Rockwell Automation 1502 Medium Voltage Contactor, 800A (Series D and E) User Manual
Page 17
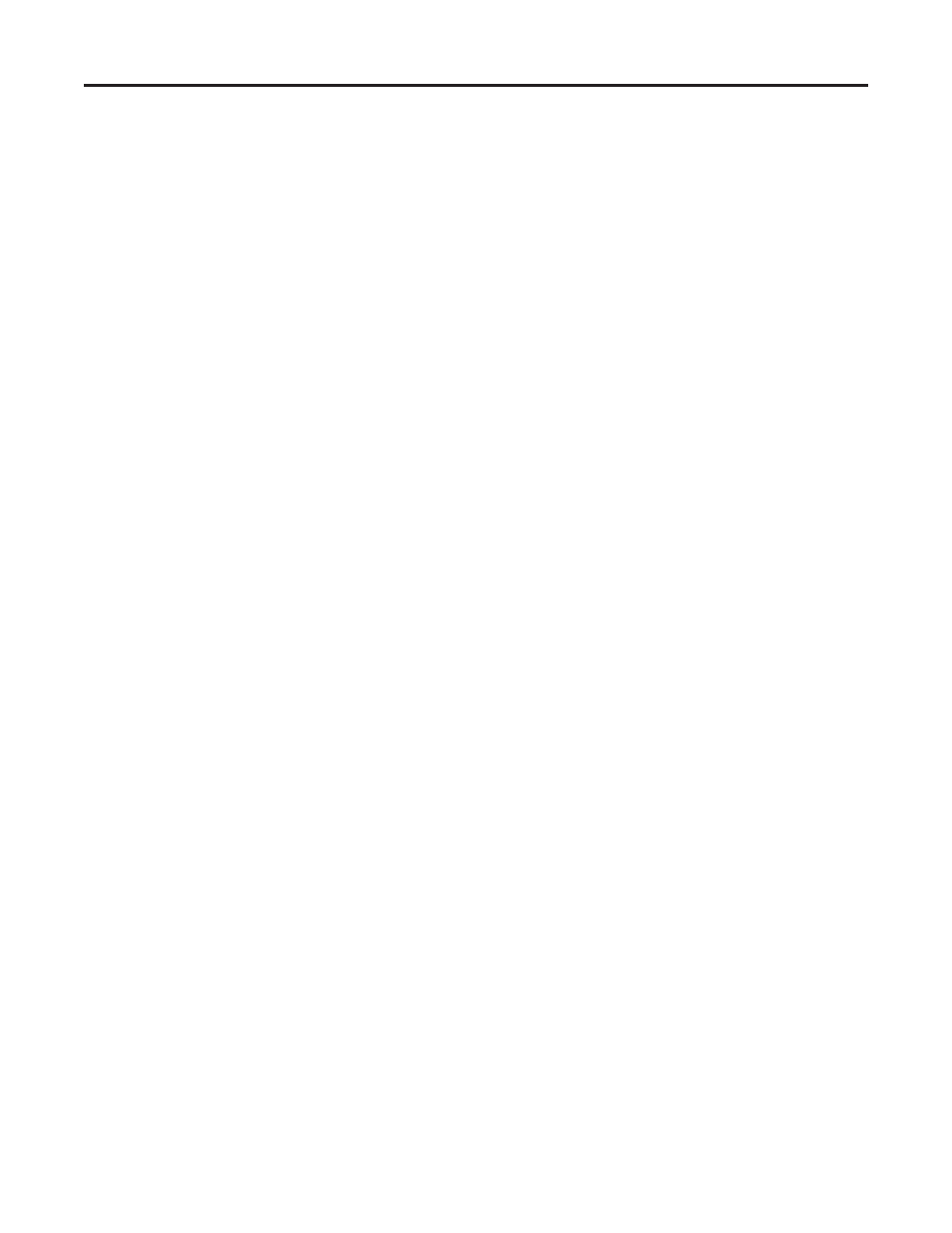
Receiving and Handling
2-5
1502-UM051E-EN-P – June 2013
The allowable leakage current of 5 mA is a maximum for new dry equipment, and is
exclusive of leakage due to test equipment leads. The test setup leakage can be
determined by running the dielectric test with test leads not connected to the
contactor and noting the maximum leakage current. If this value is more than
2 milliamperes, it should be added to the 5 mA limit when testing the vacuum
bottles.
NOTE: Rockwell Automation does not recommend DC HiPot testing because
the values obtained during the test are not a reliable indication of vacuum bottle
integrity.
DC HiPot testing is unreliable due to the occurrence of a phenomenon known
as Cathode Ray Tube Effect. This occurs when one contact of the vacuum bottle
has a deformity, such as a burr or deposit, while the other contact remains flat
and true. This sets up leakage currents which flow from a small surface to a large
surface in one direction and vice versa when the polarity of the tester is changed.
The resultant current is large in one direction which would indicate, incorrectly,
a faulty vacuum bottle.
At best, DC testing will verify vacuum integrity if both contact surfaces are
perfectly smooth. It will not, however, give any indication of the degree of vacuum
since the contact surface can feasibly change with each operation of the vacuum
contactor. AC testing, on the other hand, will provide reliable vacuum integrity
indication. As well, the degree of vacuum within the bottle can be determined by
comparing initial test results to the present readings. Increases in leakage current
indicates a reduction in vacuum within the vacuum bottle.
For these reasons, Rockwell Automation recommends AC testing as the only
reliable method of testing vacuum bottles.
Insulation Resistance Test
Using a 1000 volt Megger, the resistance from phase to phase or phase to ground
shall be greater than 500 megohms.