Rockwell Automation 1771-SPI,D17716.5.122 SPI PROTOCOL INTERFACE User Manual
Page 49
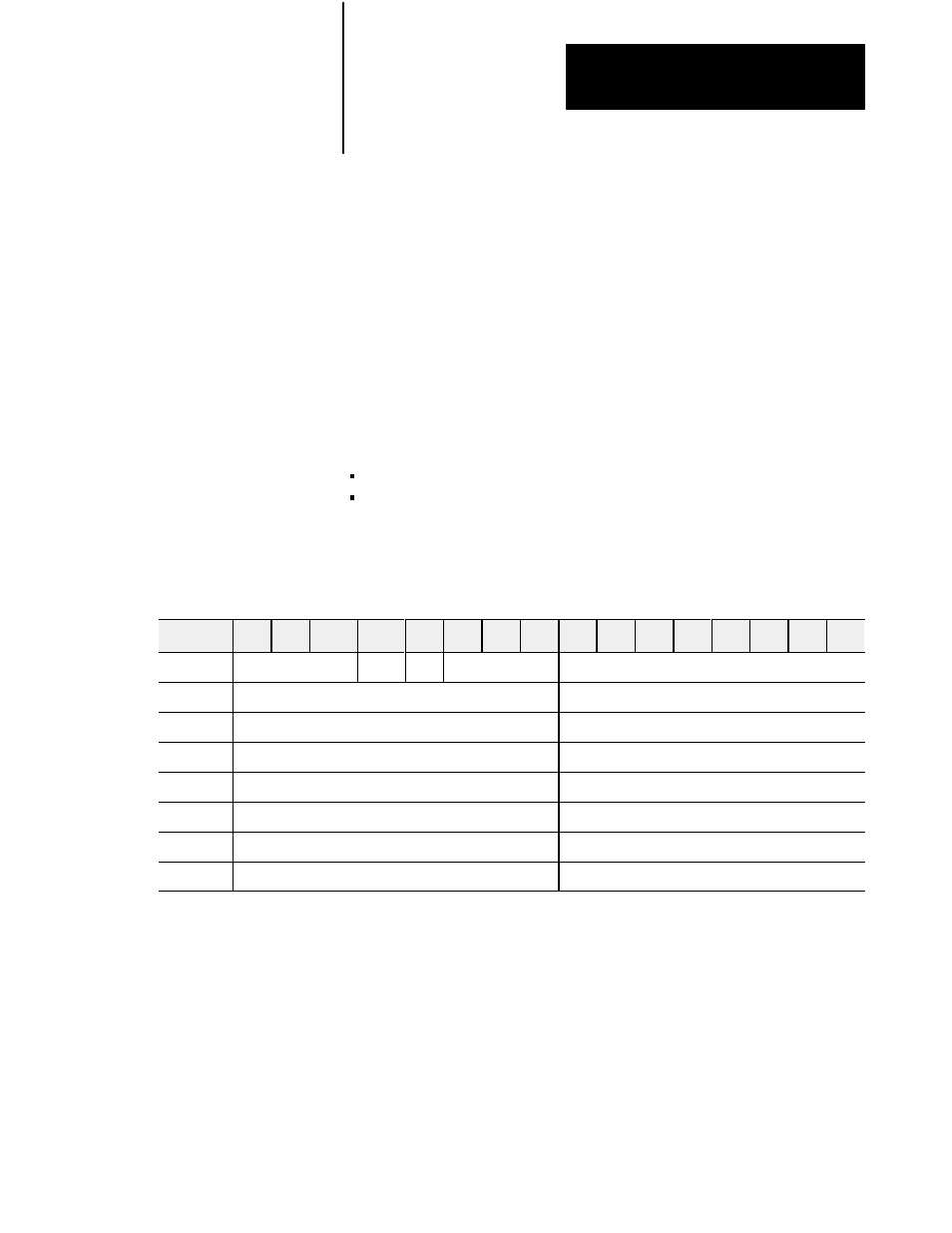
Creating Command and Status Blocks
Chapter 4
4-13
Once you have successfully configured the SPI module with the MCC and
whenever you transfer the CCB to the SPI module, it responds by returning
Custom Configuration Status (CCS).
You must correct any detected errors as indicated by the CCS before you
can transfer data to devices whose configuration has been successfully
stored in the SPI module.
The CCS is returned to the PLC processor by the SPI module. To map the
CCS in your data table, use the same number of words as its corresponding
CCB. We repeat the CCS bit/word map from chapter 3.
Important: When the SPI module detects a fault in the CCB, it returns the
CCS with its status cleared, containing information only in words 1 and 3:
word 1 identifies the device having the invalid CCB
word 3 contains the 5000 series error codes described in chapter 6.
We identify fault diagnostic information in bold print.
CCS Bit/Word Map
Word
15
14
13
12
11
10
9
8
7
6
5
4
3
2
1
0
1
CE
CA
DC
Device ID
2
Number of Numeric Setpoints or 0
Number of BitĆcommand Words or 0
3
Number of BitĆstatus Words, or 5000 series error codes
Number of ASCII Strings, or 5000 series error codes
4
Number of ASCIIĆstatus Strings or 0
Number of NumericĆstatus Words or 0
5
CMD1 (for example, 20) or 0
CMD2 (for example, 49) or 0
:
CMD1 (for example, 20) or 0
CMD2 (for example, 31) or 0
:
CMD1 (for example, 20) or 0
CMD2 (for example, 22) or 0
64
CMD1 (for example, 20) or 0
CMD2 (for example, 44) or 0
Custom Configuration
Status, CCS, to Return
Configuration Status From
the SPI Module