MTS SWIFT 50 GLP Sensor User Manual
Page 20
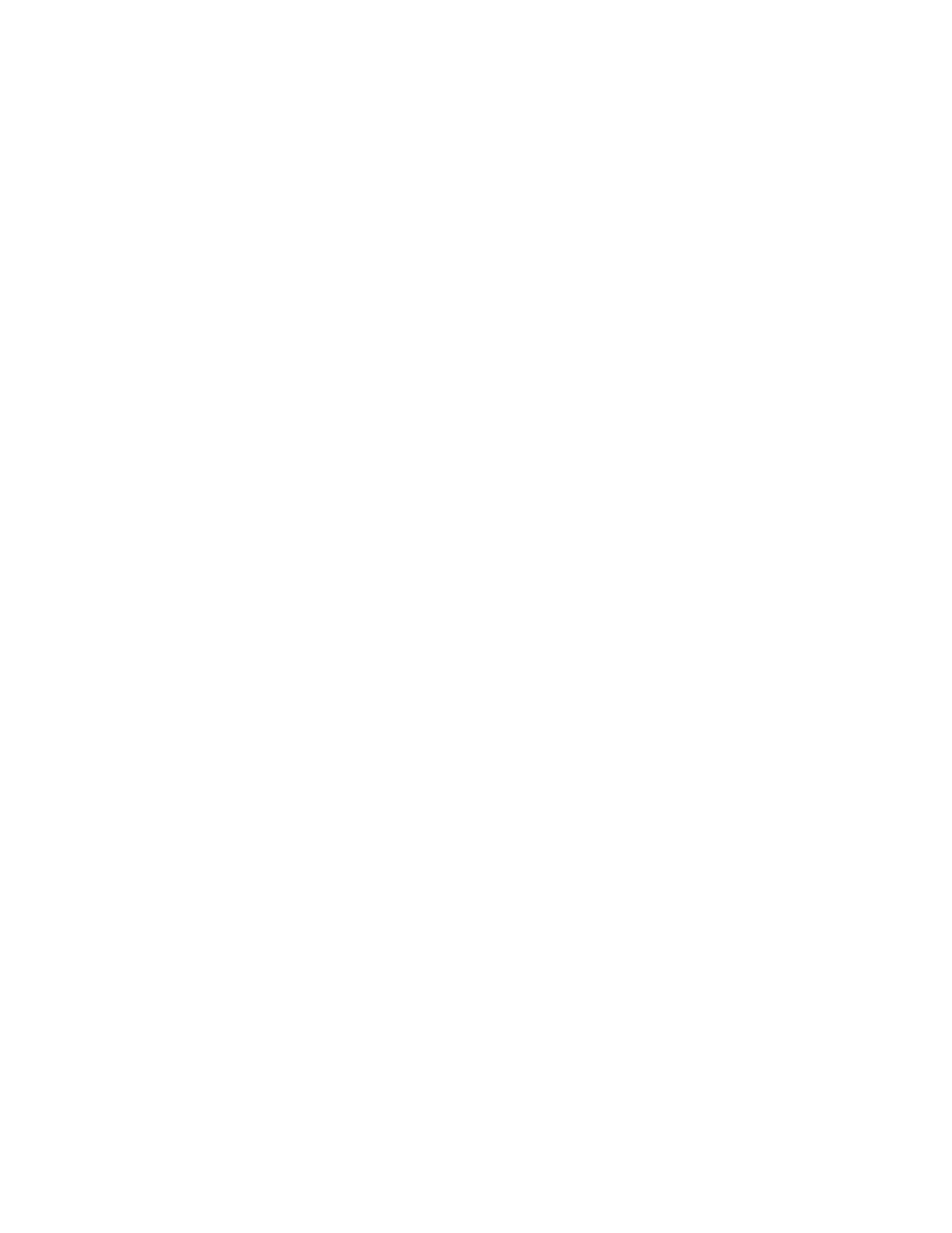
SWIFT 50 GLP Sensors Installation
20
Construction
Hardware Overview
The anti-rotate device should be configured such that no loading occurs to the
slip ring throughout all loading and suspension travel. This means that when you
attach the anti-rotate device to the vehicle, you must consider all possible motion
of the suspension. The anti-rotate device should not bump against the wheel well
at any time; any jarring of the anti-rotate arm will damage the slip ring. For
steering axles, the anti-rotate bracket must be mounted to part of the unsprung
suspension that steers with the tire, such as the brake caliper. For additional anti-
rotate device mounting recommendations, refer to the Anti-Rotate Customer/
User Assembly drawing at the back of the SWIFT 50 GLP Sensor Product
Information manual (MTS part number 100-162-722).
Transducer Interface
(TI)
The TI conditions the power supply, and uses previously stored calibration values
to convert the eight bridge outputs and the encoder signal to six non-rotating
analog outputs (Fx, Fy, Fz, Mx, My, Mz) plus an angle output. The force and
moment outputs have a value of 10 V full scale, unless a different full-scale
output is requested by a customer. The angle output is a 0–5 V sawtooth output.
Additional
components
Additional components that are supplied with your SWIFT sensor include shunt
and transducer data cables, TI power cable, a SWIFT Transducer Interface
Utilities CD or disk, and the calibration file. MTS can also provide a 12 V DC or
24 V DC power converter for use in the test laboratory.