Rockwell Automation 1336T Master/Slave Parallel AC Drv User Manual
Page 37
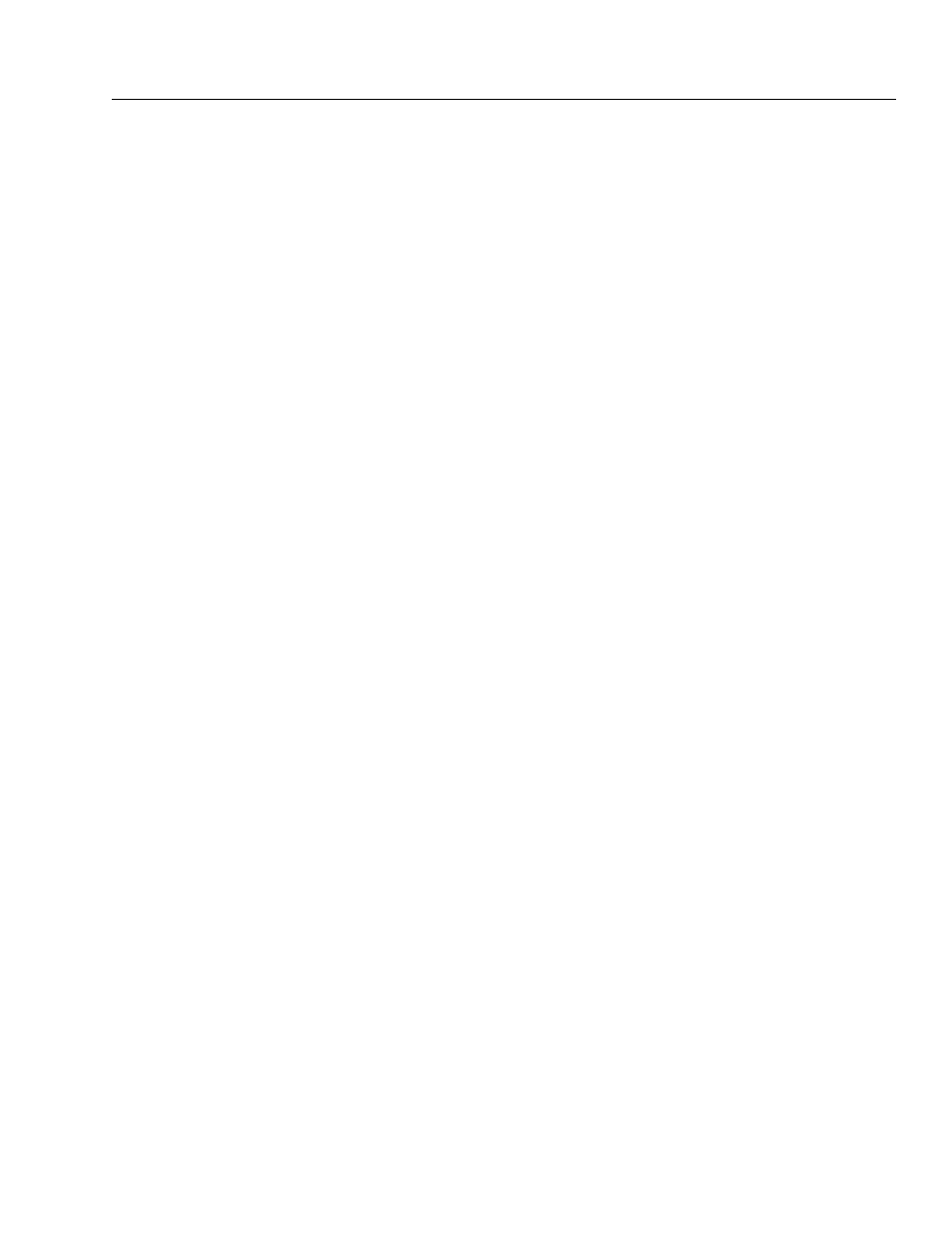
1336 FORCE-5.19 – August, 2000
Startup
3-19
Filter Setup- In most applications, a fixed light filter (P152 = 1)
or a fixed heavy filter (P152=2) will suffice. If needed, a tunable
filter can be implemented.
1. To set up a low pass filter:
a. Set filter select (P152) to a value of 3 which selects
lead/lag.
b.Set filter gain (P153) to a value of 0. (Kn = 1 disabled,
Kn<1 lag filter, Kn>1 lead filter).
c. Set filter bandwidth (P154) to a value greater than or equal
to 10 x the bandwidth of the velocity loop, P43.
d.If you run into backlash noise try setting P152 [Fdk Filt
Sel] to a value of 1 or 2.
A speed error filter can be adjusted, but should only be changed
from the default in very limited cases. The bandwidth (P142)
should be greater than or equal to 10x the bandwidth of the
velocity loop. Simply setting the parameter too low can cause the
drive to become unstable. Experience has shown that a minimum
value for this parameter is in the 50-100 unit range.
2. The motor and load should be accelerated throughout the
complete speed range a few times to ensure that instability
does not occur.
System Integration
1. With a hand tach, verify the actual surface speed of the
section. If software is loaded, adjust PLC roll diameter or
gear ratio information as necessary so that the hand held tach
and any speed displays agree.
Note: The hand tach is not the best device to measure surface
speed, but is a good device to roughly verify calculations. If
the system contains an MMI screen, verify that the screen
is displaying a proper speed, load and torque values.
2. Verify the operation of tension, position, speed override
circuits, or any speed trimming type circuits, and all auxiliary
control loops/helper motors.
3. All input/output signals, master-slave relationships, speed
and load displays, draw and/or load references, and
miscellaneous interactions to external devices/controls
should be verified. Run the section from the operator station
to verify these items.
4. Items that require the process to be operating for tune-up,
such as drooping, should be noted on the “tasks to be
completed” form for this section and filed in the Master
startup Manual.
5. Drawings should be updated for this section to reflect “As
Installed” conditions. Parameters should be saved to
EEPROM and documented on paper (a table is supplied in
the appendix for this purpose). Chart recording response plots
should be filed in the Master startup manual.