Connections – Rockwell Automation 1756-XXXX ControlLogix Digital I/O Modules User Manual
Page 23
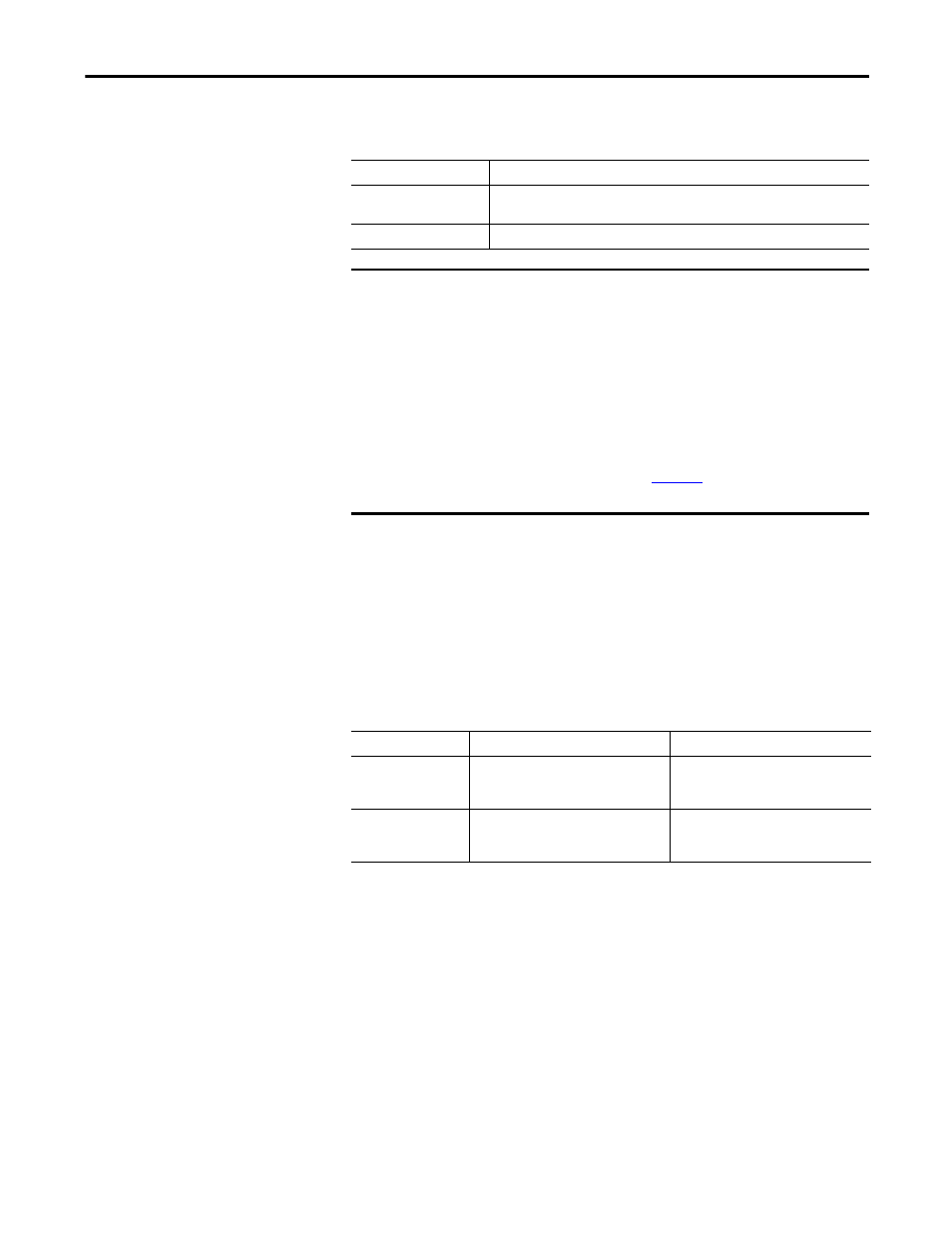
Rockwell Automation Publication 1756-UM058G-EN-P - November 2012
23
Digital I/O Operation in the ControlLogix System
Chapter 2
The table defines some of the delay factors that affect the signal propagation on
an I/O module.
Connections
With ControlLogix I/O modules, a connection is the data transfer link between
a controller and an I/O module. A connection can be one of these types:
•
Direct
•
Rack-optimized
The table lists the advantages and disadvantages of each connection type.
Delay
Description
Hardware
How the module is configured and the variance between the type of modules affects
how the signal is processed.
ASIC
ASIC scan = 200 μs.
EXAMPLE
A typical delay time can be estimated despite the number of factors that might
contribute. For example, if you are turning on a 1756-OB16E module at 24V DC
in 25 °C (77 °F) conditions, the signal propagation delay is affected by these
factors:
• Hardware delay to energize the input (typically 70 μs on the
1756-OB16E module)
• ASIC scan of 200 μs
In the worst case scenario with a filter time of 0 ms, the 1756-OB16E module
has a 270 μs signal propagation delay.
These times are not guaranteed. See
for nominal and maximum
delay times for each module.
Connection Type
Advantages
Disadvantages
Direct
All input and data echo information is
transferred, including diagnostic
information and fusing data.
With more data transferring over the
network, your system does not operate as
efficiently as with rack connections.
Rack-optimized
Connection usage is economized. The
owner-controller has a single RPI value for
each connection.
Input and data echo information is limited
to general faults and data.