system pump
(P1). If the system pumps have not operated in the past 3 days, the 371 turns on the
Sys P1 and the Sys P2 relays for 10 seconds.
After the system pumps have been exercised, then, if any of the DIP switches are set to
Mixing and a variable speed injection pump
is used, the 371 turns on the variable speed injection pump every 3 days at full speed for 10 seconds. If a mixing valve is used,
the control fully opens and closes the valve.
Once the exercising procedure is complete, the 371 returns to its normal operating sequence.
Installation
Caution
Improper installation and operation of this control could result in damage to the equipment and possibly even personal injury.
It is your responsibility to ensure that this control is safely installed according to all applicable codes and standards. This
electronic control is not intended for use as a primary limit control. Other controls that are intended and certified as safety
limits must be placed into the control circuit.
STEP ONE
GETTING READY
Check the contents of this package. If any of the contents listed are missing or damaged, please contact your wholesaler or tekmar sales
representative for assistance.
Type 371 includes:
• One House Control 371
• One Outdoor Sensor 070
• Two Universal Sensors 071
• Data Brochures D 371, D 070, D 001
• Application Brochures A 371
• Essay E 021
Other information available:
• A 000, I 030, D 054, D 074
Note Carefully read the details of the Sequence of Operation sections in all applicable brochures to ensure that you have chosen the
proper control for your application.
STEP TWO
MOUNTING THE BASE
Remove the control from its base by pressing down on the release clip in the wiring chamber and sliding the control upwards. The base
is then mounted in accordance with the instructions in the Data Brochure D 001.
STEP THREE
ROUGH-IN WIRING
All electrical wiring terminates in the control base wiring chamber. The base has standard 7/8" (22 mm) knockouts which accept common
wiring hardware and conduit fittings. Before removing the knockouts, check the wiring diagram and plan the routing of wires. The control
base can be installed on a 4-3/4” x 4-3/4” electrical box to simplify line voltage wiring.
Power must not be applied to any of the wires during the rough-in wiring stage.
• Install the Outdoor Sensor 070, Boiler Sensor 071, and the Supply Sensor 071 according to the instructions in the Data Brochure
D 070 and run the wiring back to the control.
• If a 10K Indoor Sensor is used, install the Indoor Sensor(s) according to the installation instructions in the Data Brochure D 074
and run the wiring back to the control.
• If a 10K RTU is used, install the RTU(s) according to the installation instructions provided in the Data Brochure D 054 and run the
wiring back to the control.
• If a Zone Control is used, run the wires from the Zone Control to the 371. Refer to the instructions supplied with the Zone Control.
• Run wiring from the other system components (pumps, DHW demand, boiler, motorized zone valves, etc.) to the control. Multi-
strand 16 AWG wire is recommended for all 120 V (ac) wiring due to its superior flexibility and ease of installation into the terminals.
• Run wires from the 120 V (ac) power to the control.
Use a clean power source to ensure proper operation.
STEP FOUR
ELECTRICAL CONNECTIONS TO THE CONTROL
The installer should test to confirm that no voltage is present at any of the wires. Push the control into the base and slide it down until
it snaps in firmly.
Powered Input Connections
120 V (ac) Power
Connect the 120 V (ac) power supply to terminals
Power N — L (3 and 4).
5
4
2
3
N
L
Sys
P 1
Var.
Pmp
Power
1
Sys
P 2