D.1 dual wound motor – Rockwell Automation SA3100 Distributed Power System Drv Config,Program User Manual
Page 135
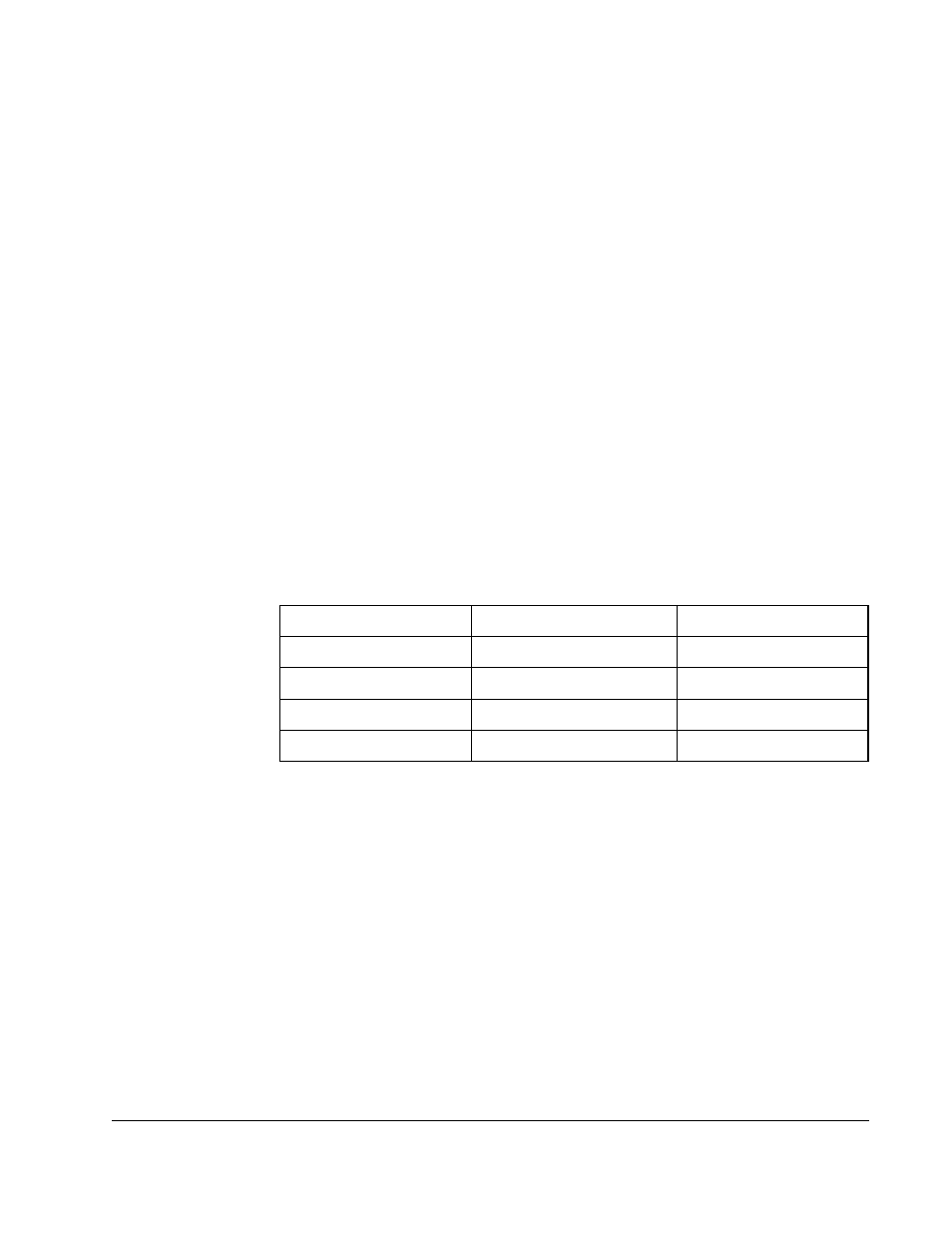
Vector with Constant Power Regulator
D-3
D.1 Dual Wound Motor
D.1.1 Overview
The dual wound motor is a specially designed motor which has two sets of terminals
for connection to two inverters. The outputs of the inverters are connected to the
parallel windings of the motor. This type of motor enables an application engineer to
use a larger horsepower motor than the horsepower of the largest inverter. To enable
the coordination between two SA3100 inverters, both inverters must be connected to
the same UDC card (the A-channel inverter is defined as the master unit). Register
700/1700 bit 14 must be asserted in each inverter.
The drives can be commissioned in the normal fashion, however, the resulting IGN
table from the A-channel inverter will be copied to the B-channel inverter. After
commissioning, both IGN tables are identical for the two drives. The application task in
the UDC will copy registers 217 and 218 from the A-channel inverter to registers 1104
and 1107, respectively.
D.1.2 Handshake Registers
After the inverters have been initially tuned, the VOA enable bit (bit 6 of register 1100)
must be set while the inverters are running. This bit causes the B-channel inverter to
follow the A-channel inverter vector orientation. The B-channel inverter indicates that
it is successfully following the A-channel inverter by asserting the VOA_OK@ bit (bit 7
of register 1200).
The configuration data for the drives is also modified. As mentioned above, the Dual
Winding bit is set in register 700/1700. The value in register 706 is set to 15. The
value in register 1706 is set to 16. The motor nameplate horsepower and current is
divided by two and set appropriately in the configuration registers. Note horsepower is
in watts divided by 10 units.
Table D.1 – Dual Wound Motor Handshake Registers
Register Number
Normal Configuration
Dual Wound
217
RPM Feedback
ID Reference
218
Slip Frequency
Vector Orientation
1104
Auxiliary Reference
Id Reference
1107
-
Vector Orientation